Raising the baseline for ULCV
MSC’s 23,000 TEU newbuildings not only set a new benchmark in their size, but embody four decades of container ship experience and some new thinking too.
With the order of eleven new 23,000 TEU vessels, MSC Mediterranean Shipping Company set a new record for the world’s largest container ship by capacity.
Construction of the ships is split between Samsung Heavy Industries, which will build six of the vessels, and Daewoo Shipbuilding and Marine Engineering, which will build the other five. On delivery in 2019 and 2020, they are expected to replace a significant number of 13,000 and 14,000 TEU vessels due to come off-hire in the near future, rather than add to MSC’s overall capacity.
The main driver for ordering bigger vessels is to reduce the energy needed to transport each individual container. More energy efficiency lowers costs and helps to minimize CO2 emissions, which improves profitability and reduces the environmental impact of global supply chains.
They bring other savings too. Each newbuilding can carry around 3,000 TEU more than MSC’s current largest ships. Multiplying that by the eleven vessels in the newbuild programme gives an overall capacity in excess of more than two of the smaller ships being phased out. The marginal cost of building bigger vessels is much less than building additional ships.
Can ships grow larger still? According to MSC’s manager for the newbuild programme, Giuseppe Gargiulo, the answer to that depends on your perspective. “Technically speaking there are no fundamental physical constraints, and from an operational point of view, a commercial case could certainly be made. The barrier, however, is shore-side infrastructure. We are approaching the maximum size that ports can handle.”
The extra capacity on the newbuilds was obtained by extending the vessels’ width and increasing the number of tiers on deck. DNV GL played a significant role in the plan approval and confirming the structural integrity of the design by performing the strength calculations using finite element analysis and other tools. Gargiulo notes the vessels are designed to withstand the heaviest North Atlantic storms.
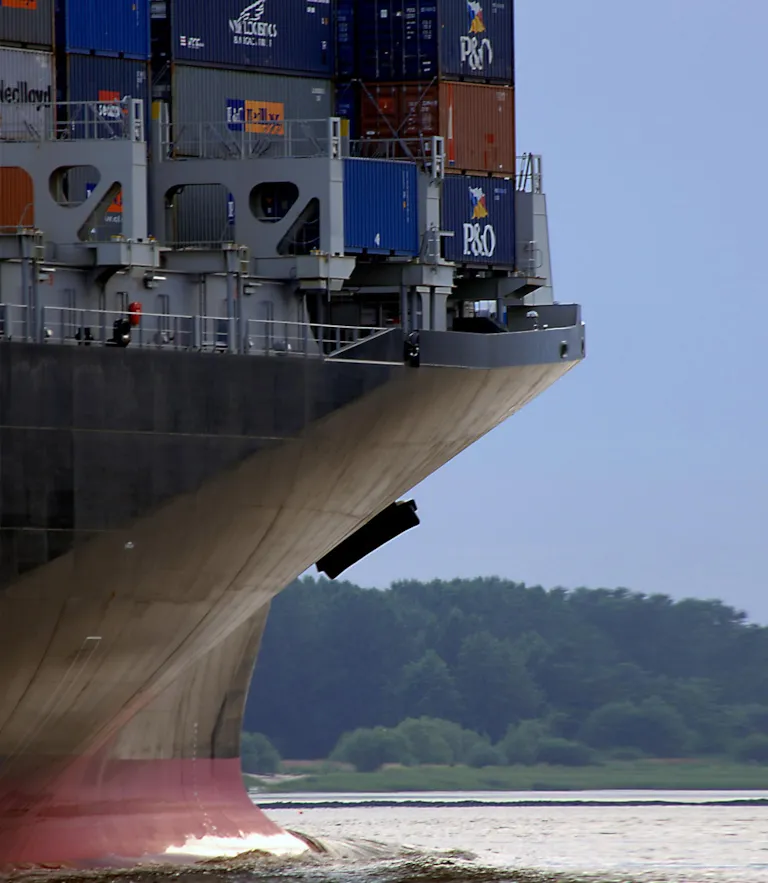
Propulsion efficiency
MSC opted for a single rather than twin engine configuration. Each newbuilding will be equipped with a MAN B&W 11G95ME-C9.5 main engine. MAN Energy Solutions will also supply the vessels’ gensets. The engine is distinguished by an ultra-long stroke that lowers the optimum engine speed and allows the use of a larger, more efficient propeller.
The new ULCSs also feature an air lubrication system. An air blower passes tiny bubbles continuously beneath the ship’s hull so that, in effect, it is sailing on a blanket of air. Despite the energy needed to generate the bubbles and additional complexity, the reduced friction translates into significant fuel savings and a 10–15 per cent net reduction in CO2 emissions. A specially designed bulbous bow yields further savings.
While the newbuilds are LNG-ready, they will initially burn conventional HFO and use exhaust gas cleaning systems (EGCS), built and operated to IMO standards, to provide a safe and practical way to minimize emissions. Gargiulo says the approach has been relentlessly pragmatic. “In our view, the global support infrastructure for LNG is still lacking, whereas the EGCS technologies provide an immediate solution for meeting IMO’s sulphur cap coming into force in 2020.” However, he never says never: “We have not ruled out incorporating LNG into our fuel strategy for the future and we remain open to a variety of alternative fuel sources and propulsion technologies.”
In another feature targeting emissions, MSC specified that the vessels can cold-iron – that is to say switch to a shore-based power source when in harbour, thereby allowing the on-board generators to be shut down. This eliminates virtually all at-berth ship emissions. The company was an early adopter and strong advocate of shore power ever since the technology was pioneered in California, USA, notes Gargiulo. Its implementation on the current newbuilding programme earned it Shore Power notation from DNV GL.
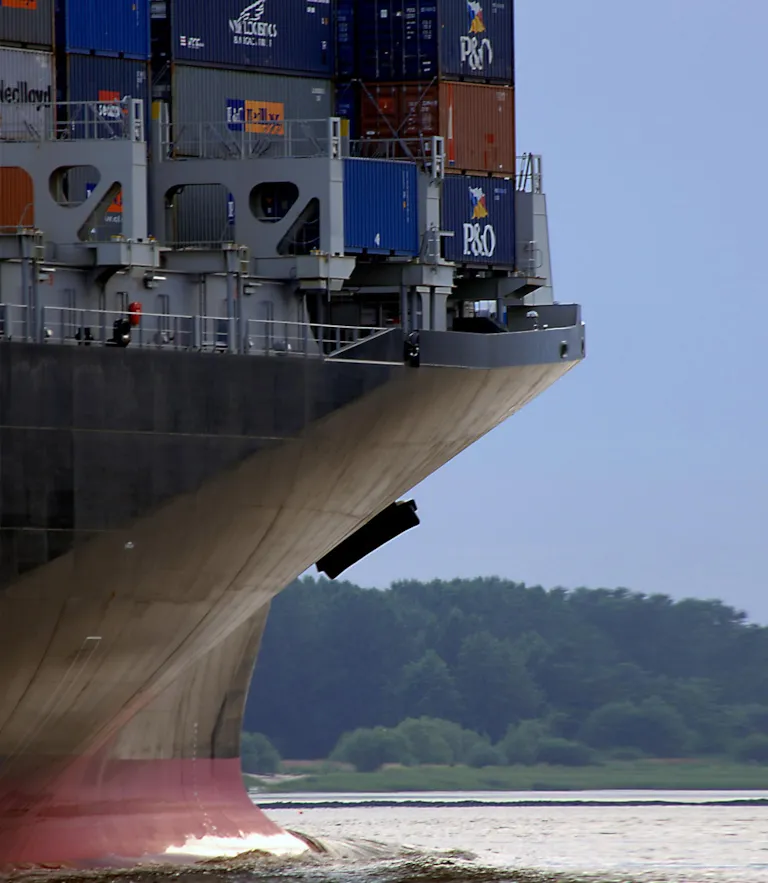
Cargo management
While paying careful attention to engine arrangement, propulsion train and hull form is important, Gargiulo warns against becoming obsessed over vessel specification. “Engineers have a tendency to become fixated on individual components. The danger is they lose sight of the bigger picture. The low-hanging fruit for reducing fuel consumption have been picked. In previous decades, savings of 4–5 per cent were possible, but today the improvements are marginal.” MSC is increasingly focusing its efforts on cargo management, both at ship and fleet levels, where, says Gargiulo, there are still considerable gains to be made. For instance, devising a better lashing system lets ships carry more containers but perhaps more significantly permits greater flexibility in cargo arrangement.
Empties can be carried on upper tiers, which speeds up loading and unloading. Shorter turnaround times mean vessels can save fuel by steaming more slowly. Stowing containers on higher tiers means the vessel floats higher in the water, which reduces friction. “These sorts of optimization have an indirect but not insignificant impact on fuel consumption. We’re approaching the problem from a different angle.”
One challenge is that vessels with a larger beam generally have a larger metacentric height (GM). While a larger GM implies greater initial stability against overturning, it can lead to higher lashing forces and shorter rolling periods. MSC obtained DNV GL’s LC notation through using special software to calculate these forces and manage the consequences on vessel behaviour. It also fulfilled the requirements for the Route Specific Container Stowage (RSCS) notation, which allows for increased stowage flexibility in certain trading areas and further improves cargo carrying capacity.
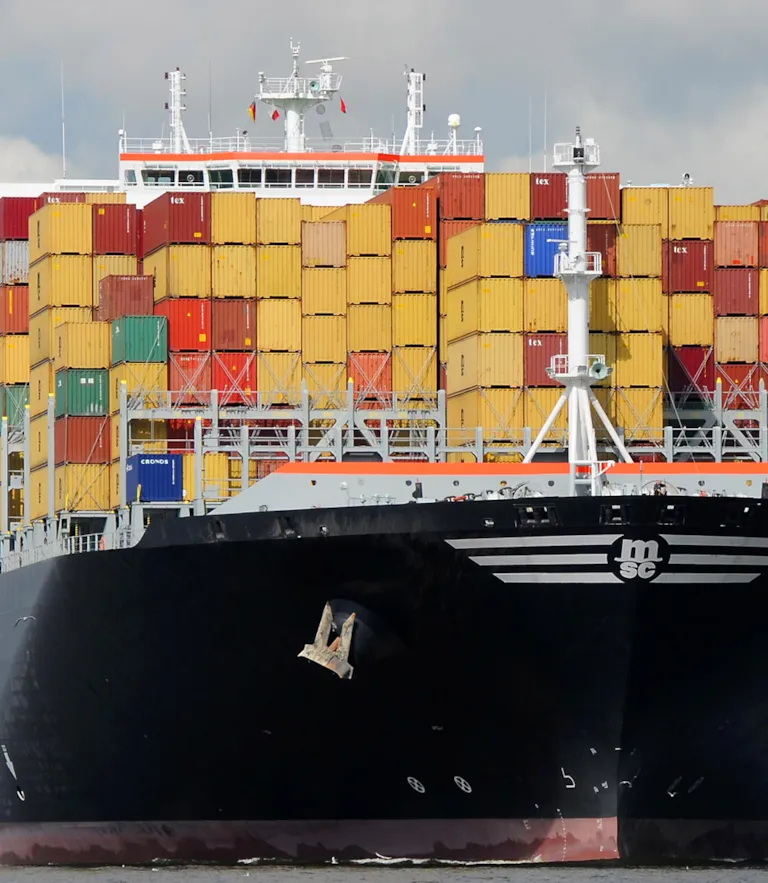
Fire safety
MSC has worked tirelessly on fire safety. Recent years have seen a spate of container ship fires across the shipping industry. MSC has already significantly exceeded the mandatory SOLAS requirements in relation to this topic. It has invested in advanced early warning systems and installed equipment to control and cool down any fires before they have a chance to escalate. Gargiulo likens the aggregate effect of these adaptations to each ship carrying its own firefighting tug. Apart from reducing the risk to life and to cargo, tackling fires early improves survivability and increases the likelihood of a stricken vessel reaching a safe port under its own steam.
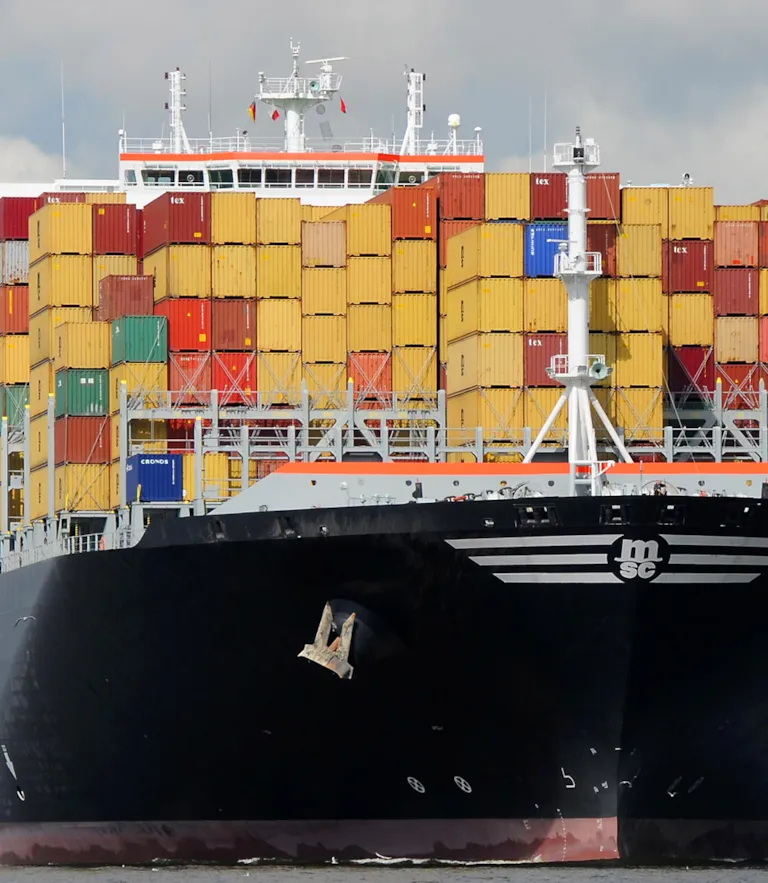
Fostering innovation for container vessels
The newbuilds, says Gargiulo, are “the distillation of 40 years’ experience”. While market dynamics may change every few years, triggered by shifts in the wider economy and global politics, MSC has consistently managed to find ways to adapt its ships and its business to weather these ups and downs.
Gargiulo ascribes this adaptability to the company’s hands-on approach to vessel operation. He explains: “When our newbuild teams aren’t working on new ships they are involved in the dayto-day issues that arise on existing tonnage. This exposure gives them a better grasp of challenges and the opportunity to notice things that might otherwise be missed.”
It results in cross-fertilization of ideas and knowledge spill-over – precisely the conditions needed to spark new ideas. Gargiulo finds it hard to imagine such innovation arising only from reviewing monthly KPI reports on fleet performance.
In this way, the current newbuild programme drew heavily on the experience MSC gained from its 19,000 TEU class ships. Although they have a smaller beam, Gargiulo says much of the know-how was transferable. “Operation of our 19,000 TEU vessels has undergone considerable refinement over time. Most of those improvements are applicable to the 23,000 TEU vessels, so we’ve carried it across. We are starting from a more advanced baseline.”
Diego Russo, Principal Surveyor at DNV GL, believes MSC has demonstrated remarkable ingenuity in this newbuilding programme. “Finding solutions to the challenges of building vessels on this scale requires a mix of practical experience and new thinking in order to bring numerous design, operational and commercial demands into equilibrium.”
He added that the vessel operator’s collaboration with DNV GL emerged from a need to manage and mitigate the risks that inevitably arise from such innovation. “The cooperation between MSC and DNV GL has grown in line with the size and number of new vessels being built in Korea. Everyone involved in the programme – including owner, shipyards, class and other stakeholders – gained valuable experience from the collaboration as they worked towards implementing these innovations, which together set a new milestone in container ship design.”
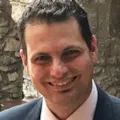
Diego Russo
Global KAM / FiS Team Leader / Principal Surveyor