Ultramax 2030 – a team effort for eco-friendly design
The shipping industry is taking the climate challenge head on, and designers are combining the best green energy technologies and efficiency enhancements to set new records in eco-friendly shipping. A new joint project sets an example.
In response to the IMO strategy to reduce greenhouse gas (GHG) emissions, Oshima Shipbuilding and classification society DNV GL have signed a long-term strategic cooperation agreement to conduct research and development together on new bulk carrier designs. The first design, the “Oshima Ultramax 2030”, reduces the energy efficiency design index (EEDI) by 50 per cent. Developed together with technology group Wärtsilä, it was introduced at Nor-Shipping 2019 in Oslo.
Zero emissions scenario
With 2008 as a baseline, the IMO strategy aims to reduce total GHG emissions from shipping by at least 50 per cent by 2050, and to reduce the average carbon intensity, or CO2 per tonne-mile, by at least 40 per cent by 2030, while aiming for a 70 per cent reduction by 2050. Beyond 2050, IMO’s ultimate vision is to phase out GHG emissions as soon as possible within this century.
“To help the industry meet the ambitious GHG reduction targets set by the IMO, the industry needs to come together to advance ship design. This design halves the EEDI of comparable vessels, and sets a new standard for low-emission bulk carriers,” said Trond Hodne, Director of Sales & Marketing at DNV GL.
The strategic cooperation between Oshima and DNV GL will continue through 2030, working towards the IMO zero-emissions scenario with annual joint industry projects, where other partners will be invited to join.
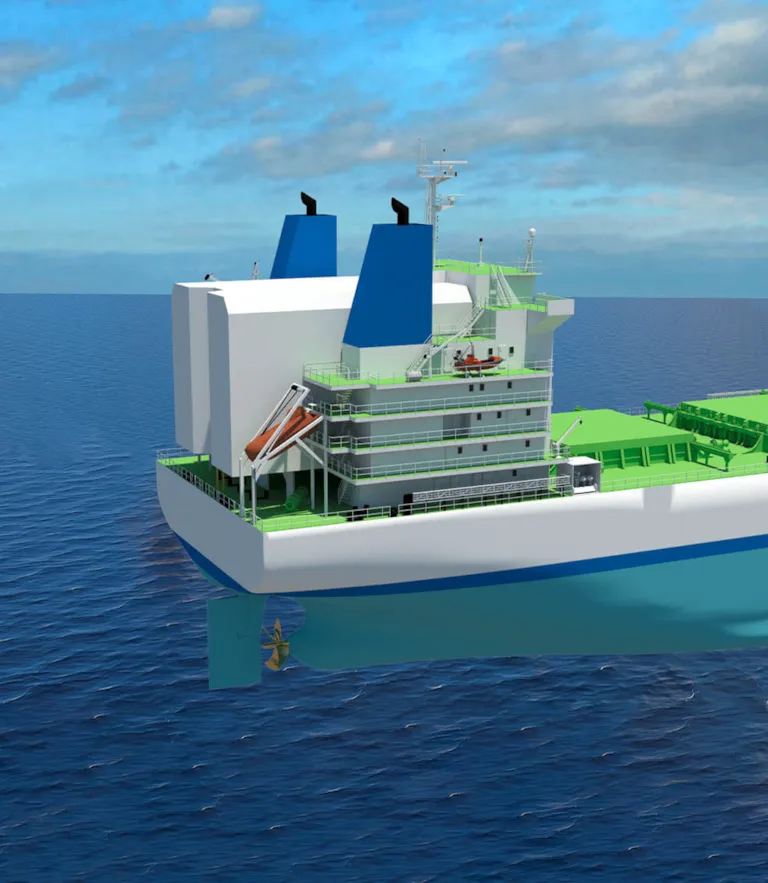
Meeting tomorrow’s requirements today
The Ultramax 2030 design maximizes operational performance while minimizing emissions by utilizing LNG as fuel, with an optimized hull shape and a hard sail to generate extra propulsion. In addition, the design uses solar panels and batteries to cover the hotel load during waiting and port operations. The array of options introduced in the new design includes a shaft generator with a battery pack and two different main engine alternatives. The first engine option is a high-pressure, two-stroke dual-fuel engine, while the second option is a four-stroke dual-fuel engine.
According to input from major shipowners, fleet profile research and automatic identification system (AIS) analysis of trade, ports, bunkering and cargoes, 40 per cent of major ultramax ports already provide access to LNG terminals, with more in the planning and building stages. Worldwide operation is the ultimate requirement for deep-sea ships using LNG propulsion, and current availability allows for bunkering of a 2,000 m3 LNG tank with the Oshima Ultramax 2030 design, giving a range of 13,600 nautical miles. This is enough to cover the main global trading pattern of a round trip from Singapore to South Africa.
A typical ultramax spends only just over 50 per cent of its time in sailing mode, while the remainder is spent either waiting or loading/unloading. The level of available shore power has only been estimated for two per cent of major ultramax ports.
With this in mind, particular attention was paid to reducing emissions while waiting and in port, in order to shrink the overall environmental footprint, not just while sailing.
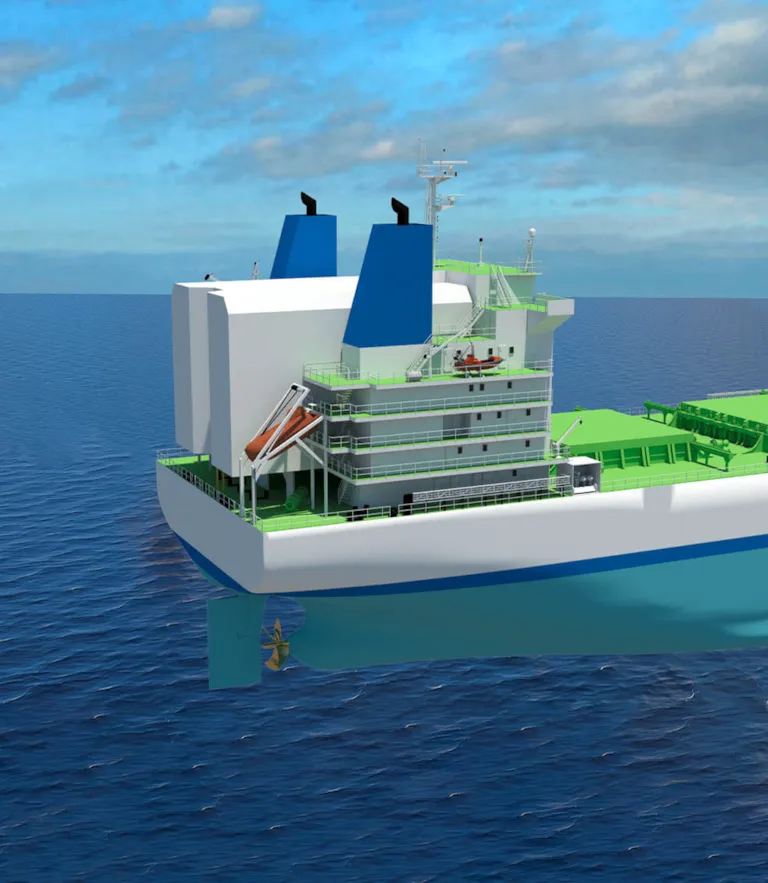
The power of the sun
Solar panels on the Ultramax 2030 design are installed on top of the hatch covers, and will generate up to 88 kWh during sunlight hours, with the remaining 42 kWh supplied by battery. This covers the expected consumption of the highly optimized hotel load of only 130 kWe in “Eco mode” during waiting times.
Total solar panel area is about 1,500 m2, including all hatch cover surfaces. The 88 kW/d output during day time will provide annual savings of an estimated 67,000 US dollars, including fuel and maintenance of gensets. The payback period for the solar panels and batteries is expected to be around ten years.
At night, battery power can be used for three hours before the battery is discharged. Whenever charging is required, diesel fuel gensets will run at optimum engine load to charge the batteries and cover the hotel load. About one hour is required to fully charge the battery.
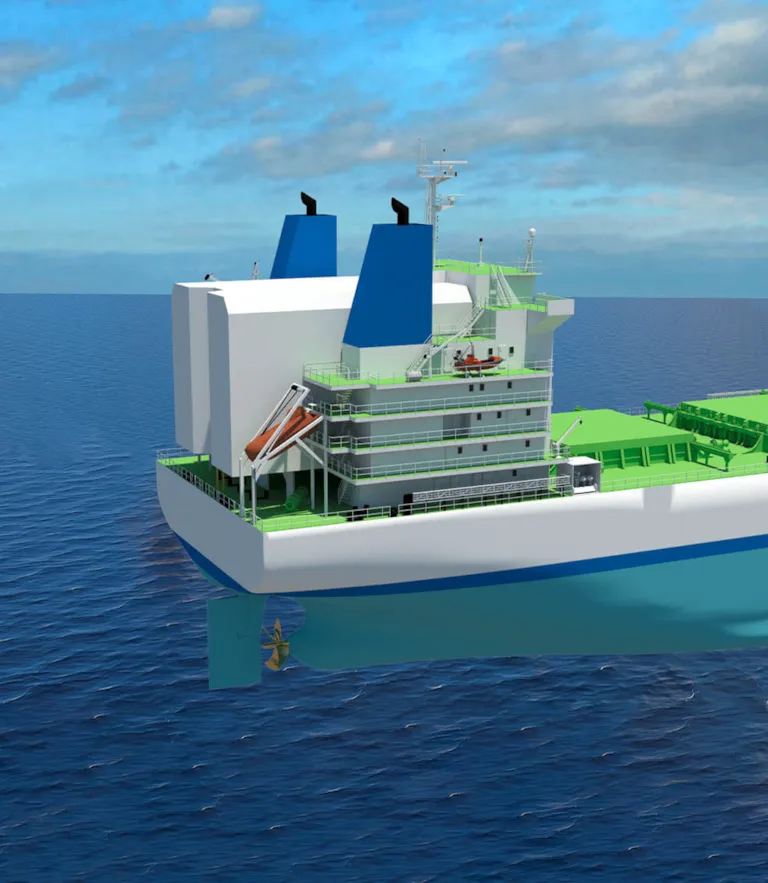
Sailing to savings
The glass fibre reinforced plastic hard sail generates additional thrust to supplement propulsion power. The sail automatically rotates to the optimal angle of attack to maximize thrust in response to changing wind conditions. The hard sail system is being developed jointly by Oshima Shipbuilding and Mitsui O.S.K. Lines.
Sail height is 60 metres, and the design satisfies Safety of Life at Sea (SOLAS) visibility requirements. The sail will be folded in unfavourable wind conditions and during loading and unloading. Oshima carried out computational fluid dynamics (CFD) analysis together with the University of Tokyo, using selected weather data for one year in the North Pacific. Expected fuel savings from sail use is up to ten per cent. Yearly fuel savings based on the current operational profile is estimated at 130,000 US dollar.
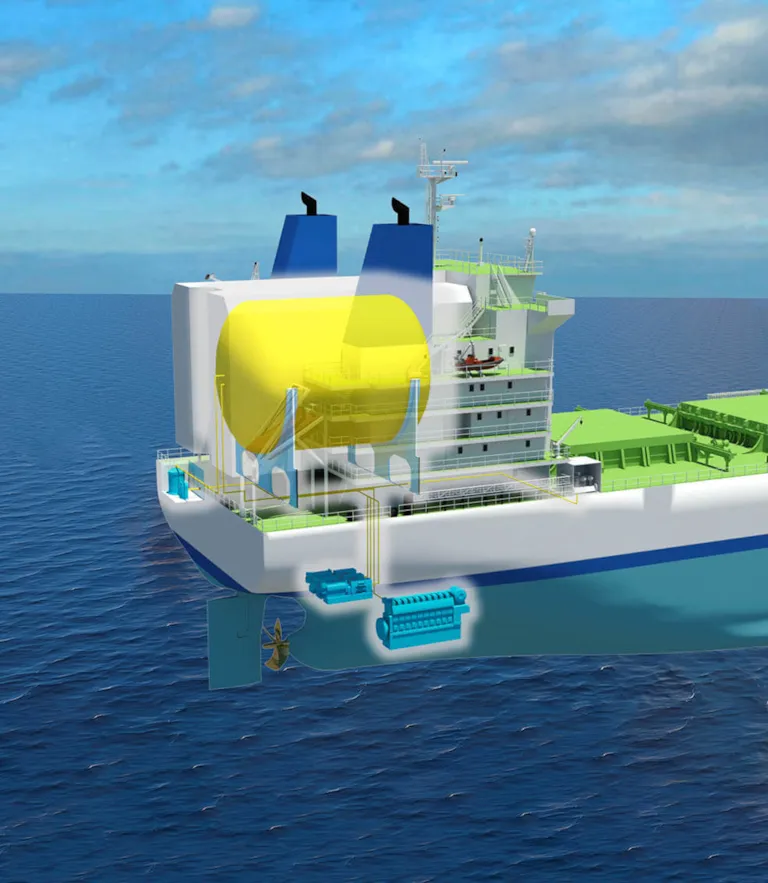
Energy Efficiency Design Index (EEDI)
The EEDI is a design index indicating the energy efficiency of a ship in terms of CO2 per tonne-mile at a specific draft and speed. The EEDI for new ships aims at promoting the use of more energy-efficient and less polluting equipment and engines. EEDI requirements were adopted as amendments to MARPOL Annex VI in 2011 and entered into force in 2013.
The minimum energy efficiency level in the EEDI is to be tightened incrementally every five years, with the aim of stimulating continued innovation and technical development of all the components influencing the fuel efficiency of a ship from its design phase. The choice of technologies for specific ship designs is left up to the industry. As long as the required energy efficiency level is attained, ship designers and builders are free to use the most cost-efficient solutions for the ship to comply with the regulations.
The EEDI covers the largest and most energy-intensive segments of the world merchant fleet. This means that ships responsible for approximately 85 per cent of CO2 emissions from international shipping are incorporated under the international regulatory regime, according to the IMO.
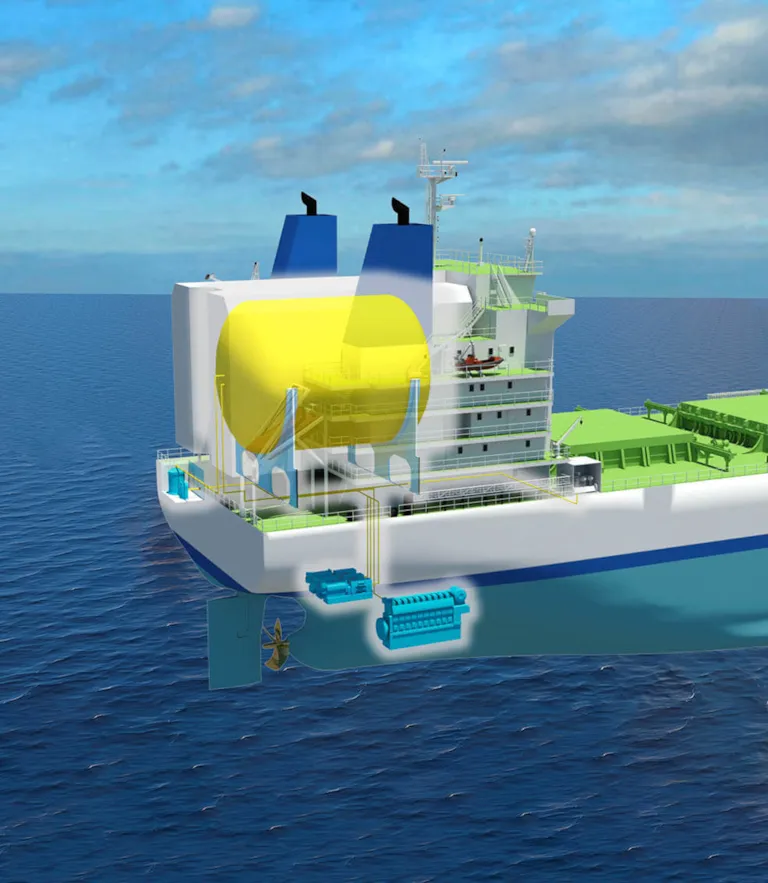
Making a greener future together
An additional aim of the Ultramax 2030 project has been to create a new standard that maximizes the return on investment (ROI) for the owner. One key objective was to minimize greenhouse gas emissions through the application of currently available technologies.
“Our smart marine initiative emphasizes collaboration between the various stakeholders, and this project is a prime example of how effective such collaboration can be,” says Stein Thorsager, Director, Merchant and Gas Carriers, Wärtsilä Marine.
“The design is based on actual operating profile data from ultramax bulk carriers, and incorporates an LNG-fuelled Wärtsilä 31DF dual-fuel main engine as one of the two engine options, connected to a power take out (PTO) shaft generator and controllable pitch propeller (CPP).
The result outperforms all existing designs in terms of efficiency and sustainability,” he stated. “Greater efficiency and better environmental performance have been made possible with the collaboration and initiative of Wärtsilä and DNV GL,” said Eiichi Hiraga, President at Oshima Shipbuilding.
“Oshima alone could not have come up with this new innovative design, which includes optimized propulsion, energy storage and solar panels. It represents a future-proof solution that will enable bulk carrier owners to comply with legislation while also lowering operating costs.”
Meeting such ambitious targets will call for significant technology development, a challenge both Oshima, already a leading designer and yard in the dry bulk segment, and DNV GL, the world’s largest class society, are willing to accept. “Our companies have significant and largely complementary know-how in the relevant fields of expertise necessary for such an ambitious development,” Trond Hodne concluded.
Morten Løvstad
Vice President, Business Director - Bulk Carriers
- Key image: Oshima
- Left side 2: Oshima
- Left side 3: Oshima