Promoting more robust DP power systems with closed bus-ties
Industry adoption of closed bus-ties to connect dynamic positioning and other power systems has been hindered by concerns over failure propagation, despite benefits like reduced emissions. An updated recommended practice from DNV can now support the wider adoption of robust, safe and fuel-efficient systems.
Power system redundancy is a critical factor with dynamic positioning (DP) systems for ship and offshore units, such as drilling rigs and shuttle tankers, to ensure station-keeping is maintained in the event of the failure of power components. A revised recommended practice issued by DNV can now facilitate the wider adoption of closed bus-ties for the connection of DP power systems in line with recent technological developments to support more robust and fuel-efficient systems.
Open-bus redundancy measures
Class requirements for DP system redundancy have traditionally been set up for the safest mode of operation. This set-up focuses on the use of open bus-tie breakers to separate redundancy groups of gensets and thrusters in a power system configuration. These circuit breakers isolate faulty parts from healthy sections in the power system during faults, such as a short circuit or overload. They prevent failures from affecting the entire system and ensure alternative power sources remain operational.
Optimized power-sharing in closed-bus operation improves energy efficiency
Closed bus-ties that enable electrical power to be transferred between power systems belonging to different DP redundancy groups have previously been perceived to have a higher safety risk due to the potential for failure propagation across a common power system.
But as the maritime industry navigates decarbonization and rising fuel costs, closed bus-ties have emerged as a viable solution to enhance energy efficiency. These allow the integration of DP power systems and reduce the number of gensets that need to run simultaneously. This leads to optimized power-sharing, reduced fuel consumption and emissions, fewer engine hours, and lower maintenance costs. Additionally, a system with active and reactive power-sharing across bus ties can mitigate and reduce the consequences of certain failure modes.
Leveraging electrification and digitalization with closed bus-ties
“Closed bus-ties for DP power systems have therefore become increasingly relevant for a range of vessels in different segments as there is now an overriding incentive to minimize the inefficient use of lightly loaded diesel generators to provide redundancy (spinning reserve) amid the prevailing trends of decarbonization and digitalization,” says DNV’s Senior Principal Specialist in DP Systems, Aleks Karlsen.
“The benefits of electrification technologies such as battery hybrid power and energy storage can be fully realized with closed bus-ties, which can also better facilitate digitalization, remote control and autonomous operations when a robust system is in place.”
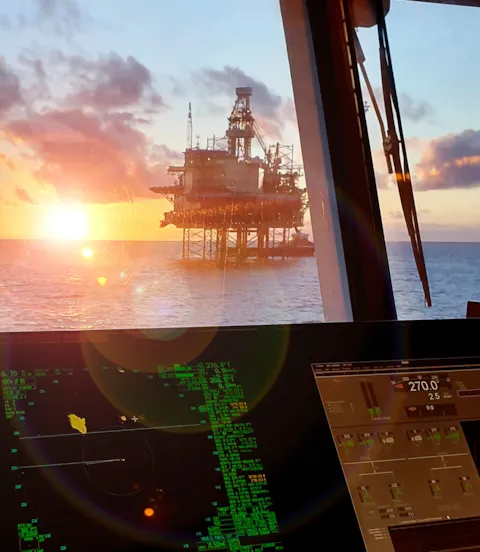
Widespread adoption and enhanced safety of closed bus-tie technology
Consequently, closed bus-ties have seen wider application, especially on dynamically positioned units, over the past 10 to 15 years. The trend is typically led by energy majors seeking to utilize them on offshore drilling rigs, followed by increasing uptake on offshore support vessels such as platform supply vessels and construction support vessels, as well as shuttle tankers. The technology is also being taken on board by other segments like cruise.
To counter failure risks in DP power systems, equipment suppliers have developed closed bus-tie systems with improved functionality and safety barriers. “We have reached the point today where the technology is sufficiently mature to implement closed systems provided they are properly designed and operated according to appropriate minimum standards for safety and robustness,” Karlsen says.
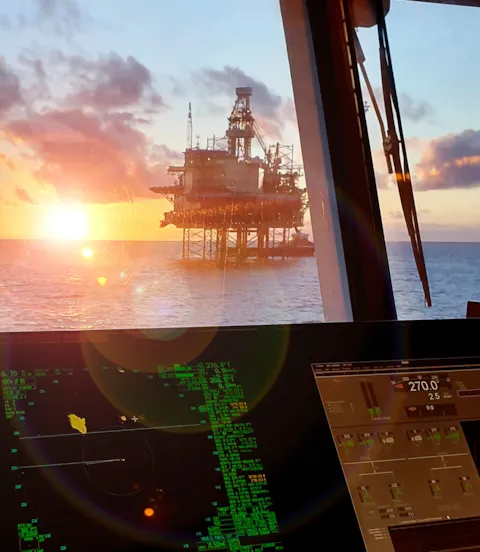
Revised recommended practice ensures higher safety standards
In response to recent technological advancements and learnings, DNV has revised its existing recommended practice (RP) document RP-0591, focusing on “Redundant dynamic positioning systems with closed bus-ties”.
Karlsen says DNV’s development of the revised guidance is “motivated by a desire to utilize modern technology to provide the industry with efficient and environmentally friendly systems without compromising safety”.
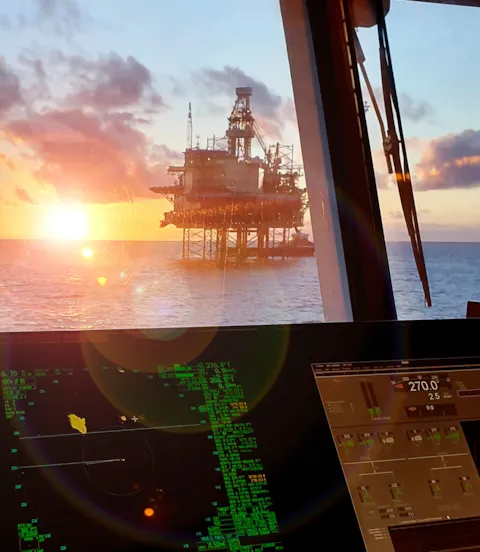
Clarifying measures for redundant DP systems with closed bus-ties
“The revised recommended practice is intended to clarify the measures that need to be implemented to achieve the integrity level required for redundant DP systems operating with closed bus-ties,” he explains. “It provides a new updated framework for robust implementation of closed bus-tie systems that can take advantage of available technology and thereby leverage the benefits for decarbonization and digitalization.”
The updated RP covers a wider scope of closed bus-tie system arrangements and includes the new closed bus-tie qualifiers CB, CBS and CBT, with additional technical, assurance and testing requirements for a broader range of redundant DP class notations, as well as guidance on DC power systems and battery hybrid DP systems.
DNV’s Senior Principal Engineer – Electrical Systems Jon Ole Overrein believes the updated RP could be a big step towards gaining industry acceptance for upgrading DP3 systems typically used on drilling rigs to closed bus-ties.
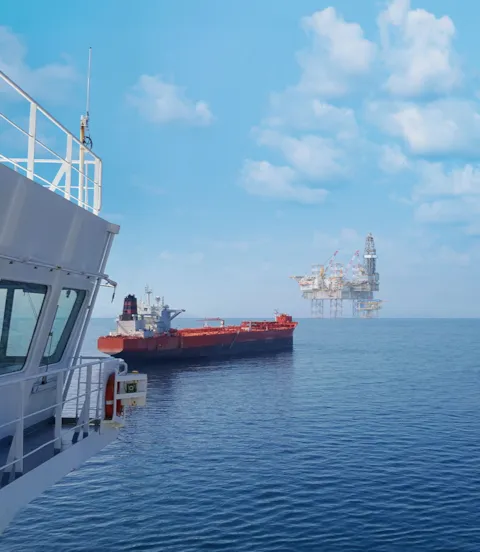
Protective safety barriers in place
Steven Cargill, Technical Authority for Dynamic Positioning, Marine Risk Advisory at DNV, points out that switching open with closed bus-ties is not a case of “replacing a perfect system with an imperfect one”, as similar failures can also occur with open-bus DP systems.
He explains that partial blackouts can occur more frequently with open-bus systems in common failure modes, while experience shows that these are also vulnerable to complete blackouts and loss of position. Such failures may be due to the fact that available equipment used in redundancy mode with open-bus systems may not run or operate to specifications, he says.
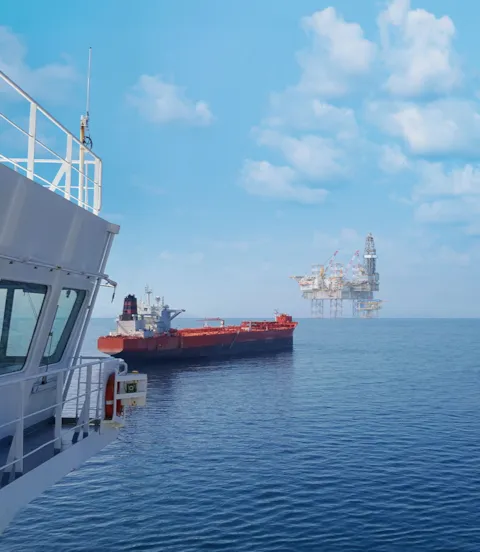
Safety advancements can be applied to all redundant DP systems
In recent years, new and improved technical solutions have been developed to detect and disconnect faulty systems and components, and provide better safeguards against failures, based on experience with fault tolerance on DP systems and other types of vessels using closed bus-ties. These solutions have been largely applied on DP3 systems.
“While there are currently a low number of DP3 units with closed bus-ties, our experience with closed-bus systems using new technical solutions has shown these can be more robust in day-to-day performance than open bus-tie systems,” Cargill says.
“Furthermore, the ability to run fewer gensets with closed bus-ties can lead both to significant fuel savings as well as maintenance economies running to hundreds of thousands of dollars a year, depending on the type and operational profile of the vessel.”
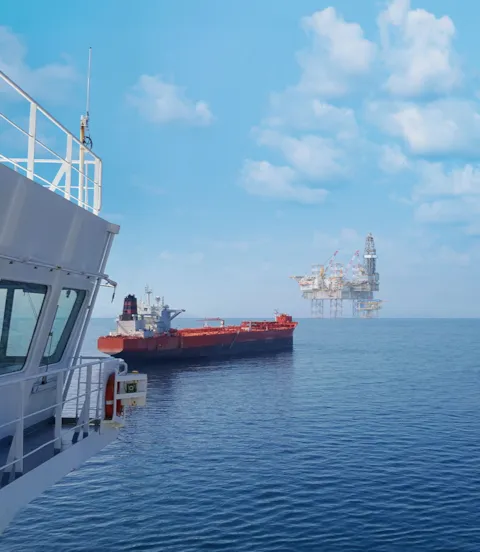
New standards can bolster trust and industry uptake of closed bus-ties
The establishment of new, higher standards such as the focus on built-in test technology as well as models and simulators as tools for verification as proposed in the recommended practice for closed bus-ties can also help reduce the current burden of frequent verification testing of such systems. If the industry is successful in developing such capabilities this may ease the path to industry adoption too.
Karlsen hopes the RP-0591 guidance “can serve as a cornerstone to build trust in the robustness of closed bus-tie systems and promote wider uptake, which will also require investments both in the technology and increased crew training to bolster competence in this area”.
“Furthermore, the recommended practice has a much broader application to support the adoption of fuel-efficient electrical power systems using closed bus-ties. Electrification is playing an increasing role in maritime’s decarbonization and digitalization efforts, and the recommended practice is not limited to DP systems,” Karlsen says.
Aleks Karlsen
Senior Principal Specialist - DP Systems
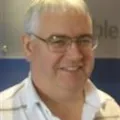
Steven Mearns Cargill
Technical Authority for Dynamic Positioning
Jon Ole Overrein
Senior Principal Engineer - Electrical Systems
- Shutterstock / m.afiqsyahmi
- Shutterstock / Smile Fight
- Shutterstock / donvictorio
- Shutterstock / MR.Zanis/Rafal Beling