Addressing methane slip in LNG-burning four-stroke Otto-cycle engines
LNG offers many benefits as a transitional ship fuel. However, certain engine types have been found to release significant amounts of unburnt methane, a powerful climate gas. DNV is involved in various projects aiming to minimize methane slip.
Methane, the main component of natural gas and LNG, has a global warming potential (GWP) 29.8 times that of carbon dioxide (CO2) over a 100-year timeframe, according to the Intergovernmental Panel on Climate Change (2021). Preventing methane from escaping anywhere along its supply chain is therefore crucial as the world tries to contain the causes of climate change.
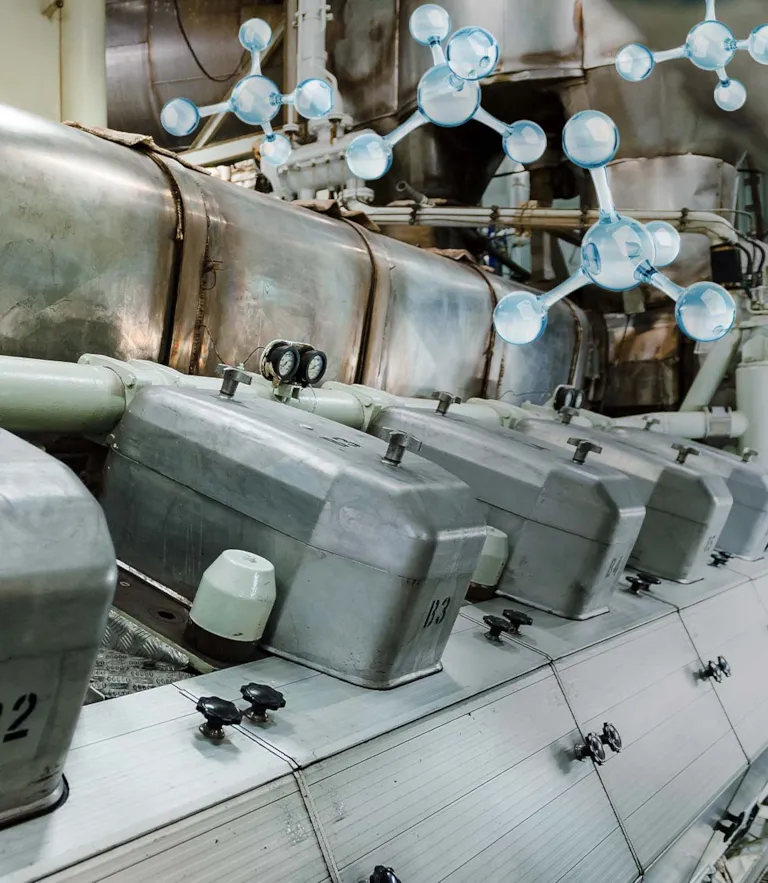
New EU regulations increase pressure to reduce methane slip
LNG-fuelled four-stroke Otto-cycle engines, which are often used for gensets on board passenger ships, have been found to release significant amounts of unburnt methane, leading to CO2-equivalent emission values that compromise what is achieved through other carbon reduction efforts.
The shipping sector will be incorporated into the EU’s Emissions Trading System (ETS) from 2024. This expansion will encompass methane and nitrous oxide emissions starting in 2026. Additionally, the FuelEU Maritime requirements for the GHG intensity of energy utilized on board will come into effect in 2025. Consequently, the shipping industry is keenly interested in addressing methane slip issues
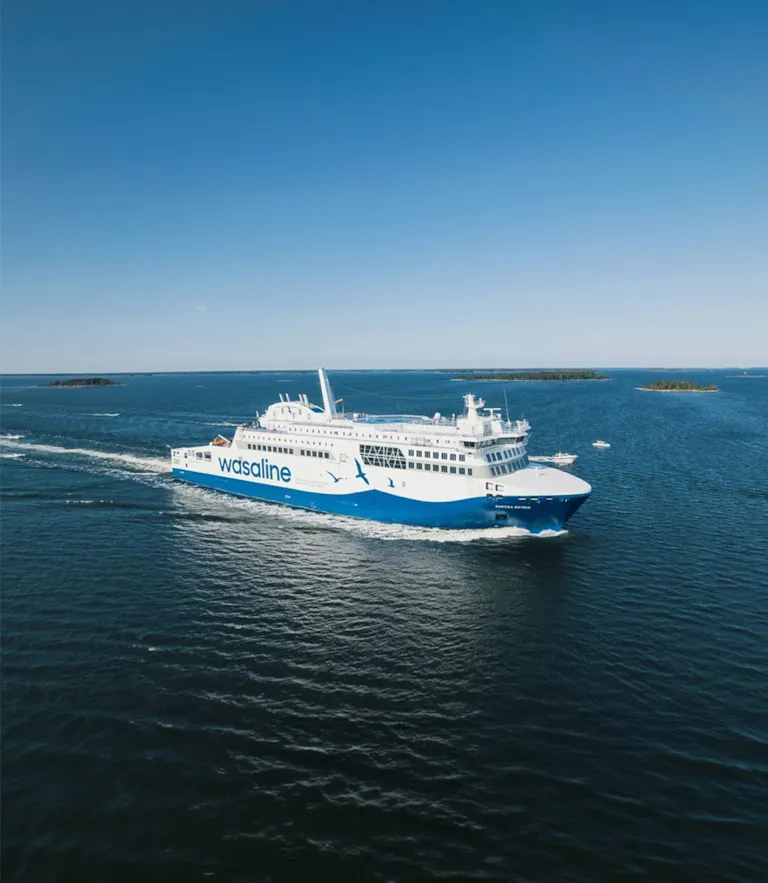
LNG's long-term zero emissions potential hinges on methane slip reduction
“Many think of LNG as a transitional fuel only, but it can also be much more than this,” says Hans Eivind Siewers, Segment Director Passenger Ships and RoRo at DNV. “But in order for this fuel to take passenger ships all the way to zero emissions with bio LNG and e-LNG, it is of major importance that we succeed in reducing methane slip.”
Fabian Kock, Head of Section Environmental Technologies Air at DNV, agrees: “Methane slip is indeed a critical issue for addressing climate change. DNV is actively working with many stakeholders and regulators to find pragmatic solutions to overcome this challenge. In particular we are happy to work closely together with the engine designers to find technical solutions which are safe and feasible to be installed on board of ships.”
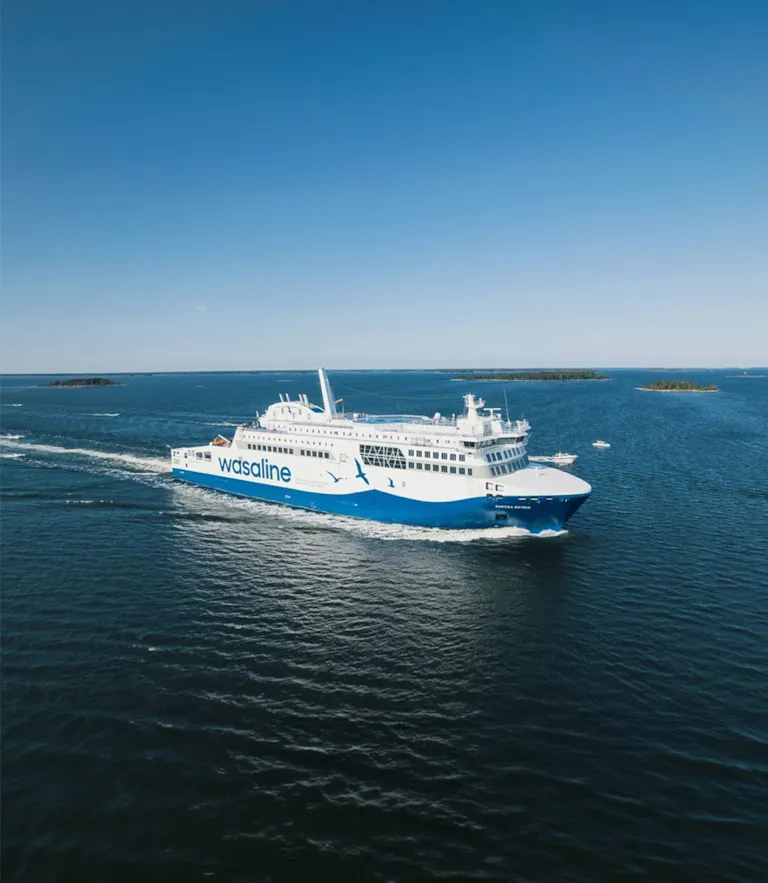
GREEN RAY industry initiative addresses methane slip
One major initiative dedicated to reducing methane slip from LNG ship engines is the EU HORIZON project GREEN RAY (new GeneRation marinE ENgines and Retrofit solutions to Achieve methane abatement flexibilitY). Launched in June 2022 under the leadership of the VTT Technical Research Centre of Finland, it aims to establish sound scientific data about methane slip from four-stroke LNG-fuelled engines by conducting on-board exhaust gas measurements, and to promote the development of methane abatement technologies.
The project consortium includes the Finnish Meteorological Institute, Shell Global Solutions, Wärtsilä, MSC, CMA Ships, Chantiers de l’Atlantique, DNV and a number of other stakeholders. A report will summarize the findings after the project ends in 2027.
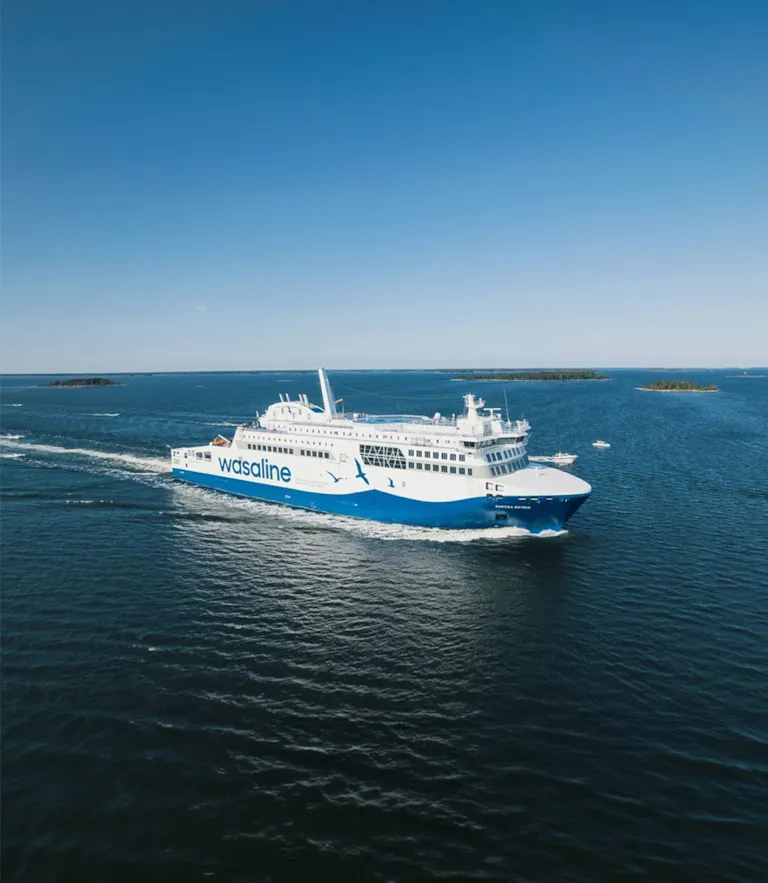
Focus on engine optimization and exhaust gas aftertreatment
The engine manufacturer Wärtsilä has been conducting research and development on engine modifications to radically reduce methane slip, including efforts to optimize engine design and control. VTT researchers studied methane emissions from two Wärtsilä 31DF engines on the AURORA BOTNIA. One used standard configuration, the other tested new combustion. Results show reduced methane emissions and potential for overall emission cuts for the modified engine.
Shell is developing methane absorption and catalytic conversion technologies for exhaust gas aftertreatment. The role of DNV in the GREEN RAY project will be to witness exhaust gas measurements, verify piping and materials as well as installation, and develop and update its class rules related to emission reduction with the option to introduce a dedicated class notation. Furthermore, DNV will provide know-how and review solution proposals.
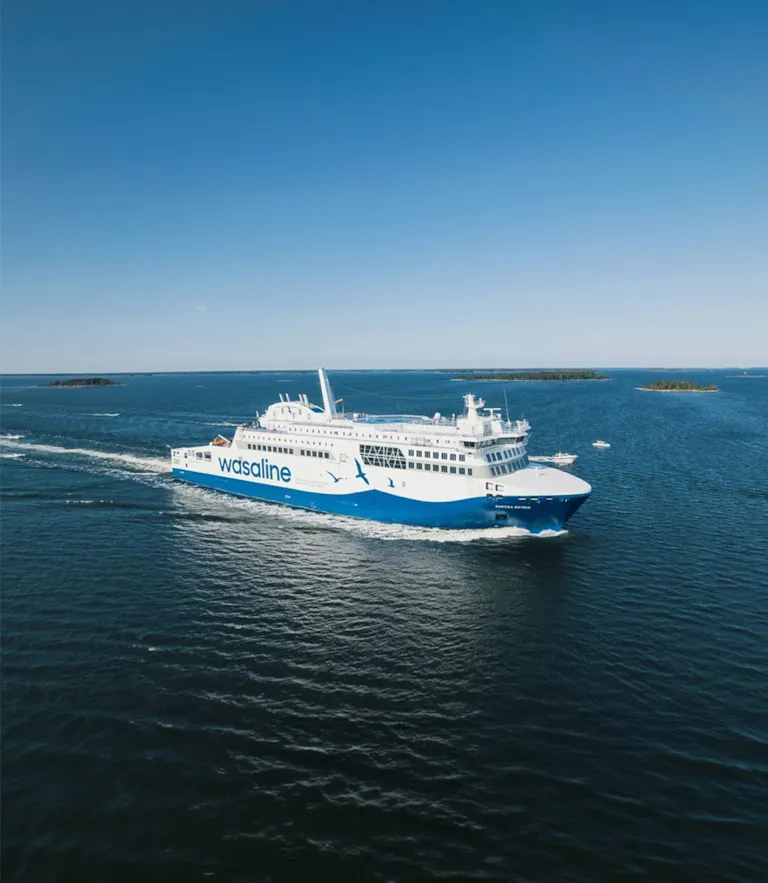
MAN takes a two-pronged approach
There are similar initiatives beyond the GREEN RAY project, as well. MAN Energy Solutions SE has been exploring ways to optimize its own engine technology to minimize methane slip. The company’s R&D into engine optimization is well advanced and integrated into every new four-stroke ship engine MAN delivers, says Dr Mathias Moser, Head of Technology and Exhaust Aftertreatment at MAN Energy Solutions SE. “We optimize the mechanical components to minimize crevice volumes in the cylinder and we adapt the compression ratio towards improved combustion,” he explains. “Furthermore, we fine-tune engine control parameters such as injection timing, pilot-fuel amount, supercharge pressure, ignition timing, valve timing and combustion temperature. Most of these improvements can be implemented as retrofits to existing engines, as well. These engine-based measures alone can reduce methane emissions significantly so the updated engines will comply with future, tighter restrictions.”
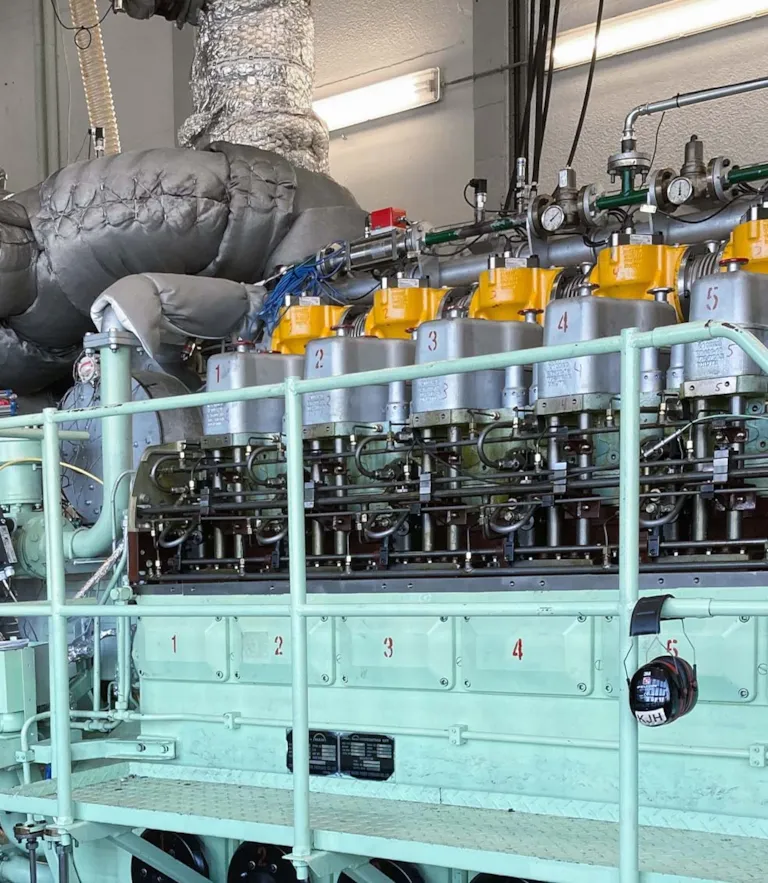
Skip-firing optimizes operational efficiency
Another advanced emission control method is “skip-firing” under reduced loads to avoid higher emissions when lower amounts of fuel are injected and combustion cannot occur in optimum conditions, explains Moser. “In such a scenario, some cylinders of an engine are automatically shut down – they idle without taking in any fuel so the remaining cylinders can operate under higher load at the designated air-to-fuel ratio and burn their fuel with higher efficiency and fewer methane emissions.”
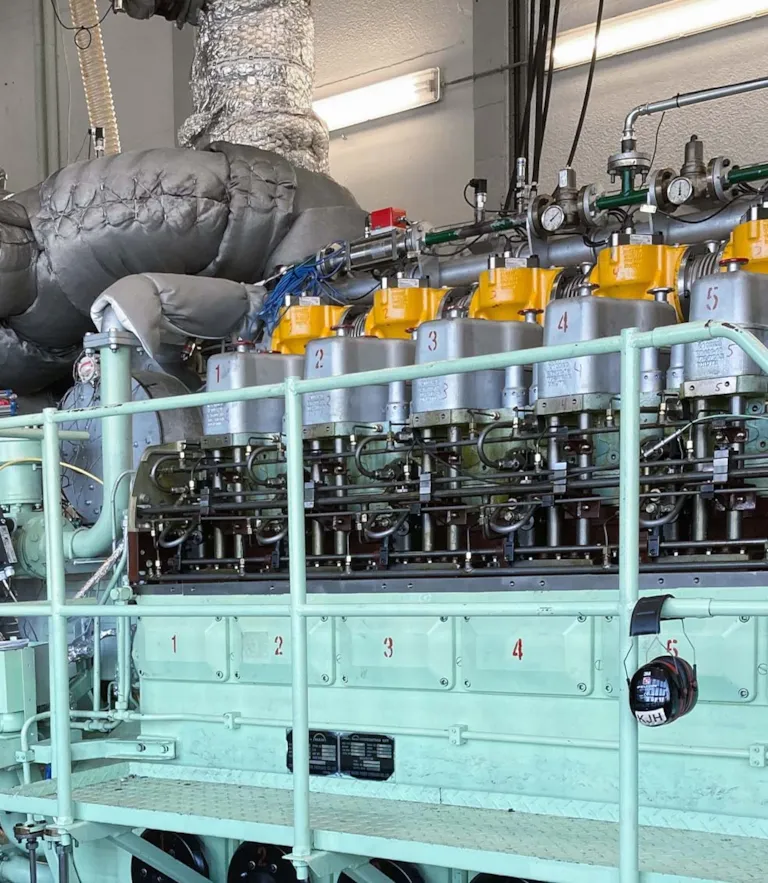
Innovative approach to catalytic methane removal
Exhaust gas aftertreatment is far more challenging, says Moser. “Existing catalytic honeycomb materials are easily poisoned by sulphur from the pilot fuel and engine lubricants. Working closely with suppliers, we had to develop an entirely new catalyst technology that withstands the harsh environment of the exhaust gas.” MAN tested many materials and finally developed a sulphur-resistant system that is able to remove around 70 per cent of the methane from the exhaust gas stream of the test engine.
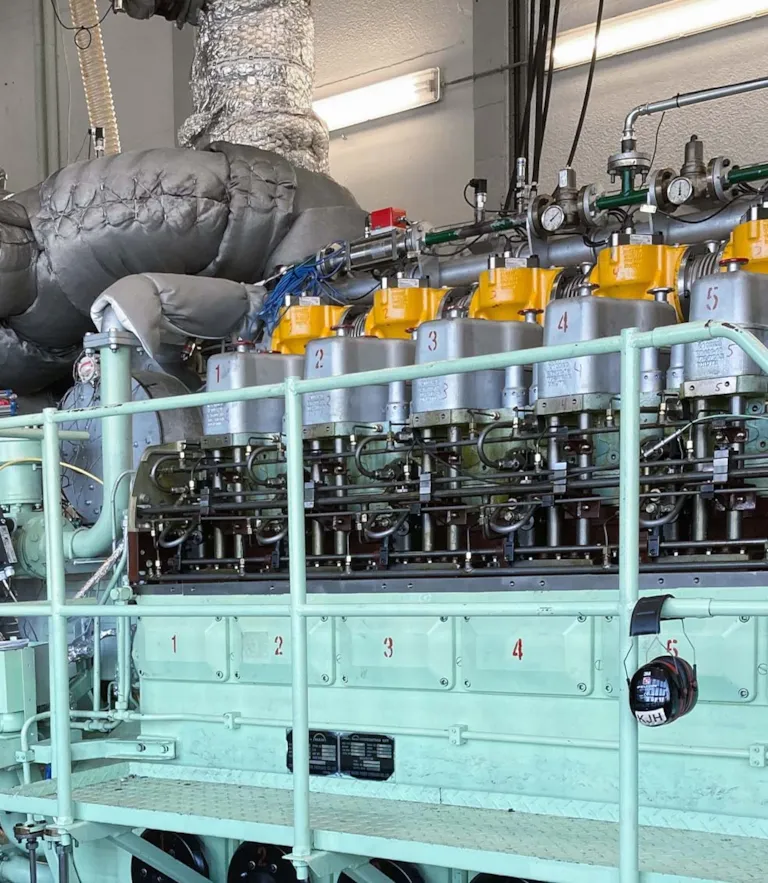
Preparing for the endurance test at sea
As a high-pressure, high-temperature system, the MAN catalytic unit must be installed in the confined space between the engine and the turbocharger, so it has to be compact. “It is important to take a holistic perspective and look at the engine, catalytic unit and turbocharger as one system because they interact,” Moser points out. “All control parameters must account for the entire organism.” The prototype is currently undergoing final test-bed trials.
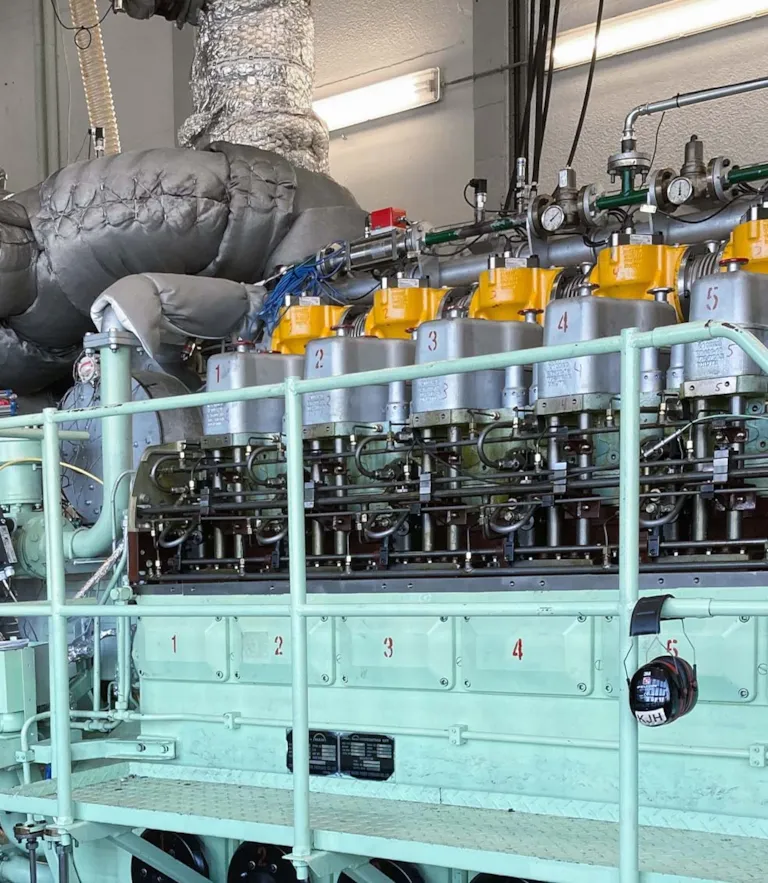
Verification and certification of emission performance: paving the way for commercial operations
“We are aiming for a system service life of 8,000 to 10,000 operating hours. This trial will provide us with crucial insights and performance data. It will also allow us to calibrate our simulation models and fine-tune our operational parameters before taking the system to the market,” says Moser. “It is important to perform these tests together with class to verify and certify the methane reduction performance, ensure compliance as well as safety on board, and ultimately get the go-ahead for commercial operation.”
Catalytic systems and well-coordinated engine optimization measures will be crucial for the shipping industry to achieve its carbon emission goals. They will provide shipowners with another opportunity to minimize their carbon footprint and demonstrate an eco-friendly operational philosophy.
Fabian Kock
Head of Section
- Wasaline
- MAN Energy Solutions
- Avenir LNG
View image copyright information