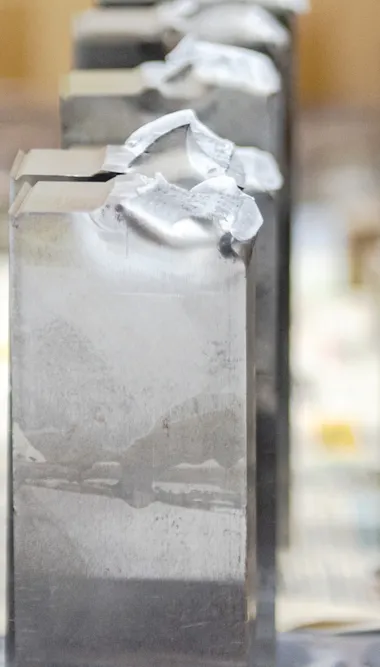
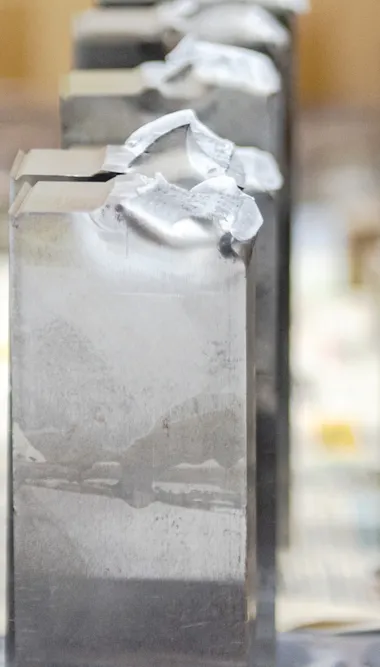
At DNV, we provide a broad range of materials and components testing under one roof to help project stakeholders ensure quality and timely delivery. Our laboratory is accredited to ISO/IEC 17025 for the management system and a comprehensive scope of testing covering mechanical properties, fracture and fatigue behavior, corrosion resistance, coatings, rail tracks, bridge bearings, and calibration services for load cells and pressure gauges.
Over the years, the DNV lab has supported various industry sectors, including oil & gas, maritime, offshore wind, carbon capture and storage (CCS) , hydrogen, railway, bridge construction, and building industries.
We conduct the following testing based on international standards, project-specific test procedures, and/or customer requirements.
Key testing for onshore and offshore infrastructures projects:
- Mechanical – tensile, compression, Charpy impact, bend, hardness
- Fracture toughness – CTOD and J-R using CT, SENB, SENT, segment
- Fatigue - SN, FCGR (fatigue crack growth rate), Paris Curvy
- Corrosion – Pitting, IG, SCC & SSC, EC
- Coating – Adhesion, CD, peel, aging, impact
- Microstructure characterization – CS, SS, DSS, SDSS, Ni-Alloy, Cu-Alloys etc.
- Strength – proof loads, breaking loads, strain gauging
- Bespoke testing – mimic actual operating, or customer specified conditions.
The typical equipment and assets tested for the energy industry:
- Subsea pipeline and riser
- Drilling/well casing and subsea components
- Offshore jacket structure, topside platform, and module
- Process equipment, gasket, and seals
- Offshore wind substation platform and structure
- CO2 and H2 transportation pipeline and storage
- NG/LNG pipeline and facility
- Offshore crane.
The typical components tested for the rail, bridge, and building industries:
- Rail track and weld joints
- Concrete sleepers and bearers
- Railway fastener components
- Mechanical pot bearing
- Laminated elastomeric bearing
- Rebar coupler and connector
- Load cell, transducer, and pressure gauges (calibration).