Paving the way for large-scale transportation of liquid hydrogen
A collaboration between CB&I and Shell, with close support from DNV, has led to the Approval in Principle (AiP) of a large-scale, liquid hydrogen (LH2) cargo containment system. This could pave the way for an expansion of global hydrogen supply chains in the future.
In August 2023, CB&I received Approval in Principle (AiP) from DNV for its design of a liquid hydrogen (LH2) containment system for carriers. Drawing on CB&I’s established technology for onshore LH2 storage, Shell’s experience with hydrogen carriers, and DNV’s regulatory and safety know-how, a robust design is now ready for further development. Crucially, this will enable the transportation of much larger quantities of hydrogen, compared to previous designs, reducing the cost of transport per unit of energy.
Shipping vital to transportation of hydrogen
Hydrogen is free from carbon and thus viewed as a potentially key contributor to global emissions reductions, especially when created through electrolysis. However, its transportation presents several complications. Whilst some regions could import hydrogen via pipeline, this is not possible over longer distances, such as from Asia to Europe, and shipping solutions are required.
Shipping hydrogen in liquid form is regarded as more practical than gas because of its higher energy density. However, LH2 shipping presents some extra challenges, particularly related to safe storage.
“To liquefy hydrogen, it must be cooled to minus-253 degrees Celsius,” says Tom Klungseth Østvold, Principal Engineer, Structures at DNV Maritime Advisory. “Once this is done, the liquefied hydrogen needs to be stored in tanks with the highest standards in vacuum insulation. Exposing the hydrogen to normal gases will lead to significant impairment as well as many safety hazards.”
Drawing from experience in onshore liquid hydrogen storage
Utilizing technological expertise from the global leader in land-based liquid hydrogen storage can help shipping to achieve higher standards in liquid hydrogen transportation.
“CB&I’s LH2 cargo containment system for LH2 carriers is based on our technology for large-scale onshore LH2 storage,” explains David Creech, Director, R&D at CB&I. “The most reliable design meeting these requirements is a vacuum-insulated double-wall sphere, which provides boiloff rates of less than 0.05% per day, as demonstrated in tests of CB&I’s tanks by NASA. By adapting this technology for shipping, we can provide the market with a proven design backed by over 60 years of operational history.”
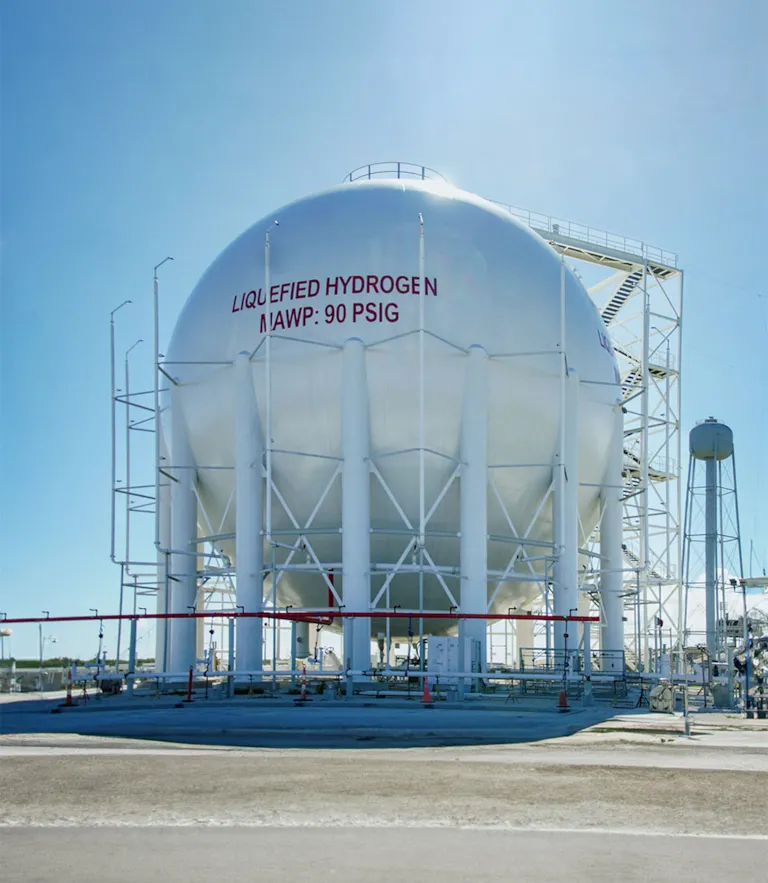
Challenges of adapting LH2 tank design to shipping
Designing the LH2 tanks for shipping required adaptation to a completely different physical environment, such as cold temperatures and ship motions.
“A significant difference between onshore and shipping applications is the presence of cyclic loads from ship motions. Onshore LH2 tanks are designed for earthquakes, but fatigue is not typically a concern,” says Creech. “Thankfully, the support system that CB&I uses to suspend the inner sphere within the outer sphere proved to be readily adaptable for fatigue design.”
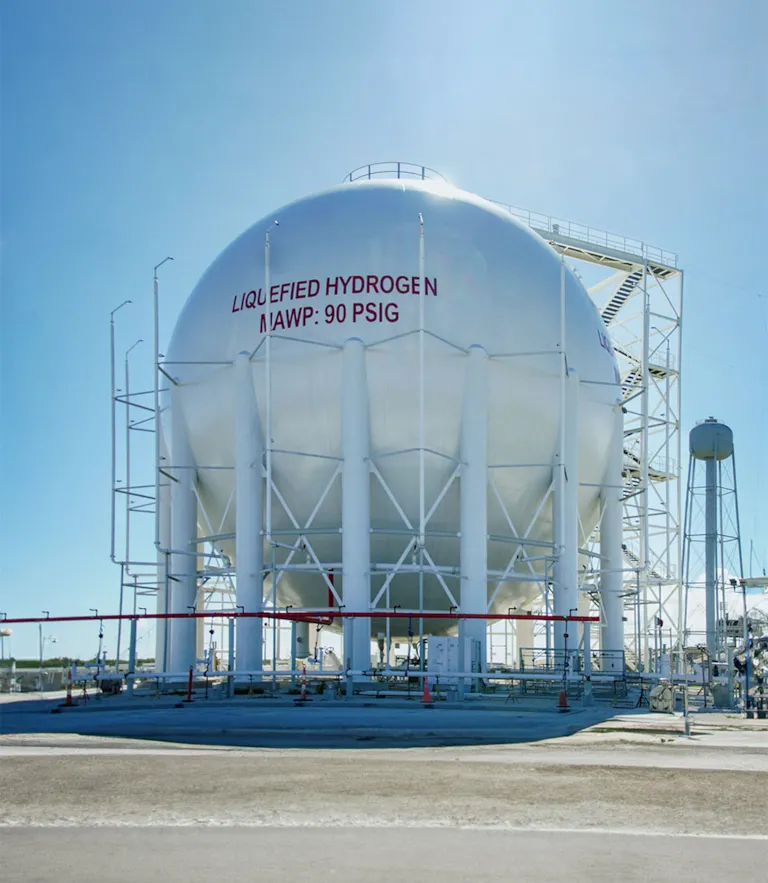
Shell adds maritime experience to tank design
Shell’s expertise was equally valuable in adapting CB&I’s design to the maritime environment.
“Following initial discussions, it was agreed that CB&I would leverage their extensive experience in LH2 storage to develop the containment system and Shell would provide much of the maritime expertise, including the application of experience gained in the design and operation of LH2 equipment and facilities,” says James Cocks, IRD Project Manager at Shell International Trading and Shipping Company Limited.
Early in 2023, ship designer Houlder completed the development of a concept design for a 20,000 m3 LH2 carrier for Shell. Shell then followed this up with a number of initiatives, including a feasibility study for fuel and powering arrangements, concept general arrangement, hull design and powering, and structural design work.
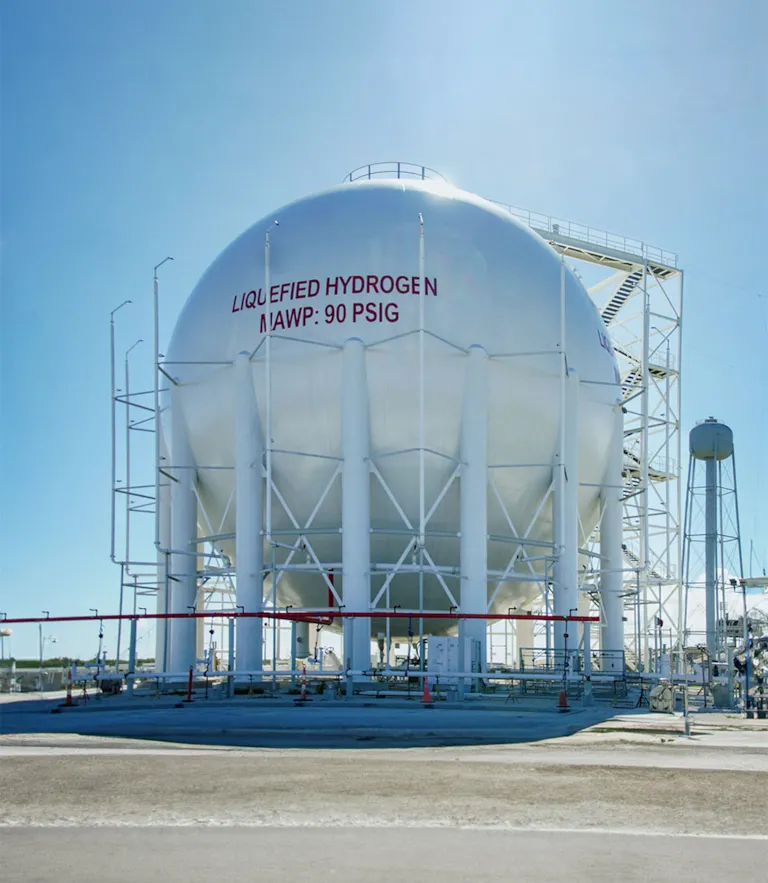
Overcoming the gap and maturity of LH2 standards
Taking this initial design through to AiP has also required careful navigation of maritime regulations and safety codes, including class rules, the International Code for the Construction and Equipment of Ships Carrying Liquefied Gases in Bulk (IGC Code) and the IMO’s Interim Recommendations for Carriage of Liquefied Hydrogen in Bulk, Resolution MSC.420(97). This has been a challenging proposition for a relatively novel maritime technology.
“The immaturity of rules and regulations for LH2 cargo containment systems in maritime transport was a major challenge. This led to the decisions being made at the start of the project about which sections of the IMO’s IGC Code should be applied, despite the code not currently including LH2 as cargo,” says Cocks.
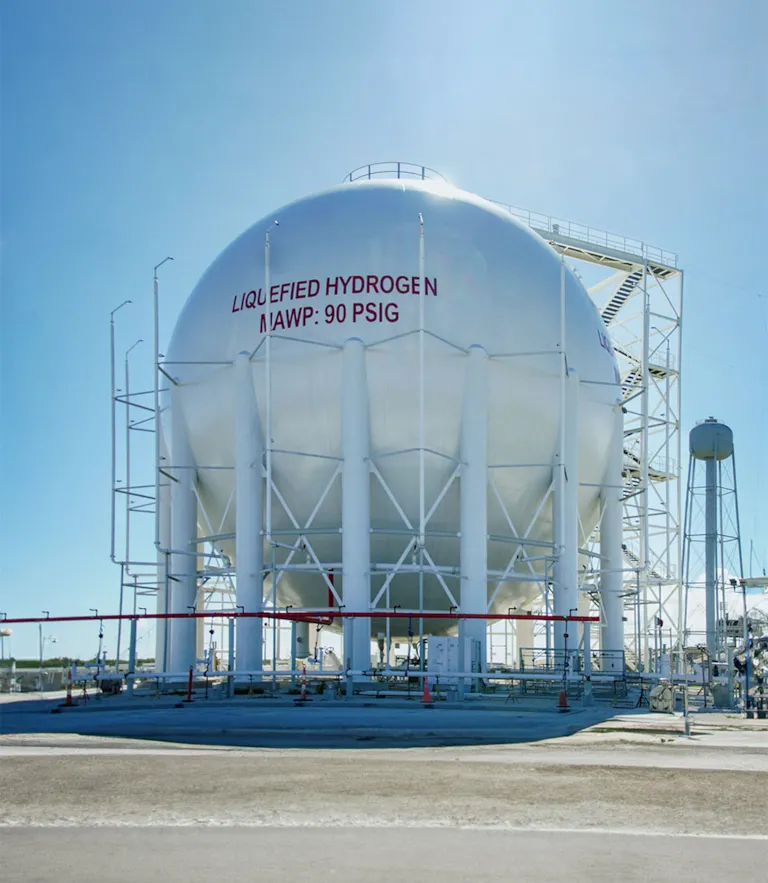
Bridging the gap with DNV’s regulatory know-how
DNV’s experience and know-how around maritime regulations were instrumental in smoothing this process.
“Standards are very much a work in progress for both the onshore and shipping applications of LH2 storage,” says Creech. “DNV provided CB&I with key insights into how IGC Code and Class Rules would view the unique aspects of LH2 cargo containment systems.
“A key part of DNV’s role was to explain the regulatory framework and how this would differ from what CB&I applied when designing these tanks. They were happy to take this advice on board and adapt it into their design,” says Østvold.
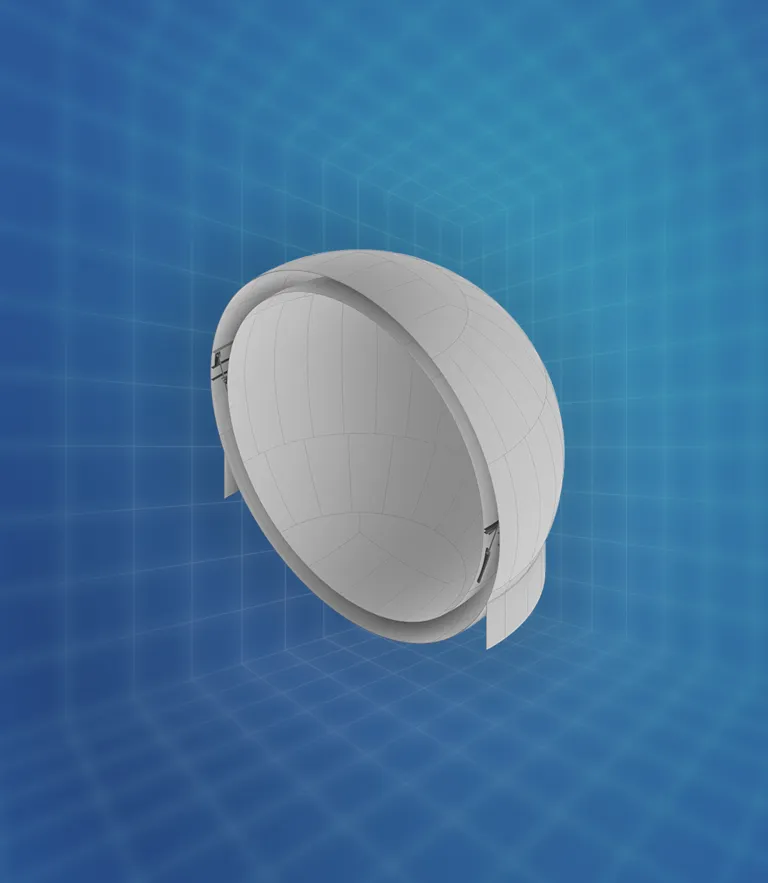
Successful design adaptation to maritime standards
Close collaboration with DNV has led to some incremental changes to the original design, resulting in a concept that is robust and fully fit for maritime transportation.
“It was a smooth process with good dialogue on all sides,” says Østvold. “We covered a lot of areas, probably in more detail than is strictly necessary for an AiP, but this resulted in a final design that’s safe and has very few uncertainties.”
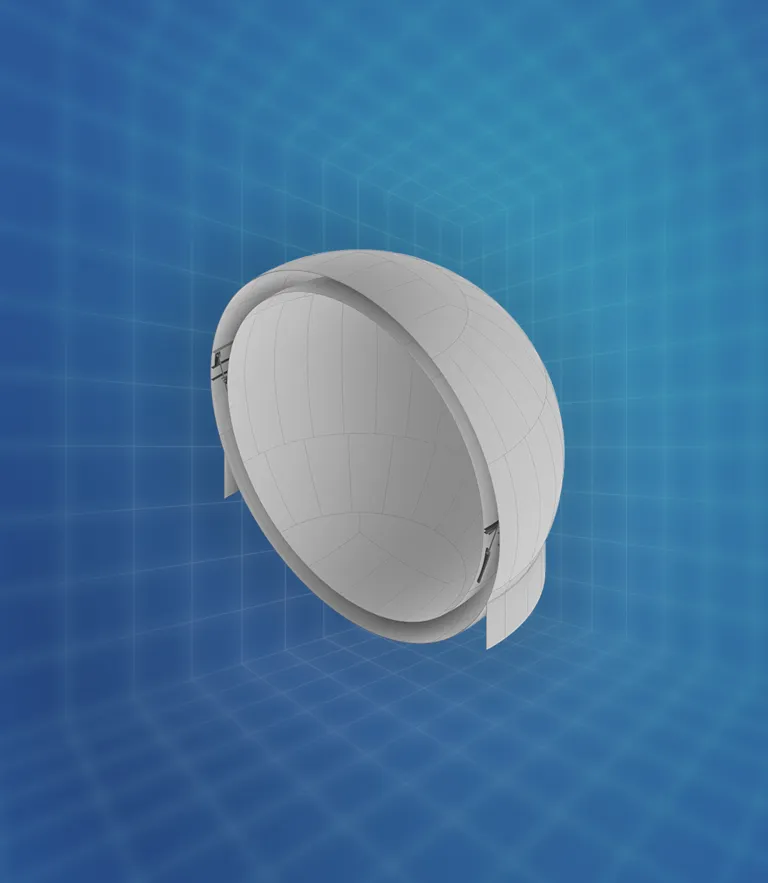
Achieving AiP a key milestone for hydrogen supply chain
Receiving an AiP from DNV has been a key milestone in the development of the LH2 carrier concept, paving the way for further development of hydrogen supply chains.
“The awarding of an AiP from DNV resulted from a lot of hard work and collaboration between companies working at the forefront of innovation in this sector,” says Cocks. “To support the role of liquid hydrogen in the energy transition it’s critical that its potential as a viable energy carrier is demonstrated with urgency. Achieving this AiP was a significant step in the right direction.”
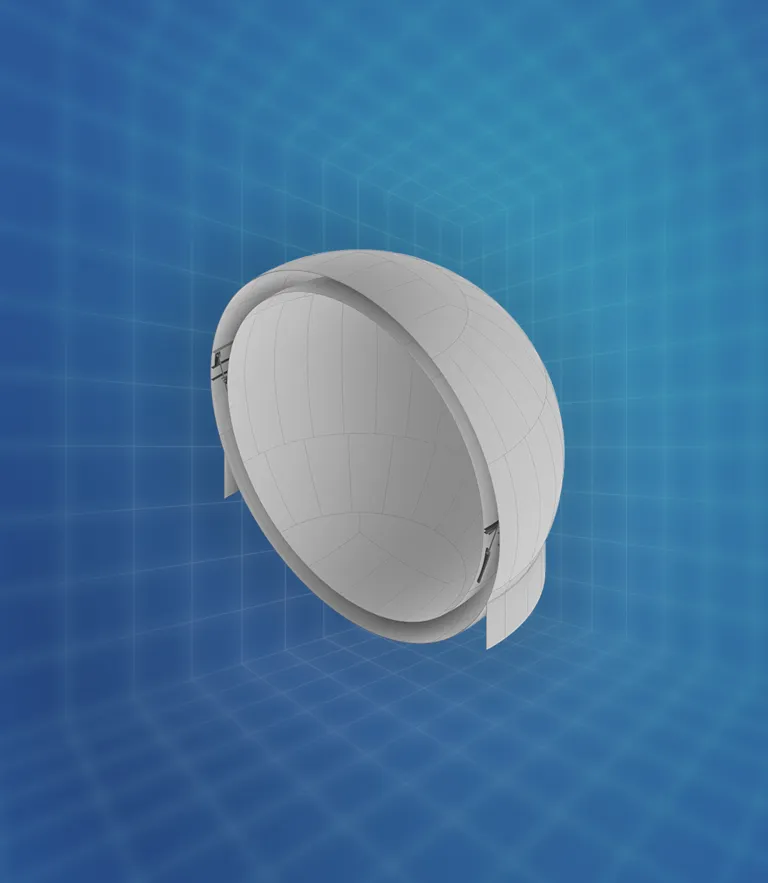
LH2 tank sizes scalable
The success of this collaboration has already spurred these companies to explore how this design could be scalable in the future.
“CB&I’s present technology can scale up to 40,000 m3 per tank, which is sufficient for carriers up to 200,000 m3,” says Creech. “Our focus is now on working with shipyards to integrate our containment system into ships optimized for liquid hydrogen.”
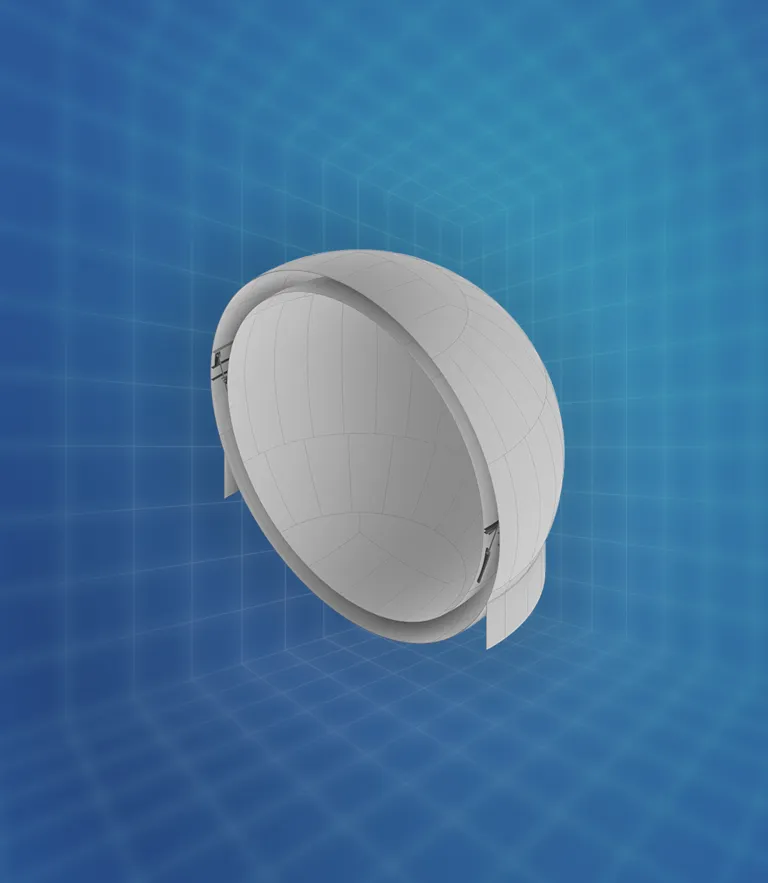
Hydrogen role in the future energy mix
With hydrogen seen as a key fuel of the future, CB&I are already planning for further technological development. “We’re very active in research and development of cryogenic storage technology so we can continue to bring innovations to both the onshore and shipping markets for liquid hydrogen,” says Creech.
As this project has shown, collaboration with maritime experts will be crucial to future success.
“DNV will continue to support companies like CB&I and Shell at the forefront of the development of technologies and infrastructure for hydrogen,” concludes Østvold. “This will require navigation of rules and an appreciation that safety should always lie at the heart of innovation.”
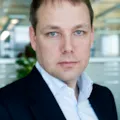
Tom Klungseth Østvold
Principal Engineer, Structures
- Shell/Houlder
- CB&I
- CB&I/Alesandro14 – Shutterstock
View image copyright information