New guidance on achieving stable lifting operations
What is best practice when it comes to cranes lifting loads onto, off and between ships in port or at sea? New guidance from an industry forum initiated by DNV dives into the key considerations and calculations to help ensure these hazardous operations are performed safely to reduce the risk of loss to life, property and the environment.
“The paper Guidance on Stability of Lifts plugs a gap among the many guidance documents available for operations in the maritime sphere,” says Karsten Behrens, Managing Director of SAL Engineering GmbH. “It enables readers to assess the stability of particular lifting arrangements by using the provided methods and data. This puts them in the position to achieve a ‘stable lift’, which is one that remains in a balanced condition, within a safe margin, when subjected to predefined disturbing factors.”
What is in Guidance on Stability of Lifts?
The paper explains currently available calculation methods, along with relevant explanations, guidance for assumptions on loads and factors, and background information.
The core of the paper is a flow chart for assessing the lifting stability of a rigging arrangement, which also reflects the common workflows of the participating project partners.
Checkpoints and information blocks in the chart enable users to review the rigging plan they have created, to assess its suitability, and to create a framework of boundary conditions.
“The paper also helps the user to identify important factors for assessing the lifting stability and potentially dangerous combinations of them,” Behrens states.
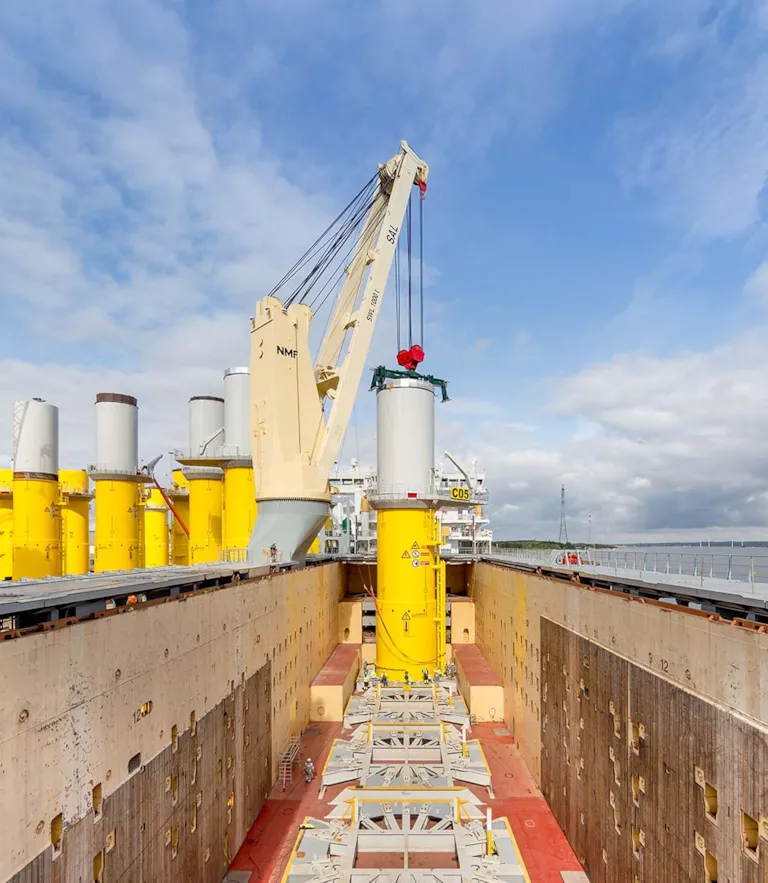
Following step-by-step guidance
In an easy-to-follow systematic approach, the guidance then works through details clarifying steps from the flow chart.
Guidance is grouped into five steps. Step one involves preparing a draft rigging plan. Step two is to assess whether the rigging points are friction-dependent. Step three is working out if the centre of gravity (CoG) of the rigging arrangement is above the lifting points. Step four, if applicable, is determining and documenting operational limits.
“Step five is to create a final rigging plan complying with the selected criteria, which can then be added to the operational procedure,” Behrens adds.
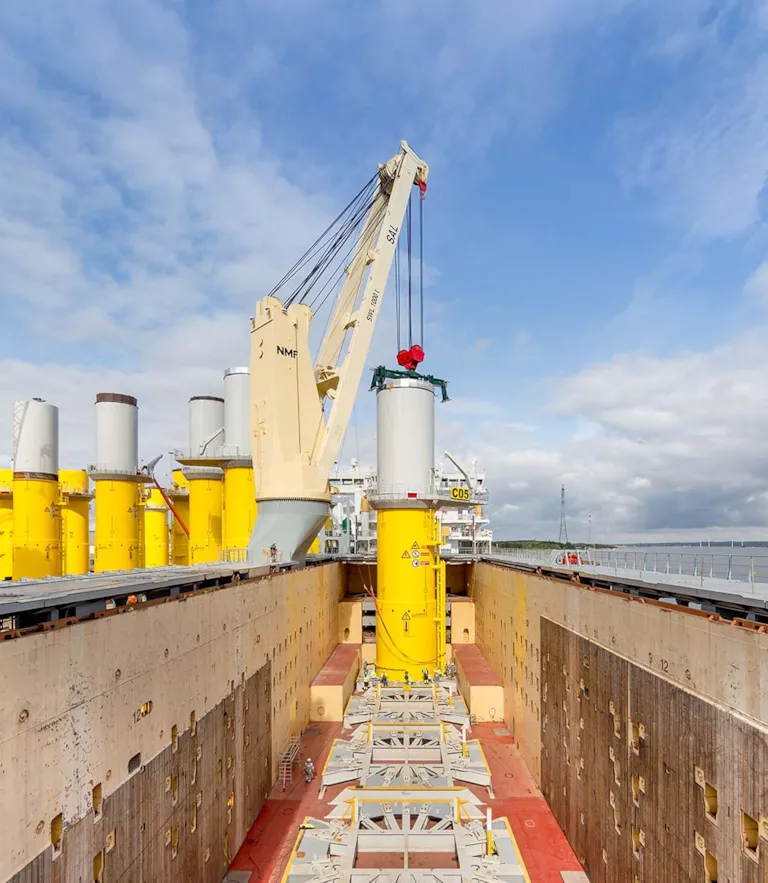
Comparing methods for stability assessments of lifts
To assist the process, the guidance makes a comprehensive comparison of different methods to assess the stability of lifts.
These methods are the Virtual CoG concept; the Kaps method, which is widely used in the maritime industry; the Nikitin method; and standard and extensive versions of numerical computer simulation methods.
The applicability of these methods for various purposes is discussed. For example, Virtual CoG and Kaps allow users to evaluate the initial stability of the lift, Nikitin provides insight on the stability against the overturning of two-chain suspensions, while numerical computer simulations allow a much more detailed analysis. “The numerical simulations are useful to understand the behaviour of a lift at certain phases of a lifting operation,” explains Sebastian Becker, Team Lead CAD Design, SAL Engineering GmbH.
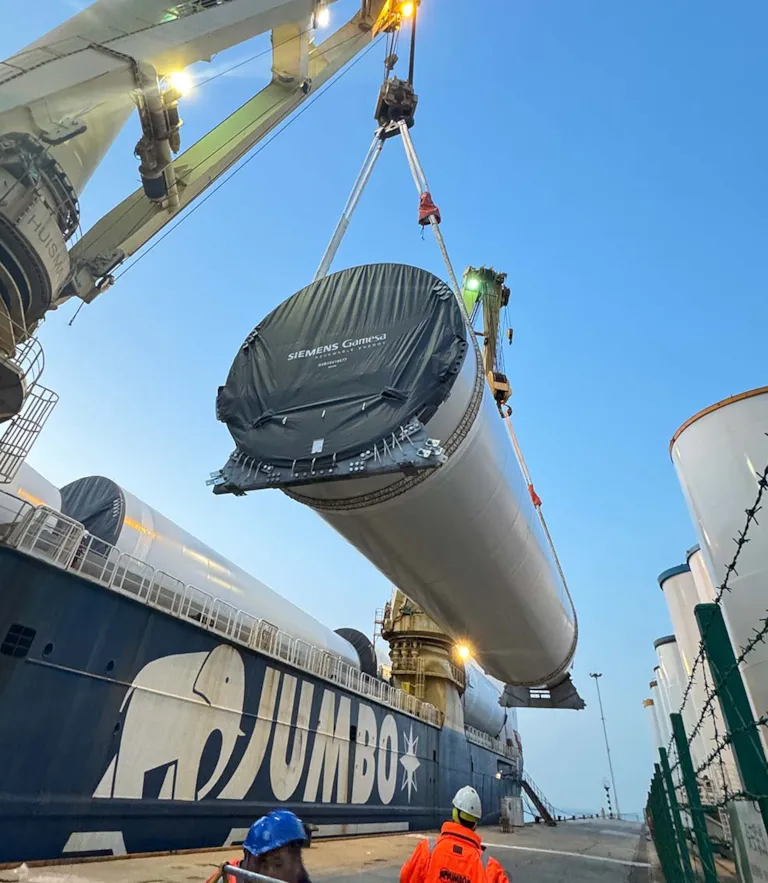
What should be considered in the stability assessment?
A stable lift is one that remains in a balanced condition, within a safe margin, when subjected to predefined disturbing factors.
Disturbing factors may include wind force, rigging length tolerance, steering line forces, crane movement, CoG shift, vessel motions and friction at the lifting points.
The guidance paper explains several disturbing factors, together with relevant mathematical equations for calculating their impacts. It presents this material in a way that allows these factors to be incorporated into the calculations for rigging stability assessment.
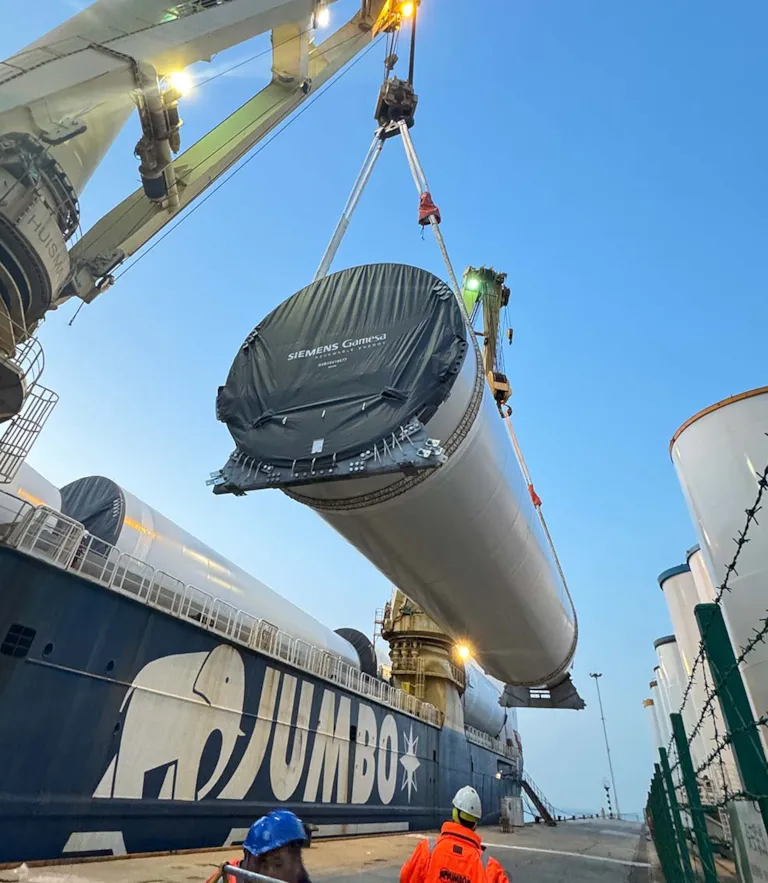
Calculating sliding and effective inclination angles
The sliding angle is the inclination angle at which a lifted cargo starts to slide, and it should never be reached during lifting. The angle depends on the friction between the materials in use, and on the shape of the contact surface. For instance, the effective inclination angle of a belly-slung cylindrical object is significantly different to a conical section.
Calculating sliding and effective inclination angles is useful when assessing lifting arrangements that involve friction-dependent lifting points, which exploit the fact that frictional force resists relative motion between surfaces in contact.
“The guidance includes extensive discussion and formulas to calculate theoretical sliding angles for standard cases. Of course, coefficients indicating degrees of friction can vary significantly, and assumptions should be made conservatively,” Becker comments.
Guidance on Stability of Lifts has been developed by a sub-working group of the Heavy Lift Exchange Forum, a DNV-initiated round table for heavy-lift shipping companies. Members of the working group are from the companies BBC Chartering, BigLift Shipping, DNV, Heerema, Jumbo Maritime, SAL Engineering and United Heavy Lift.
Jan Rüde
Ship Type Expert MPV
- BigLift
- Guidance on Stability of Lifts, HLEF, 2024; after Kaps, 2013 (1)
- SAL
- Guidance on Stability of Lifts , Heavy Lift Exchange Forum, 2024
- Guidance on Stability of Lifts, Heavy Lift Exchange Forum, 2024
- Jumbo
View image copyright information