Testing the potential of additive manufacturing
When Wärtsilä Marine Solutions took the decision to utilize additive manufacturing (AM) to create a vital component for an inert gas system, initial production prototypes displayed an unexpected characteristic. In this new field, with new potential, DNV GL’s established expertise was on hand to help.
Additive manufacturing, or 3D printing, has the potential to transform the maritime equipment supply chain. With the adoption of technology enabling printing in metal, vital spare parts and system components can now be printed on demand in locations around the world, including on vessels themselves. The result is dramatically reduced lead times, costs, labour needs, stock requirements and environmental impact (with less logistics and less waste), as well as the complete disruption of traditional business models.
And that’s just the supply side. The impact on manufacturing capability is just as radical. Suddenly the constraints of traditional processes can be broken, with machines bringing previously impossible designs to life through the precise application of layer upon layer of metals. For the frontrunners in maritime manufacturing, such as Wärtsilä Moss AS (a division of Wärtsilä Marine Solutions), it represents a special kind of magic.
Unique potential
“We came up with a new design that could only be realized with AM fabrication,” he explains. “The geometry of the part, the complexity involved in producing it, makes it far too difficult and expensive to manufacture using traditional methods. It can only be brought to life with AM.”
Working with stainless steel and utilizing a fabrication process called selective laser melting (also known as laser-based powder bed fusion (PBF)), the team and their selected supplier – in partnership with the University of South-Eastern Norway – created a unique nozzle, one theoretically capable of greater spray adjustment and performance than anything else on the market.
However, initial quality assessment identified an anomaly. An anomaly no one –not at Wärtsilä Moss AS, the AM supplier or the university – could explain. “About halfway through the PBF printing process a shift occurred, causing a small yet noticeable offset, or ridge, on the nozzle,” Lindløv reveals, adding: “It was only 0.375 mm, but it was unexpected.
“Our question was, how will this affect the integrity of the material and the operation of the part itself? And we couldn’t answer that, so we needed someone that could. That’s why we approached DNV GL.”
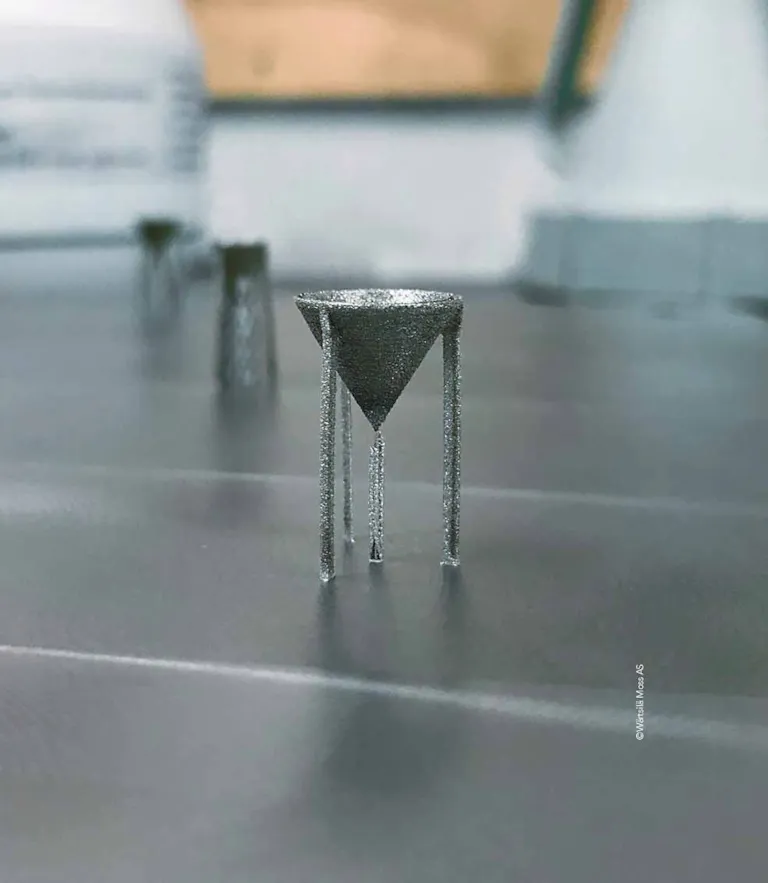
3D vision
Ramesh Babu Govindaraj, Principal Material Specialist, is part of a DNV GL team that has been looking into the potential of 3D printing since 2016. This work has encompassed the initiation of a number of JDPs, pilot studies, innovation papers and, in November 2017, the introduction of DNV GL’s first classification guidelines for the approval of 3D printed products (class guideline DNVGL-CG-0197). In July 2018 this was followed by the class programme for Approval of Manufacture (DNVGL-CP-0267) for AM, and DNV GL has since included AM as an accepted process for ships and offshore (similar to rolling, casting and forging) in ship rule DNVGL-RU-SHIP Pt 2 Ch 1 and offshore standard DNVGL-OS-B101.
Govindaraj sees DNV GL’s role as an enabler for the industry, helping customers understand the potential and realize the value of AM, while supporting, certifying and, in this case, providing expert assessment and testing services for a new generation of printed parts.
“Additive manufacturing is an exciting but new discipline – especially as far as metals are concerned – so caution, patience and expertise are prerequisites for projects,” he comments. “New processes, products and designs also introduce new possibilities for things to go wrong, and we need to take time to understand how these ‘failure modes’ impact upon the integrity of materials and parts. Wärtsilä’s fuel nozzle provided an interesting case in point.”
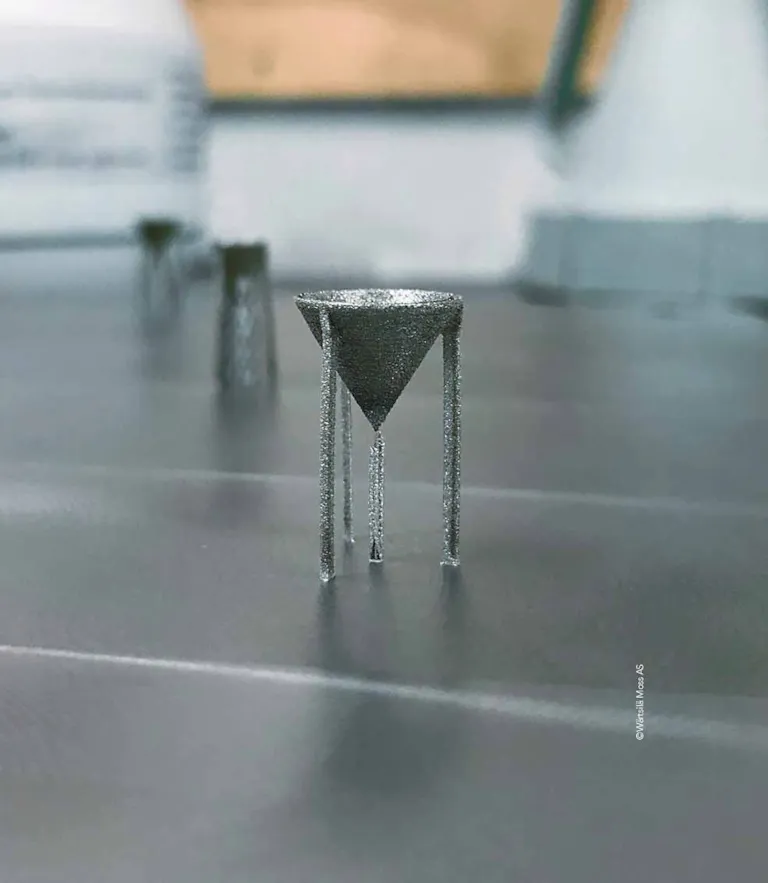
Stringent standards
From the outside, the “offset” in the printed fuel nozzles was largely irrelevant, as machining could be used to create a flush surface. However, if the airflow inside was compromised by the resultant ridge, or the part itself was weakened, the potential consequences could be serious. The DNV GL lab in Høvik has expertise in failure investigation and material technology for both maritime and oil and gas. Here, led by engineer Ole-Bjørn Ellingsen Moe, a team of metallurgical experts carried out a thorough testing programme, including microstructural assessments, hardness measurements, penetrant testing and radiography.
“With critical components, fabricated and designed in new ways, the level of scrutiny required is exceptional,” Govindaraj notes. “This degree of testing is tailored to provide complete insight and total assurance, helping our customers successfully navigate an unfamiliar manufacturing landscape. We are, quite simply, here to help.”
The in-depth examinations delivered a positive conclusion for the Wärtsilä team. The material properties of the nozzle were not significantly impacted by the offset, while the crucial airflow inside was not disturbed.
“In summary,” Govindaraj says with a smile, “the nozzle is fit for purpose.”
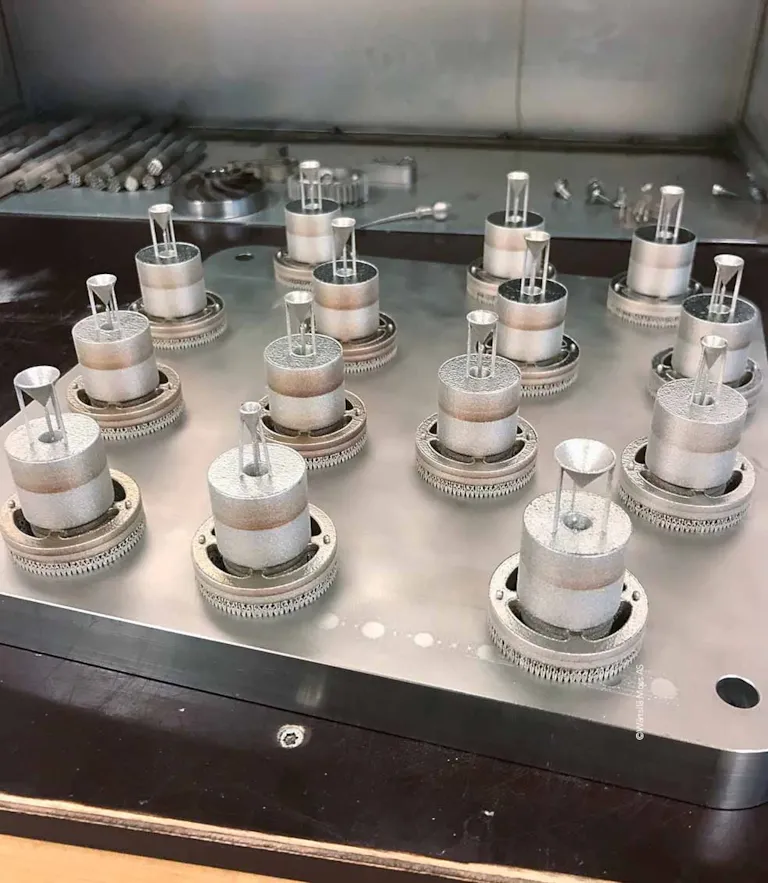
The path to progress
Lindløv and his team are now conducting the first vessel tests with their innovative AM-fabricated nozzle and are hopeful for a successful introduction to the market in the future.
“I am convinced that additive manufacturing is going to have a major impact on the way we do business,” Lindløv notes, “unlocking innovation, enhancing value and delivering tangible benefits to our customers, our organization and our industry. This nozzle is just a first step, albeit an important one, and I’m excited to see where we can go from here.”
We all need help from experienced people when trying new things, and that´s certainly true for additive manufacturing.
His advice for others considering 3D printing is simple: “Jump in,” he says, “the potential is enormous … but make sure you find the right partners to work with. We all need help from experienced people when trying new things, and that’s certainly true for additive manufacturing.”
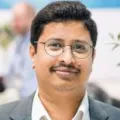
Ramesh Babu Govindaraj
Principal Specialist - Material, Welding & Additive Manufacturing
- Wärtsilä Moss AS
View image copyright information