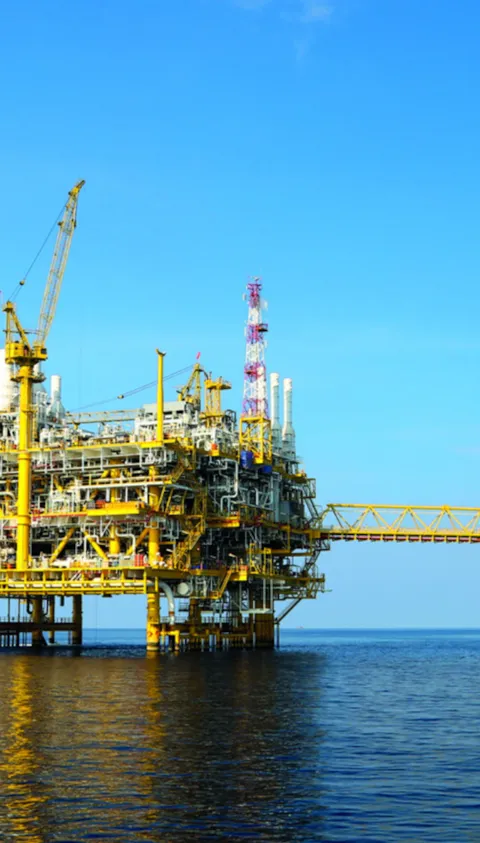
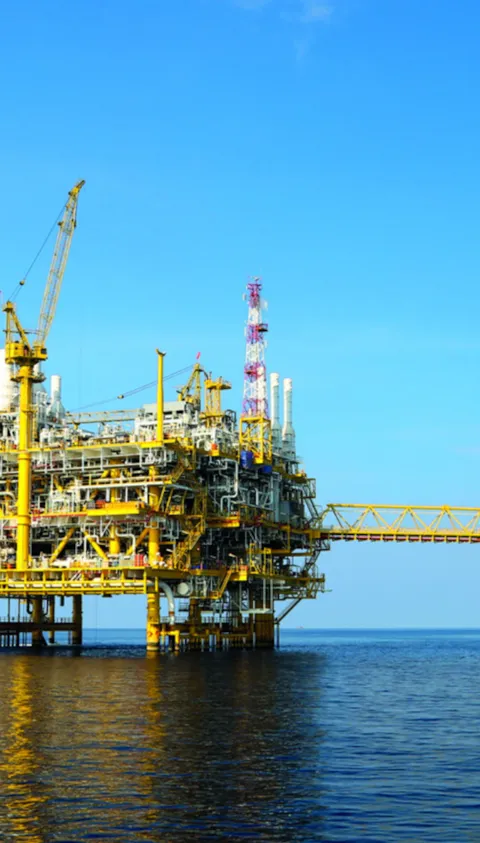
Proving the residual strength of an asset after many years of service is an important part in a life extension project
A key element in the structural integrity assessment is to document compliance with codes of practices and calculate remaining fatigue life. Sesam has all the facets to support owners and engineers to perform the needed structural analysis to document that an asset is fit for purpose for life beyond initial lifetime.
We believe success relies on the ability to have engineering workflows that allow for the re-use of old model data to include modifications, corrosion and environmental changes in a modern and updated structural analysis system as Sesam.
Sesam
Software supporting the structural design during lifetime extension work
DNV has developed Sesam for decades to overcome the challenges owners and engineers are exposed to when doing life extension work of bottom fixed offshore installations like topsides, substations, traditional jackets for O&G, jack-ups, subsea templates and bridges.
The software facilitates a complete and user-friendly process covering all the analysis steps needed to document structural integrity and fit-for-purpose for life beyond initial lifetime. The basis for all analyses is normally the as-built model where modifications, corrosion and changes in environment are accounted for. Sesam has a unique advantage that it can import old models from various sources and convert into a more modern data format allowing for easy modifications prior to performing code checking, fatigue, non-linear analysis and earthquake analysis. The same model is used for all analyses resulting in easy re-design when a model is edited.
The functionality is the same as Sesam for Design and Operation of offshore bottom-fixed installations, but in addition non-linear analysis allowing for push-over (also known as collapse), boat-impact, dropped objects, temperature and explosion are included. Sesam includes advanced technologies that could prove more residual strength of existing assets than legacy systems can do. This in turn can lead to significant cost savings as replacement or costly repairs can be avoided when assessing extended lifetime.
A common challenge is to document satisfactory remaining fatigue life. The fatigue life calculated for the as-built condition has often been based on traditional beam fatigue analysis using parametric stress concentration factors for tubular joints or other welded connections. Sesam offers unique functionalities to easily convert tubular joints from beams to an integrated shell model including a finite element mesh that satisfies DNV-RP-C203 Chapter 4.2 for finding SCF or to do shell fatigue analysis. The use of shell models may prove that costly repairs or modifications can be avoided.
A life extension project requires that member and connection code checks are carried out using the latest editions of typically API/AISC, ISO/Eurocode or Norsok/Eurocode. Sesam supports previous and latest revisions of the codes, and it is seamless to switch between the various revisions.
The model and results from code checking, fatigue and non-linear analysis can be shared with your stakeholders for online collaboration and reviewing.
Together with CFD heat calculations done by KFX from DNV, Sesam also supports time domain non-linear fire analysis to calculate the structural integrity as well as the amount of passive fire protection (PFP). Retrofitting of PFP and corrosion protection (part of Sesam functionality) are often cases to prove during life extension.
Great for:
- Structural design of offshore bottom-fixed installations and their topsides, equipments, flarebooms, helidecks and bridges
- Structural strength analysis inclusive of detailed stress analysis for 3D model data
- Strength analysis (ULS and SLS)
- Fatigue analysis (FLS)
- Earthquake analysis – by spectrum or time domain method
- Non-linear push-over (collapse), boat impact and accidental analysis (ALS)
- Corrosion protection analysis
- Passive Fire Protection analysis in combination with KFX
- Version control of model data and results – and web-based sharing with stakeholders