The right vibes
Stricter demands for noise and vibration aim to increase comfort and safety on board. DNV GL supports the Chinese shipyard GSI in achieving compliance.
For seafarers working on recently delivered vessels, life on board is about to get much quieter. A resolution passed by the IMO’s Maritime Safety Committee (MSC) incorporates the previous recommendation for noise on ocean-going ships into SOLAS (Safety of Life at Sea), thereby making it a mandatory requirement. MSC resolution 337 (91) aims to enhance crew well-being and safety by ensuring undisturbed resting times and therefore reducing the risk of accidents caused by fatigue. It applies to nearly all seagoing newbuilds (above 1,600 GT) with a building contract signed on or after 1 July 2014.
In addition, the certification body ISO replaced their guideline for measuring, reporting and evaluating vibration with regard to habitability on passenger and merchant ships with a new standard in 2016 (ISO 20283-5). While not mandatory, this standard implies a significant drop of the currently applied levels of acceptable vibration. “To give an example: the acceptable vibration level on a cargo ship’s navigation bridge has been lowered from 8 mm/s to 5 mm/s, and in the crew accommodation areas from 6 mm/s to 3.5 mm/s,” explains Michael Holtmann, Team Leader Vibration & Shock, Department of Structural Engineering, DNV GL – Maritime. “It may take some time for the new ISO standard to be implemented in shipbuilding specifications, but judiciaries and maritime authorities can already apply it in case of disputes or crew complaints about the vibration levels on board a ship,” he adds.
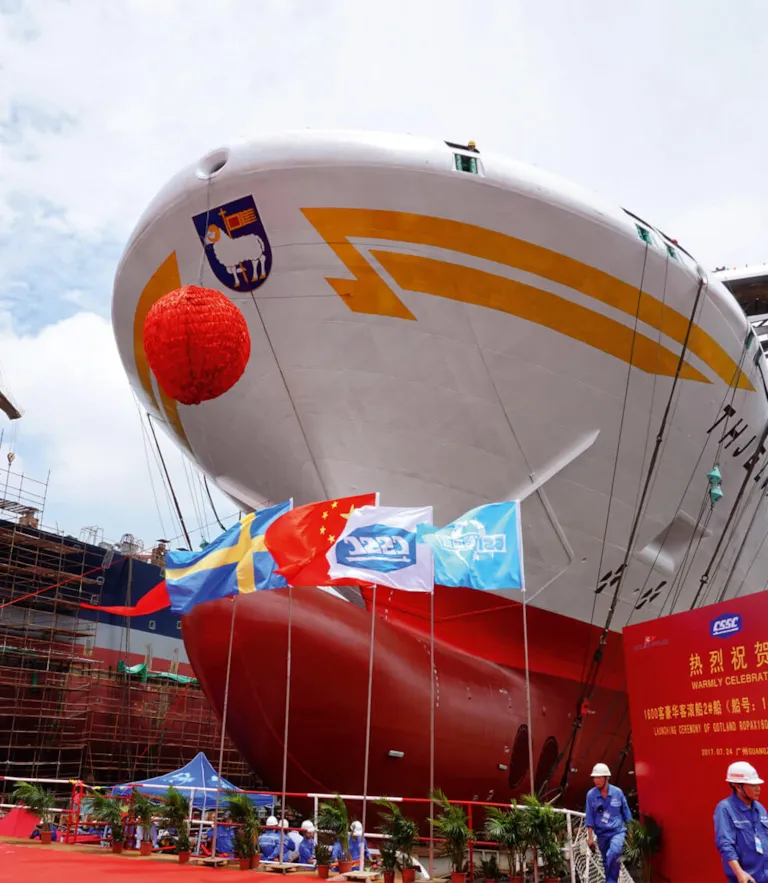
Sound pressure reduced by 56 per cent
Meanwhile, the impact of the IMO noise standard is already being felt across the shipbuilding industry. “Many of the ships that were first affected by the rule have recently entered into operation or are in the final stages of construction,“ says Stefan Semrau, Senior Engineer Maritime Advisory at DNV GL – Maritime. The mandatory directive requires the noise levels on vessels with a GT mark of 10,000 or above to be reduced by five decibel (dB) in crew accommodation areas, compared to the previous recommendation IMO A.468 (XII). This includes cabins, hospitals, messes, offices and recreational rooms.
“While five dB may not sound like a lot, this figure poses a significant challenge to shipyards, because the decibel scale is not linear. To put it into perspective: cutting the noise level by nine dB means the environment would be half as loud to the human ear. A reduction of five dB is equivalent to curbing the sound pressure by about 56 per cent,“ explains Semrau. He is one of DNV GL’s noise and vibration (N&V) experts in Hamburg. DNV GL has established dedicated N&V service centres in Hamburg, Høvik, Shanghai and Miami. In 2017, the company worked on 144 N&V projects around the world, 26 in China alone.
Using a fully numerical analysis (FEM), a statistical energy analysis (SEA) or a semi-empirical analysis during the early design stage, DNV GL experts work with shipyards to predict the level of noise and its propagation through the ship structure. “The main noise sources on board are the propeller, the main engine as well as the auxiliary engines and the exhaust gas systems,“ explains Semrau. “We also troubleshoot vessels in operation that have noise issues affecting the crew,“ he adds.
During the analysis, DNV GL examines the sources of vibration and noise, the sound transmission pathways and the insulation of the affected areas. “A fully numeric solution leads to extreme project costs. Therefore, classification societies rely on their experience along with databases of comparable vessel designs to create a statistical baseline for new analyses. DNV GL’s database is vast and contains projects from around the world. This puts us in an excellent position to offer accurate noise predictions,“ Semrau explains.
One of the most difficult areas to analyse is the propeller, as the design is tailored to a vessel’s specific requirements. “We invented the Tip Vortex Method to overcome this problem. It creates a digital model of the propeller to simulate its flow parameters. We can then compare these parameters to similar models in our database to get an accurate noise prediction,“ Semrau adds.
A strong partnership in China
“The reliability of DNV GL’s analyses is the reason why the company has been our main partner in N&V control since the 1990s. In the past five years, we have worked together on more than 15 N&V projects,“says Hao Chen, Chief Design Officer at Guangzhou Shipyard International Company (GSI). “Investing in reliable N&V analyses early on saves significant costs that can occur at a later stage, for example if the noise levels exceed the specifications during sea trials. We believe that DNV GL has the most knowledge and experience in this field, and our cooperation makes us confident that our newbuilds excel in N&V control,“ he adds.
“GSI’s holistic approach to tackling N&V issues and the cooperative attitude of both its technical staff and the management have made this a great partnership for us as well. We look forward to continuing to support GSI in the future,“ says Xiaofeng Jason Liu, Head of TCC Maritime Advisory China at DNV GL.
One of most recent N&V projects GSI and DNV GL have worked on is the LNG-powered ro-pax ferry Thjelvar. Ordered by Swedish owner Rederi AB Gotland, this DNV GL-classed vessel will be able to carry 1,650 passengers and will undergo sea trials at the end of 2017. “Making sure the vessel’s design complied with the new N&V requirement was not a big challenge for us, as GSI also builds passenger and research vessels, which have to comply with even stricter noise requirements,” explains Chen.
In October, DNV GL awarded the SILENT certificate to GSI and Xiamen University for the recently delivered oceanographic research vessel Jiageng. It is the first time this certificate has been awarded to a Chinese-built vessel. “This has been a very demanding project due to the ambitious requirements. However, through excellent collaboration between the owner, yard, designer and DNV GL, we were able to achieve compliance with the rules during the first sea trial,” said DNV GL Senior Principal Engineer Kai Abrahamsen.
The DNV GL SILENT class notation (see box below) is voluntary and covers underwater noise emissions. However, for owners operating regular cargo ships, N&V control on board is at the top of the agenda.
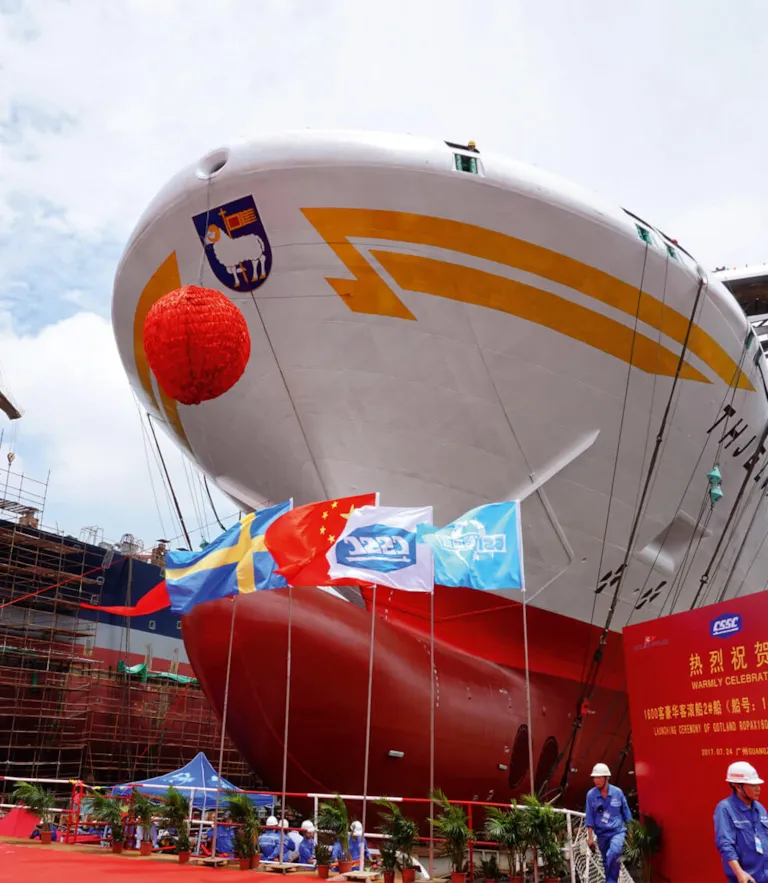
How to push down the volume
Small container vessels just above the 10,000 GT mark are one of the vessel types that has been most affected by the new mandatory IMO standard, because they are designed with high engine power and the accommodation areas are close to the main noise sources. Without modifications to the design, many would not fulfil the mandatory requirement.
However, there are several things a yard can do to dampen the noise: “Floating floors are one of the main measures we recommend. This means you add a layer of mineral wool onto the vessel’s steel structure and then top it off with another level of steel or cement,” says Semrau. Floating floors effectively reduce higher frequency noise, which can come from sources such as exhaust gas systems. Lower frequency noise portions can be reduced by installing so-called damping tiles. This method involves glueing on a second layer of steel.
The main challenge with this is time. “It is important to consider the impact of N&V from an early design stage and to look at every structure’s potential effect on N&V. For example at GSI, even the design of the hull line, which usually focuses on efficiency, considers the impact on the vessel‘s N&V performance,“ says Chen. Semrau agrees: “Taking a holistic approach to N&V control and factoring in potential measures as early as possible is the best strategy for achieving compliance and minimizing additional costs.“

Stefan Semrau
Principal Engineer