Successful emissions reduction: Stena Drilling’s breakthrough in energy efficiency measures
Stena Drilling collaborated with DNV’s class independent Maritime Advisory experts to identify the most effective energy efficiency measures tailored to their operations. After successful implementation, Stena Drilling was one of the first companies to be awarded DNV’s Abate notation for their DrillMAX vessel, acknowledging highest standards in energy efficiency in the offshore industry.
With the transition to carbon-neutral fuels likely to take decades instead of years, energy efficiency will be an important piece of the puzzle for decarbonization. In partnership with DNV Maritime Advisory, Aberdeen-based Stena Drilling has achieved significant emissions reductions for their vessels through the implementation of operational and technological energy efficiency solutions.
Energy efficiency a growing priority in oil and gas industry
“There has been a major shift in decarbonization attitudes in the oil and gas industry in recent years,” says Mikael Johansson, Head of DNV Maritime Advisory Sweden and Denmark. “This is largely due to pressure from a range of different stakeholders, including shareholders, charterers, financial institutions and – not least – the public at large.
“DNV is using our experience of 20 years working with energy efficiency measures and management in industrialized shipping to support the offshore oil and gas industry in making this transition.”
Results of the fleet review basis for energy efficiency management plan
Stena Drilling’s partnership with DNV Maritime Advisory began in 2020.
“This started with an energy review of our entire offshore fleet,” says Andrew Calderwood, Energy Performance Superintendent at Stena Drilling. “The findings revealed several operational measures as well as technological upgrades requiring capital investment which could reduce the energy consumption of our fleet, enhancing its environmental footprint. This provided a comprehensive roadmap for improving energy efficiency.”
First goal: Receiving ISO 50001 certification
The initial goal of Stena Drilling was to develop procedures which would enable them to achieve ISO 50001, a cross-industry certification of a company’s commitment to continual improvement in energy management. This started with the development of an energy efficiency management plan.
“We began by understanding and verifying a starting point (the baseline), which future energy efficiency gains could be benchmarked against, then progressed to an energy review where we mapped out relevant systems, and what could be done to achieve energy and emission savings,” says Johansson.
“Once this was agreed with Stena Drilling, we developed an energy efficiency management plan specific to each rig. This plan included a detailed list of measures that were needed to reach their goals, as well as monitoring and control measures, where improvements could be clearly identified and validated.”
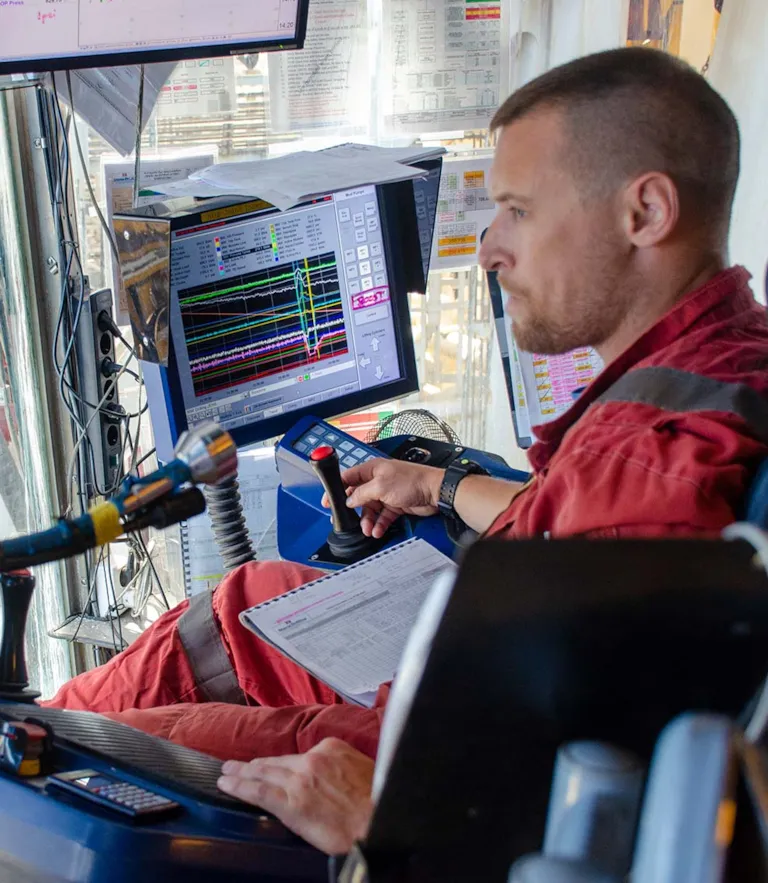
Change in attitudes of crew crucial in achieving operational gains
From the outset, Stena Drilling knew that any energy efficiency measures had to go hand in hand with a change in the attitude and mindset of crew, and the implementation of a cultural shift throughout the company.
Central to this was the framing of the overall initiative, with the environmental impact of actions a powerful motivation.
“We quickly figured out that we were getting much more buy-in from the crew when the results of energy saving exercises were being conveyed as emissions reductions as opposed to fuel savings,” says Calderwood.
In addition to energy efficiency training for all personnel, it was also crucial for Stena Drilling that crew were aware of the company’s goals, and how important their actions were in achieving those goals.
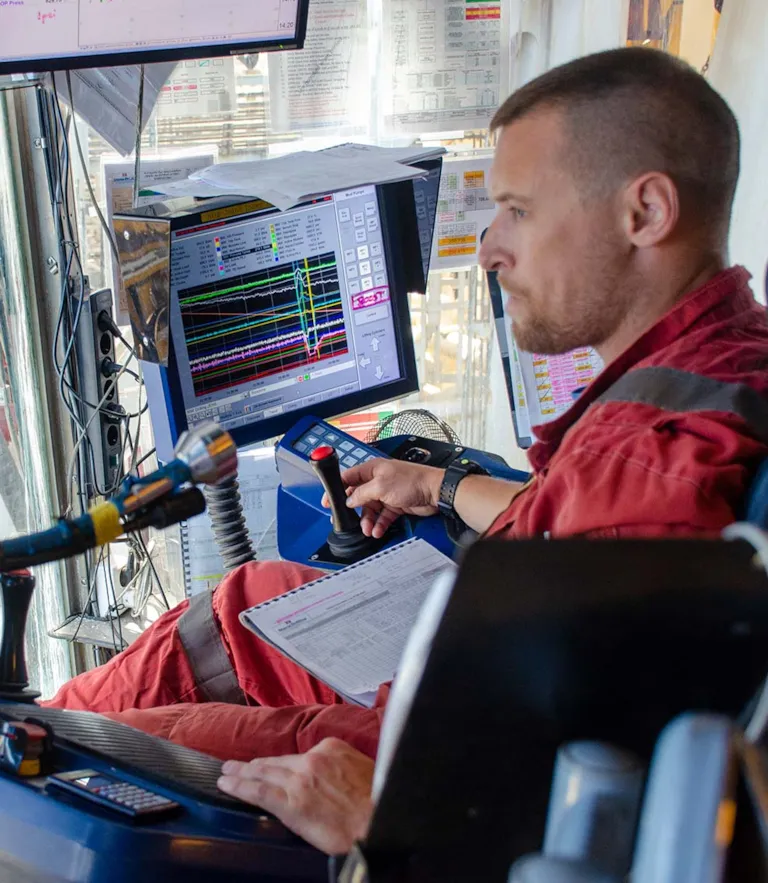
Energy efficiency begins with operational improvements
Energy efficiency usually starts with operational or behavioural changes, where fuel and emissions reductions can be made through procedural amendments, with minimal investment.
Using DNV’s energy efficiency management plan as a guiding tool, Stena Drilling have implemented a number of operational measures. Among a range of things, crew members have been trained to reduce the use of key machinery when it is not needed. This has been aided by the use of smart meters on rigs and onshore.
“These show engine loads, power used by the significant energy users, fuel consumption, emissions and environmental conditions, enabling crew members to make decisions around energy efficiency in real time,” says Calderwood.
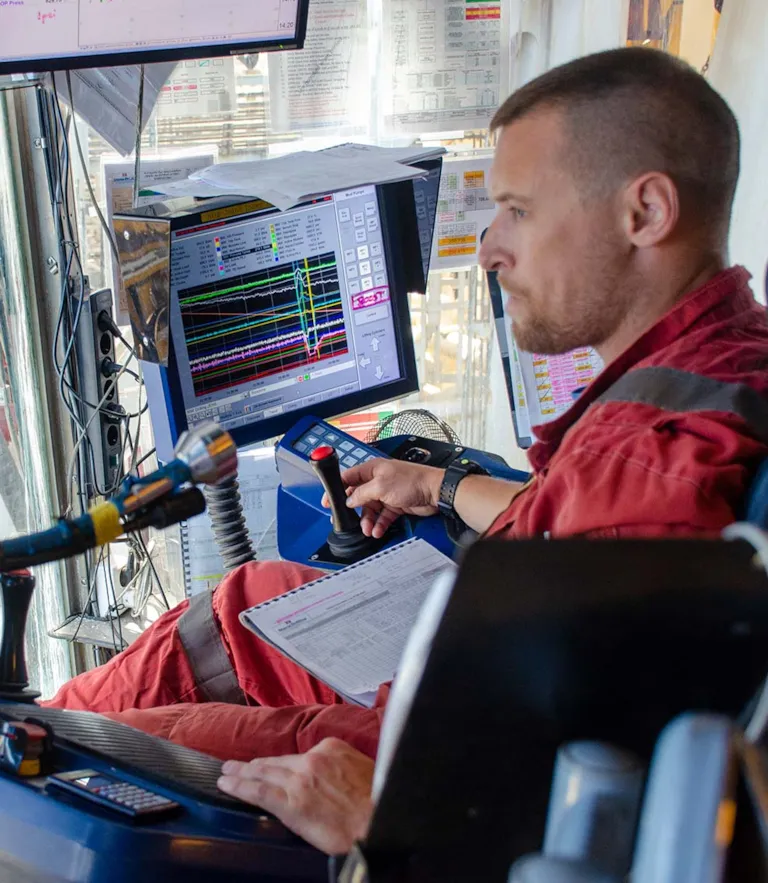
Technological energy efficiency solutions for Stena Drilling
The effects of the cultural changes across its organization and implementing operational energy efficiency measures resulted in emissions reductions of around 5% in the first year of the project. Building on this success, a range of technological improvements were made to take energy efficiency to the next level.
The installation of reverse osmosis (RO) units was the most effective. In combination with the installation of electric lube oil heaters, Stena Drilling was able to either shut down or significantly reduce the use of boilers. This change resulted in a reduction of associated emissions of around 8–10%.
Using a cylinder hoisting rig lift calculator also generated significant energy savings. This consists of a software algorithm for lifting cylinders which analyses all possible combinations of lift pumps and hoist cylinders and advises the driller on the most energy efficient configuration to attain the required hook and load speed.
“This provides the driller with intuitive feedback indicators to promote energy efficient operation,” says Calderwood.
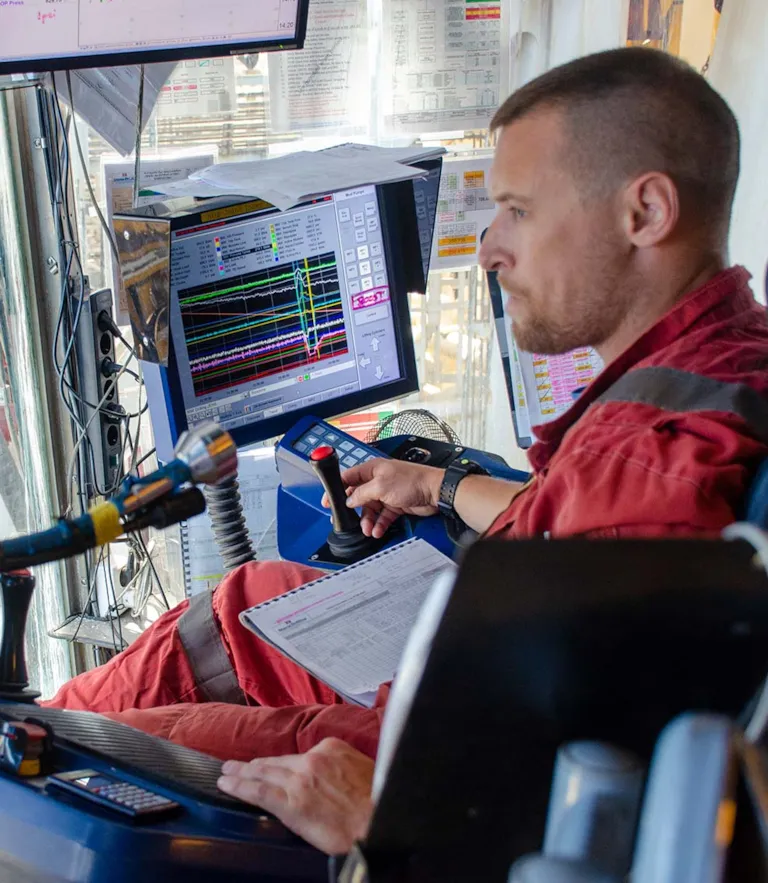
VFD upgrades bring energy savings to next level
Stena Drilling also fitted variable frequency drives (VFDs) to cooling seawater pumps on their Stena DrillMAX and Stena Carron vessels.
“VFDs have their own temperature and pressure sensors. Instead of the pump motors constantly running at full speed, the VFDs control the speed of the pump motors depending on the temperatures and pressures,” says Calderwood.
These improvements are already delivering savings of between 27% and 68% in power usage of high-load pumps, equivalent to an additional emissions reduction of around 7%.
“This has been one of our biggest savings so far and was fully supported by our client in their own effort to reduce their upstream carbon footprint. It was the final push we needed to achieve the Abate notation from DNV,” says Calderwood.
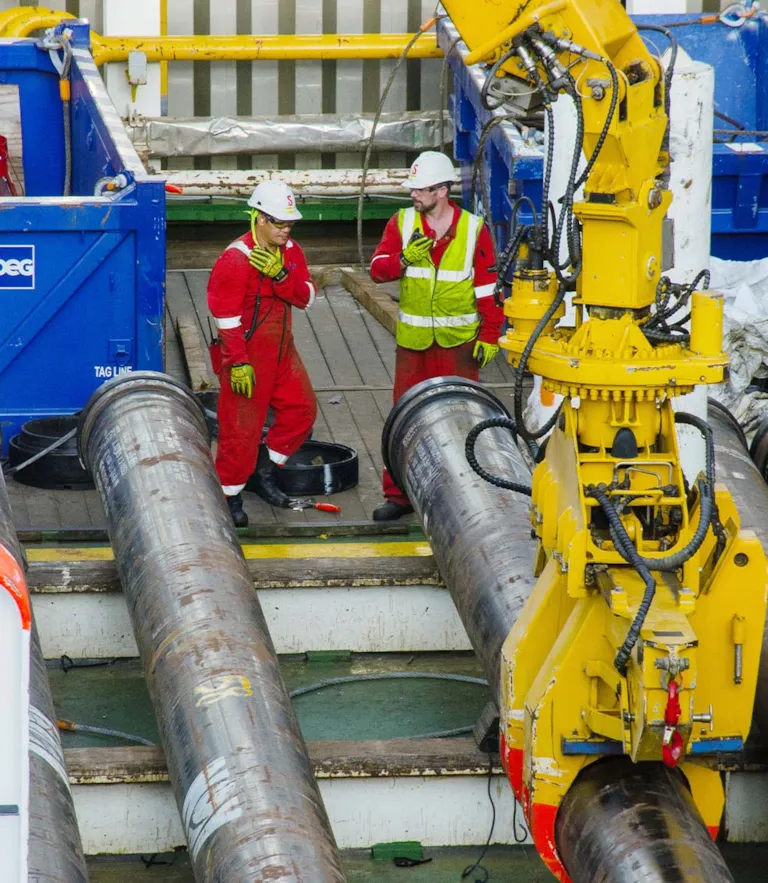
Cooperation with Stena Drilling in developing Abate notation
After building up so much experience in energy management in the offshore industry, Stena Drilling gave valuable input to the development of DNV’s Abate class notation, a measure which demonstrates the highest standards in energy efficiency in the offshore industry.
“Input and feedback from DNV’s customers like Stena Drilling are very important in the development of new class notations like Abate,” says Lars Tore Haug, Head of Section, Offshore Safety and Systems, DNV Classification. “Through close dialogue with their team, we were able to set the expectations and to identify current best industry practice to achieving energy efficiency in offshore vessels. This also helped us to gain a better understanding around what kind of realistic actions a company could take to achieve significant, tangible emissions reductions.”
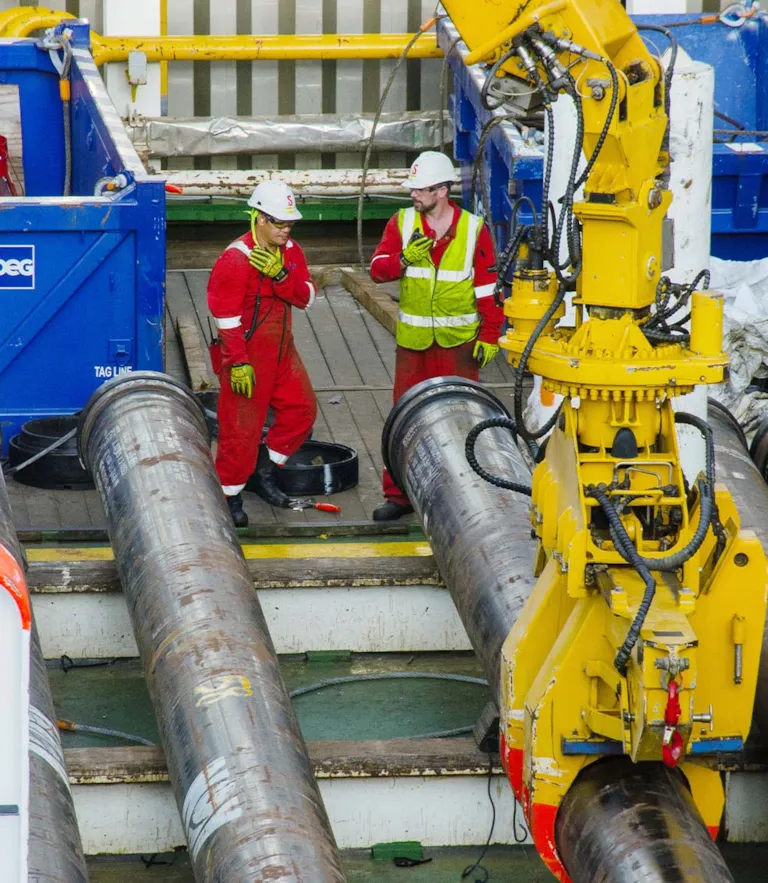
Abate notation proves effectiveness of measures
Following this close cooperation, in December 2023 Stena Drilling’s DrillMAX became the first vessel to be awarded DNV’s Abate notation. Building on the success of receiving ISO 50001 certification for all of its vessels and onshore operations, this is further recognition of Stena Drilling’s pioneering energy efficiency efforts and a clear demonstration of how effective these measures can be.
“This was a key milestone on our journey as it acknowledges the great amount of effort our team and our clients have put into reducing our carbon footprint,” says Calderwood. “It also sets us a target for the future, as having the notation means that we need to maintain our energy efficiency standards.”
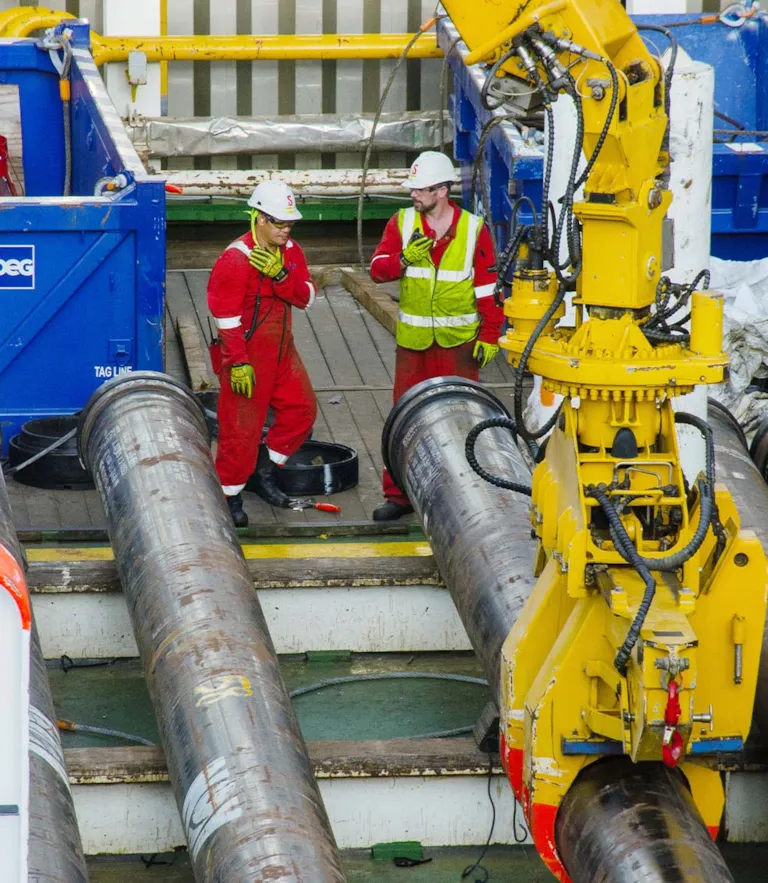
Abate notation provides competitive edge for Stena Drilling
Receiving the Abate notation, in addition to the ISO 50001 certification, provides Stena Drilling with a competitive market edge.
“Our clients have their own ESG targets but they don’t have their own drill ships, so they are dependent on us to achieve emissions reductions,” says Calderwood. “Being able to show them that we are ISO 50001 certified, and now possessing the DNV Abate notation, really helps us in our dealings related to ESG performance.”
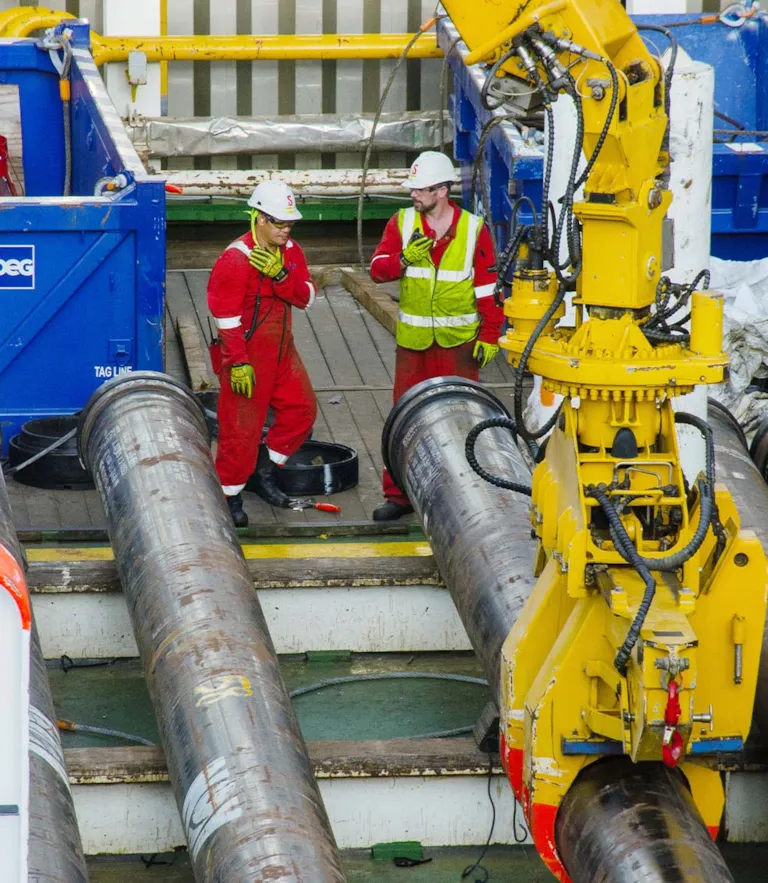
Switch to alternative fuels likely next step
Following the implementation of such a comprehensive energy efficiency plan, Stena Drilling is now exploring how it can further reduce emissions.
“As we start to reach saturation point on technical energy reduction solutions, we will have to concentrate on alternative fuels,” says Calderwood.
“This is likely to begin with the use of synthetic diesel fuel oils. They can be introduced without major engineering work and only a percentage needs to be added to conventional fuel oil. Of course, the ultimate goal would be to use 100% when stocks allow.”
Stena Drilling has also conducted feasibility studies on the potential use of green methanol and green ammonia and could use these in the future.
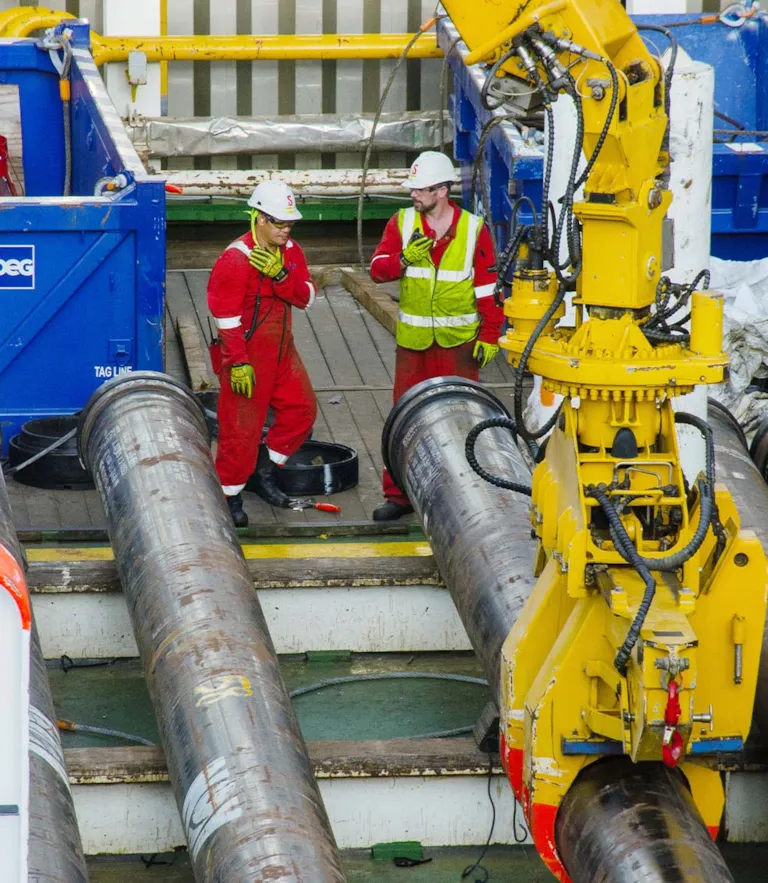
Expanding DNV’s Abate notation to other vessels
Further measures should also see other vessels in Stena Drilling’s fleet being awarded DNV’s Abate notation.
“As we continue to make energy efficiency gains, this will be the next logical step for us and we look forward to more cooperation with DNV in the future,” says Calderwood.
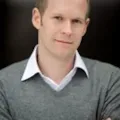
Mikael Johansson
Head of Maritime Advisory, Sweden and Denmark
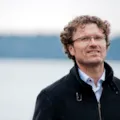
Lars Tore Haug
Head of Section, Offshore Safety and Systems, DNV Classification
- Stena Drilling
- Stena Drilling/JACMAC
- Stena Drilling/Michal Wachucik/Abermedia
View image copyright information