Understanding the risks of isolated vapour pockets
Isolated vapour pockets (IVPs) are generally believed to be an issue only when tank fill levels exceed 98 per cent. Experience has shown, however, that the risks are much more wide-spread. DNV’s ERS™ service can provide advice and emergency assistance.
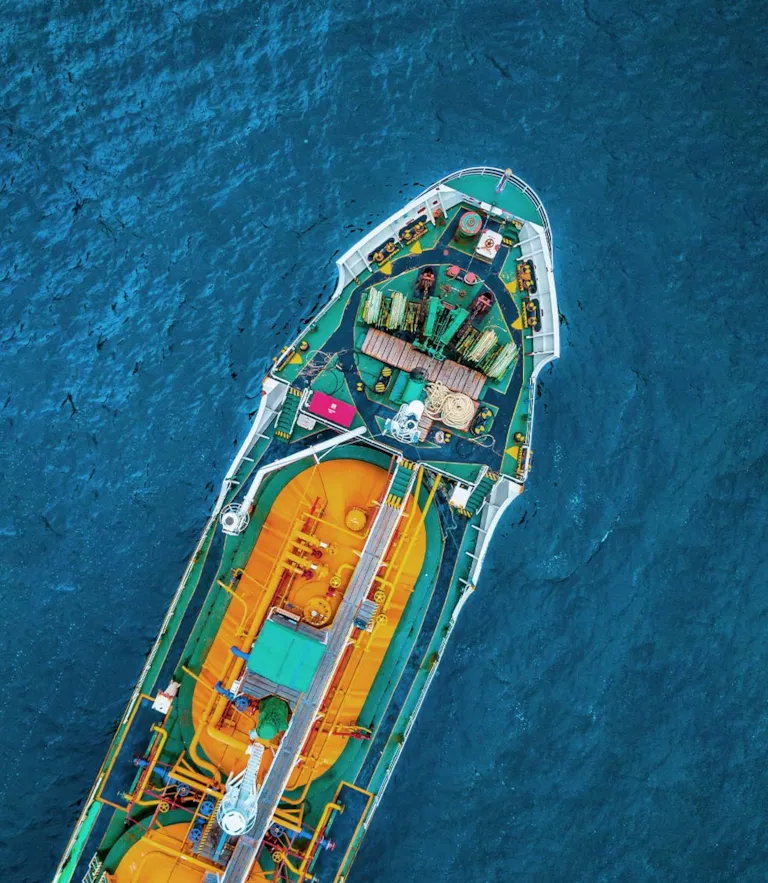
Pushing cargo capacity limits
According to the IGC Code, Administrations may allow owners to exceed the statutory 98 per cent maximum fill level up to 99.5 if the vessel in question satisfies certain criteria. For ships built since 1 July 2016, the new IGC code requires formal assessment of the risk for IVPs.
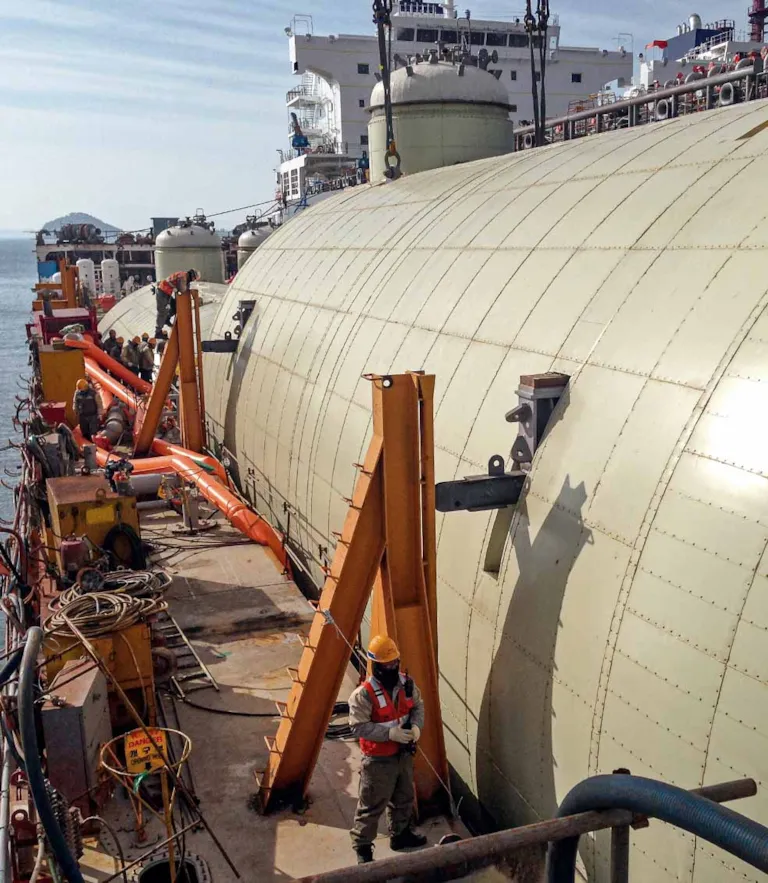
Boil-off gas needs space to expand
The vapour space at the highest point of the cargo tank is connected to vapour lines and safety valves, which allow the boil-off gas to escape when it exceeds a certain amount of pressure. While the vapour “bubble” may wander around in the upper part of the tank and sometimes split into several pockets as the ship rolls and pitches during a voyage, it will always return to the highest point of the tank whenever the ship is in an upright position, allowing all the individual vapour pockets to reunite and connect to the safety valves and vapour lines.
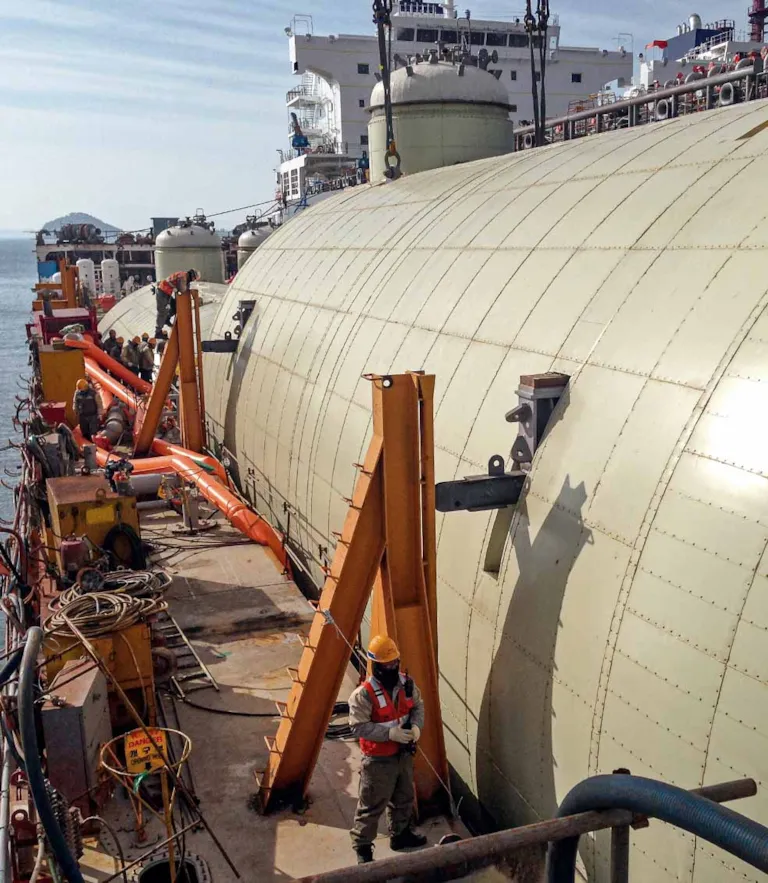
Isolated gas pockets are highly hazardous
When a gas carrier experiences a significant permanent list or excessive trim for an extended period of time due to grounding, flooding or any other exceptional condition, isolated vapour pockets (IVPs) will form and remain stuck in locations of the tank that are not connected to the safety valves and vapour domes. When this occurs, the expanding boil-off gas will push the liquid cryogenic cargo into these vapour collection systems, causing them to shut down, which in turn will result in an additional pressure increase. If this pressure cannot be relieved, liquefied gas will enter the vent mast, which may crack or burst because it is not designed to withstand exposure to cryogenic liquids, says Rossen Panev, Principal Engineer, Emergency Response Service (ERS™) at DNV: “The liquefied gas may spill on the deck and cause severe damage; it may even catch on fire or explode. This is why static list poses a grave risk for these ships.”
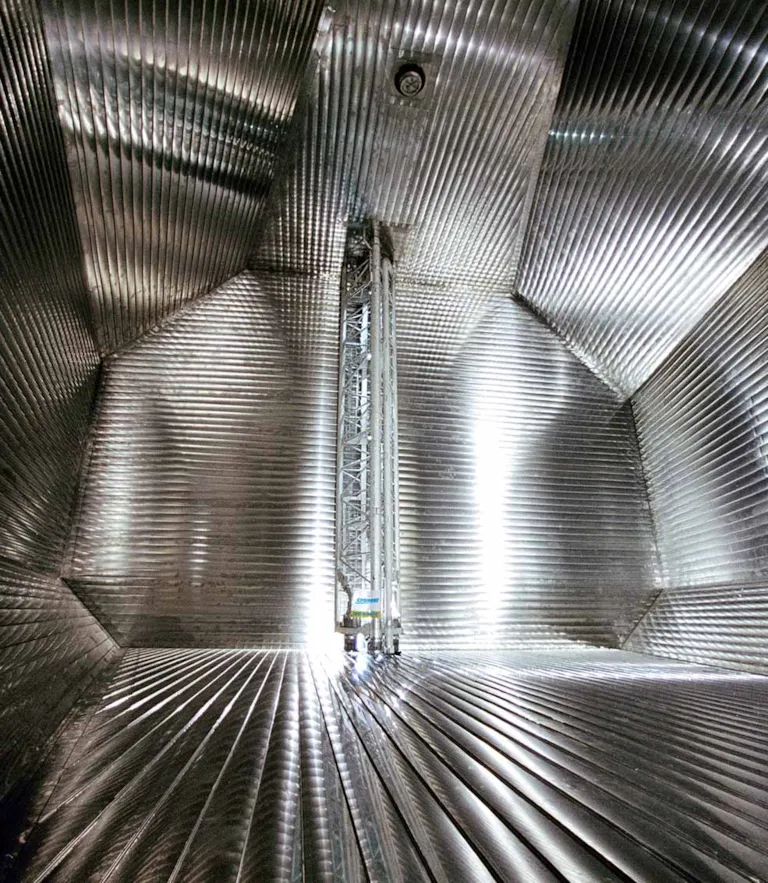
Underestimated risks even at lower filling levels
“While the focus and the requirement for formal assessment of IVP-related risks are set on filling limits higher than 98 per cent, it is important to understand that the phenomenon can also occur at lower filling limits at high values of static list and trim,” says Panev.
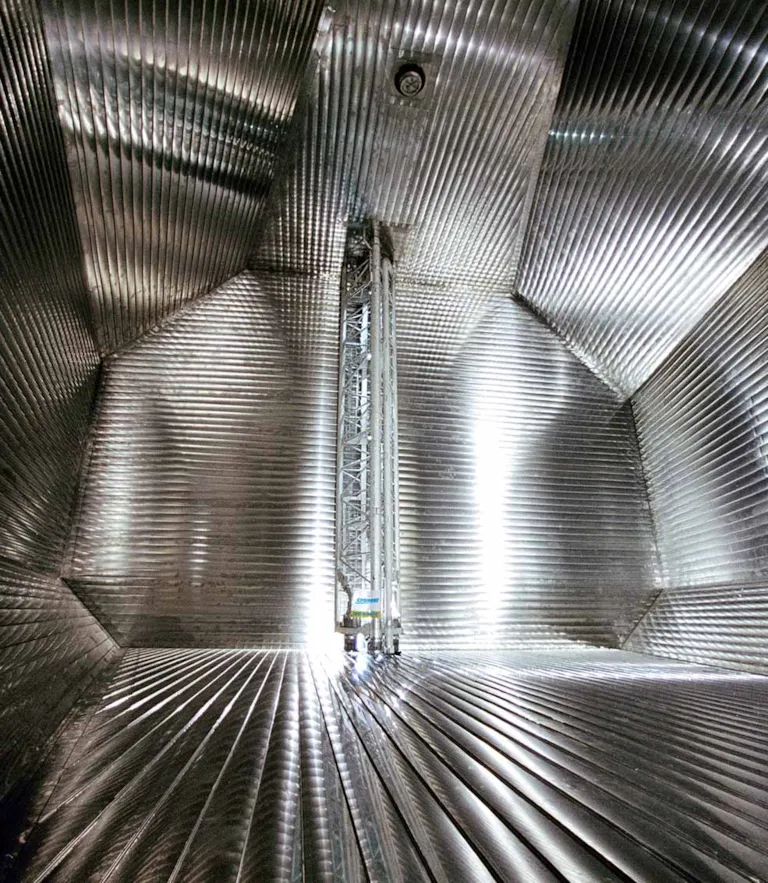
Many tank and liquefied gas types affected by IVPs
What is more, hazardous conditions caused by IVPs are not limited to membrane tanks. “Type-C and bilobe tanks can encounter this phenomenon, as well,” Panev points out. “The range of ships and conditions where IVP issues can occur is much wider than is generally assumed. It is important for gas carrier owners to be aware of this and determine whether their vessels are subject to IVP-related risks. In many cases, ships have no appropriate procedures in place and IVP situations are not included in their emergency drills.”
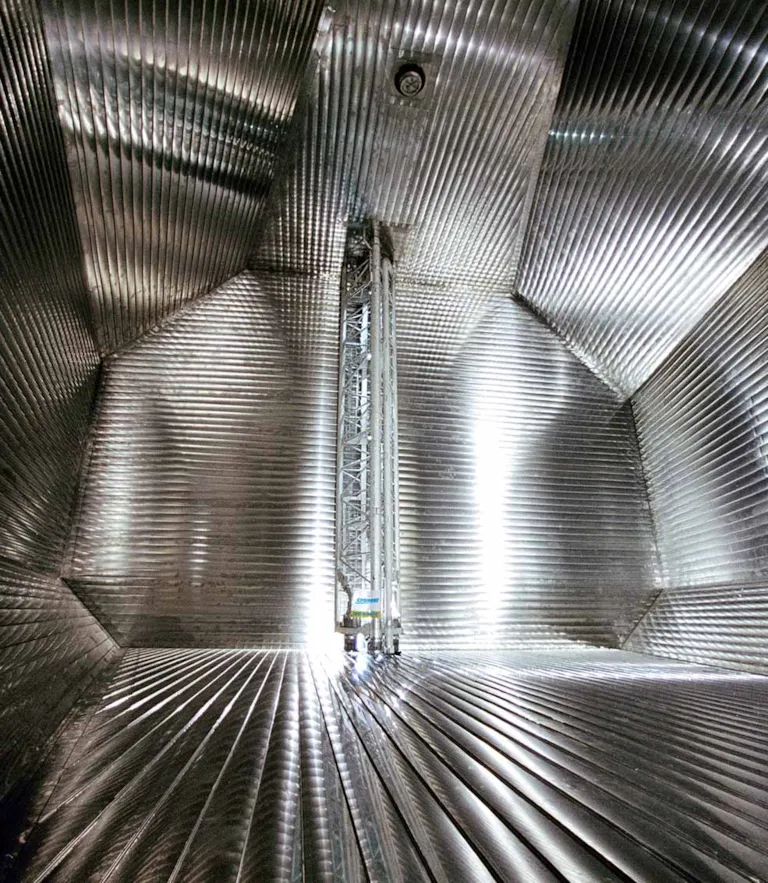
Options for handling damage situations involving IVPs
Knowing what to do in a critical condition is not easy. “For example, when a ballast tank or the engine room is flooded, you cannot simply put the ship upright by adding water to the ballast tanks on the opposite side because the sheer weight of the water may cause the vessel to break apart,” says Panev. There are various options to connect the isolated vapour pocket with the main vapour space and eliminate it, such as transferring some of the cargo between tanks, venting it, consuming some of the cargo using a boiler or gas consumption unit (GCU), spraying cool cargo into the IVP to reduce pressure, or as a last resort, jettisoning some cargo in a controlled and safe manner.
The ERS™, DNV’s damage control service for ships in trouble, now includes comprehensive support for gas carrier damage situations involving IVPs. Available to pre-enrolled ships 24/7, DNV’s ERS™ experts will use a 3D virtual ship model; current list, trim and fill level information provided by the crew; and custom software to simulate the cargo tank position and determine where IVPs are located. Based on their conclusions they will provide specific advice to the crew on how to address the situation, minimize the risk and – if possible – restore contact between the IVPs and the vapour collection systems so the pressure can be relieved without causing further damage or harm.
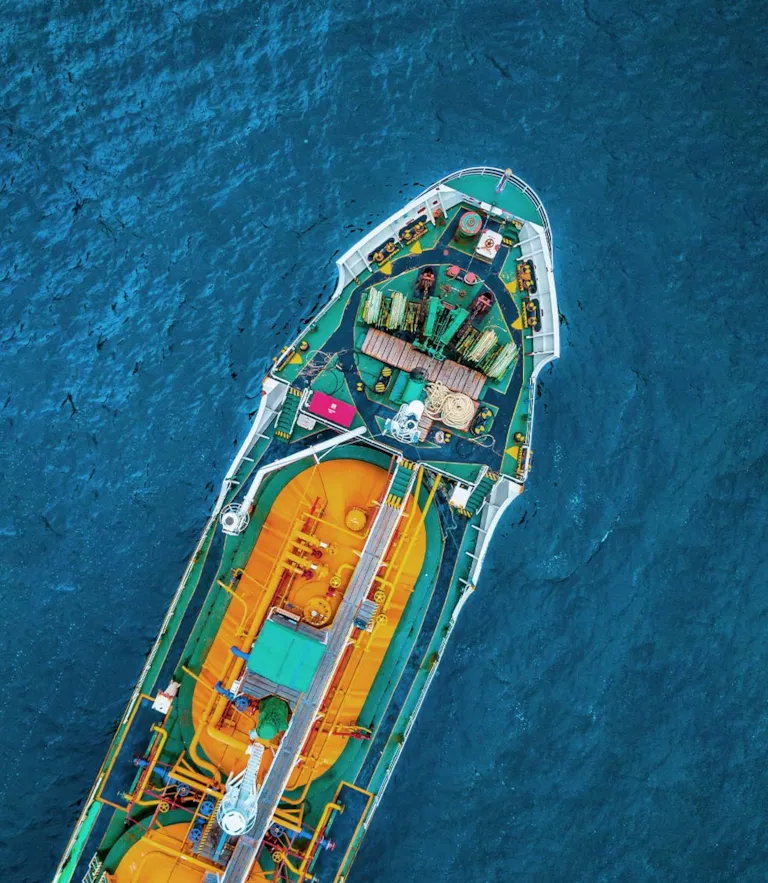
ERS™ now provides comprehensive support for gas carriers
Furthermore, DNV offers damage control drills using IVP simulations. DNV recommends gas carrier owners and operators to develop their own emergency procedures for situations involving IVP risks. DNV has published a flyer titled “Awareness and mitigation of isolated vapour pockets on LNG and LPG Carriers,” which provides further details.
The IACS, various ship designers and the Society of International Gas Tanker and Terminal Operators (SIGTTO) have developed various guidelines on IVP mitigation. “We at DNV urge gas carrier operators to look into this matter and reconsider whether their vessels might be affected in certain circumstances,” says Rossen Panev. “There are many gas carriers trading today whose owners may not even be aware of the risk they are running. Some may believe their ships are fine because they don’t carry LNG or don’t exceed the 98 per cent fill level. They may be wrong. We want the industry to know that we now have this system that allows us to visualize the cargo tanks and simulate the damage condition of a particular ship and see what can be done.”
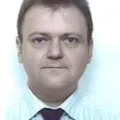
Rossen K. Panev
Principle Engineer ERS, Norway
- Avigator Fortuner – Shutterstock.com
- DNV, Hyeon Chul Lim
- DNV
- DNV, DSME
- DNV
View image copyright information