Published: February 2020
Some 40% of onshore and offshore well fields are in sour service conditions created by the presence of significant levels of hydrogen sulphide (H2S).1 Metallic materials such as carbon steel and weldments can become brittle and crack in sour service environments (Figure 1) due to a combination of chemical, physical and electrochemical factors.
This may lead to equipment failure without warning, consequently affecting asset performance and reliability. These risks can present major technical, operational and financial challenges to operators through threats to health, safety and the environment.
Figure 1: Types of cracking seen in sour environments
|
Achieving safe and efficient operation in sour service environments requires a holistic approach across design, choosing materials, construction and installation. Understanding the basics of sour service, and adopting industry best practices, help to overcome the challenges through smarter design solutions and materials selection, testing, and analysis.
The three key ways to overcome materials challenges in sour gas fields are:
- choosing the right materials from the start
- developing weld flaw acceptance criteria from engineering critical assessment, and
- applying best practice and guidelines to address specific sour service challenges and improve the reliability of assets.
Choosing the right materials from the start
Defining the service conditions of the field is a pre-requisite for selecting the most suitable material. Materials may be selected or qualified by:
- selecting materials resistant to SSC/SCC from the list of qualified materials identified in NACE MR0175/ISO 15156 part 2 (carbon steel) or part 3 (corrosion-resistant alloys)
- qualification of a material by documented field experience, and
- qualification of a material based on laboratory testing.
Industry standards developed over decades assist in materials selection and qualification. In 1975, the first edition of Standard NACE MR0175 established limits of H2S partial pressure above which precautions against SSC are always considered necessary.
In 2003, combined Standard NACE MR0175/ISO 15156 was developed.2 It categorizes the severity of sour service environment into three regions based on the acidity of the water phase and the partial pressure of H2S in gas phase:
- SSC Region one – mild sour condition
- SSC Region two – intermediate sour condition
- SSC Region three – severe sour condition.
In situ acidity as measured by pH is charted against partial pressures (bar) of H2S in Figure 2, which is sourced from NACE MR0175/ISO 15156. A maximum limit on materials strength/hardness is commonly required, and the value of this limit varies slightly between international standards and company/project-specific requirements.
Figure 2: Sour Service – Domain of Application3
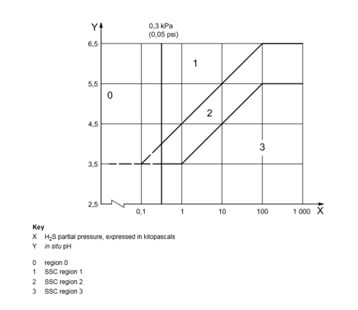
NACE MR0175/ISO 15156 also provides requirements and recommendations for materials qualification and selection for application in a sour-service environment containing wet H2S.
Developing weld flaw acceptance criteria from engineering critical assessment
The threat of cracking inevitably focuses attention on weld imperfections inadvertently generated by the welding process. Most offshore sour service field development projects have stringent flaw acceptance criteria. The criteria may be overly conservative in some cases, however. This can lead to higher weld-repair rates, thereby reducing construction productivity and increasing cost. These impacts are magnified when constructing long-distance, large-diameter transmission pipelines where tens of thousands of welded joints are completed on-site to construct many kilometres of pipeline.
The DNV's Standard, DNVGL-ST-F101 Submarine pipeline systems (2017), provides inspection requirements and acceptance criteria for all girth welds during construction and fabrication of pipelines and risers. However, the acceptance criteria in DNVGL-ST-F101 are not valid for the pipeline and riser girth welds to be used in sour service conditions. Consequently, DNV recommends that project-specific acceptance criteria are developed.
Using overly conservative flaw acceptance criteria can cause high weld repair rates. Low installation rates can potentially lead to impairment of weld properties due to repeated welding and introduction of additional weld defects. These are examples of how design and actual operating conditions can impact some offshore sour service field development projects when workmanship-based criteria is used.
Hence, there is an increase in offshore sour field development projects developing flaw acceptance criteria based on a fit-for-purpose approach backed by scientific engineering assessment.
Applying best practice and guidelines to address specific sour service challenges and improve the reliability of assets
Fracture mechanics and material testing conducted according to best practice and guidelines help to assess welds. DNV's Recommended Practice DNVGL-RP-F108 Assessment of flaws in pipeline and riser girth welds (2019), specifies a procedure of fracture mechanics analysis (often referred as engineering critical assessment, or ECA) and requirements for material testing in the relevant environment.
The advantage of using a fracture mechanics-based analysis approach, supported by testing, is that the different possible failure modes are adequately addressed for all relevant phases, such as installation and operation.
Through this approach, two-tier acceptance criteria can be implemented when the ECA-based acceptance criteria accept a larger flaw size than the workmanship-based criteria do. This will help to optimize construction by reducing installation time without compromising on reliability. If justified, the workmanship-based acceptance criteria can be used to control quality during welding. However, the final acceptance or rejection of the weld can be based on the ECA-based criteria.
Offering an integrated solution to sour service challenges
As understanding of the mechanisms of materials failure in sour services environments grows, DNV GL continues to develop best practice and guidelines to address the challenges and improve the reliability of assets for the industry.
Our experience has assisted clients to solve numerous complex materials and integrity challenges in recent decades. Our sour service test laboratories and test sites in Norway (Bergen), Singapore, US (Columbus, OH) and UK (Loughborough and Spadeadam) provide both standard and bespoke sour-service testing on samples from small to large- and full-scale components. With a global network of subject matter experts, DNV GL is well positioned to help the industry address current and future challenges emerging from sour service field development projects.
References
1 ‘Subsea corrosion and scale’, Yong Bai, Qiang Bai, in Subsea Engineering Handbook (Second Edition), Publ. Gulf Professional Publishing, November 2018, pp 455–487, ISBN 9780128126226
2 International Standard ISO 15156-2 Second edition 2009-10-15 Petroleum and natural gas industries — Materials for use in H2S-containing environments in oil and gas production — Part 2: Cracking-resistant carbon and low-alloy steels, and the use of cast irons. Reference number ISO 15156-2:2009(E). ISO 2019
3 ISO 15156-2:2009