A new, open industry standard for 3D model-based class approval
As the shipping and shipbuilding industry makes great strides in digitalization, there are more opportunities for classification to streamline and accelerate its approval processes where the use of 3D models instead of drawings has become a reality.
To date, plan approvals for newbuild projects have been based on conventional 2D drawings. Since most designers use 3D modelling software, however, the obvious next step is to extract the information needed for design approvals directly from these models and perform the entire review process digitally instead of manually. The challenge is to standardize the format and process for submitting design data to class for approval to overcome compatibility issues.
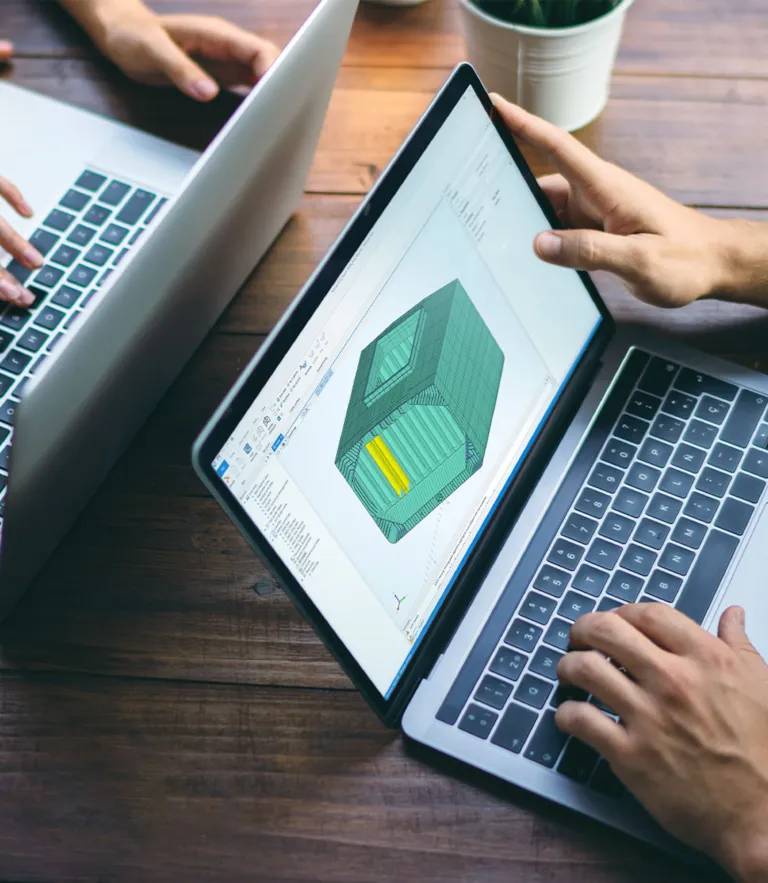
Joint research project develops a concept
In 2016, DNV initiated a joint industry project involving design offices, CAD software developers, The Research Council of Norway (NFR) and other partners to develop a concept for using 3D models as design documentation for verification.
The result is a model-based class approval and verification scheme for newbuild projects, enabled by a cloud-hosted digital model sharing platform. Cloud-based collaboration benefits from the “single source of truth” principle, eliminating media breaks, duplicated data entry, data quality issues and wasted work.
“The main drivers behind a model-based approval process and a digital workflow between the stakeholders during the design stage are reduced time to market, improved quality and traceability,” says Ole Christian Astrup, Senior Principal Specialist at DNV Maritime who headed the project. CAD models have been used in the engineering industry for some time to communicate designs to manufacturers, builders, maintenance companies and regulators.
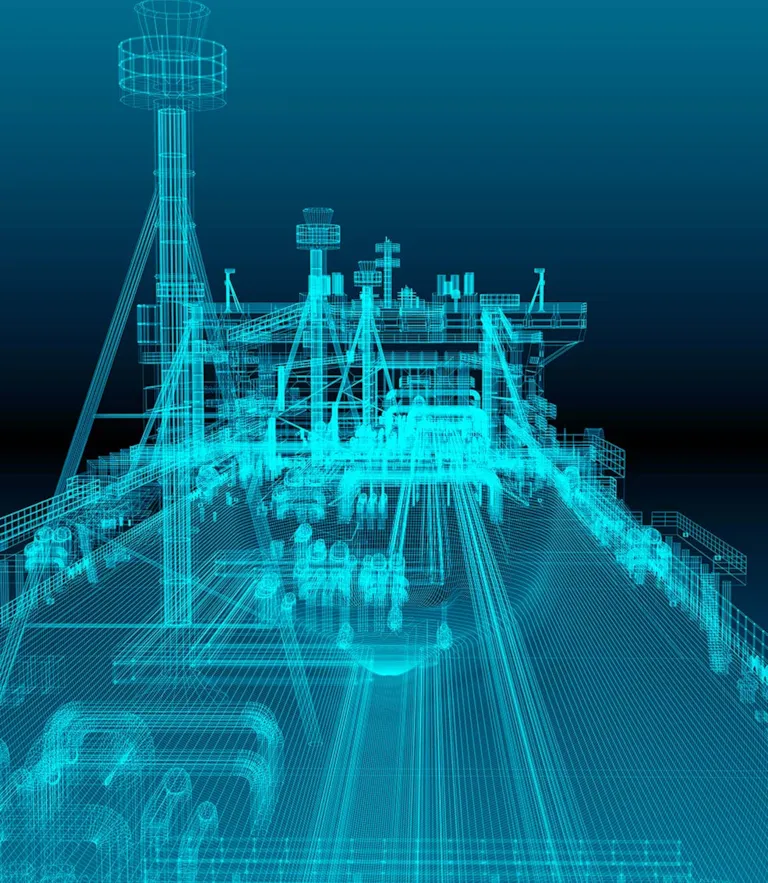
The key: The Open Class 3D Model Exchange (OCX) format
Developing an open-standard exchange format to ensure interoperability across all the different CAD software applications and allow class to review models generated by many different CAD tools was a key activity of the JIP. The result is the Open Class 3D Exchange or OCX standard.
To ensure neutrality and avoid the emergence of multiple incompatible exchange standards, an independent consortium was established to industrialize, promote and maintain the OCX standard. A number of classification societies including DNV, Lloyd’s Register, Bureau Veritas, Korean Register, Türk Loydu as well as major Computer Aided Design (CAD) providers have joined.
“For the classification societies to succeed with 3D model-based approval and reap its benefits it is instrumental that OCX becomes a recognized industry standard. If this is to happen, the maritime industry must cooperate and work together to implement and use the standard. Therefore, DNV has taken the initiative and established a joint OCX consortium with participation of the major classification societies and the maritime industry,” says Geir Dugstad, Director of Ship Classification & Technical Director at DNV Maritime.
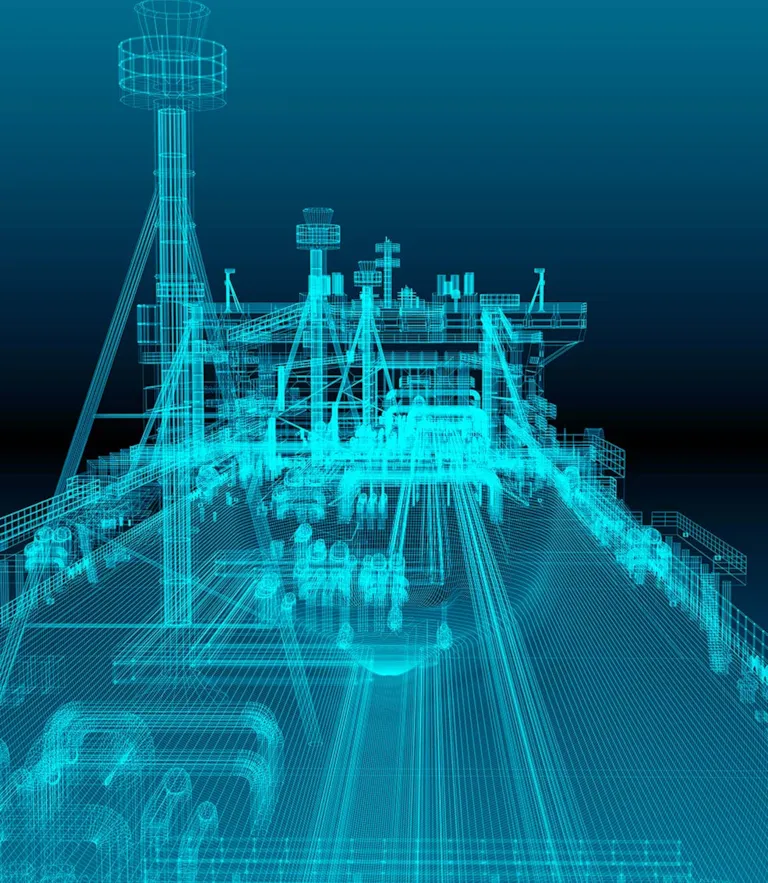
Successful pilot with DSME and NAPA
The new 3D approval platform and the “design-centric work process” were piloted by DNV, NAPA and Daewoo Shipbuilding & Marine Engineering (DSME) in a three-party Joint Development Project (JDP) for a very large crude oil carrier (VLCC) designed by DSME. The 3D OCX model fully eliminated the manual 2D modelling tasks, providing a seamless exchange of the 3D model between the CAD system and the DNV calculation tool Nauticus Hull.
The JDP successfully demonstrated that the VLCC model designed by DSME using NAPA Designer can be reused by Nauticus Hull providing an instant calculation assessment of any part of the 3D model. This also benefits the yard, which will save time by avoiding the tedious creation of the calculation models necessary for steel weight optimization.
DNV and NAPA are developing a new 3D OCX integration between NAPA Designer and Nauticus Hull, which allows the designer to verify their design directly in NAPA. “As a software vendor of tools for the early ship design phases, NAPA sees great potential in the current and future development of OCX. Instead of having individual interfaces between different software packages, the OCX concept opens up new possibilities to utilize best-of-breed tools, which will boost the digital transformation of the shipbuilding and ship design industries from classical drawing-based design towards seamless information exchange using a 3D model. NAPA offers full support for import and export of OCX data and is looking forward to its expansion becoming the world-wide standard,” says Mikko Forss, EVP, Design Solutions.
In the future, the entire process may take place on the cloud-hosted exchange platform integrated with the DNV customer portal. The design firm or the design department of the shipyard must first convert their CAD model to the OCX exchange format using a software interface, then upload it to the DNV portal where it is automatically verified against the DNV rules by the rule calculation tool. The output highlights the design parameters that were not accepted along with the rules that were violated and is saved with the model. The designers can instantly access the annotated model and stream it back to their desktops. “This is still into the future,” says Astrup. “But it is technically fully feasible and once again the key enabler is the OCX exchange format.”
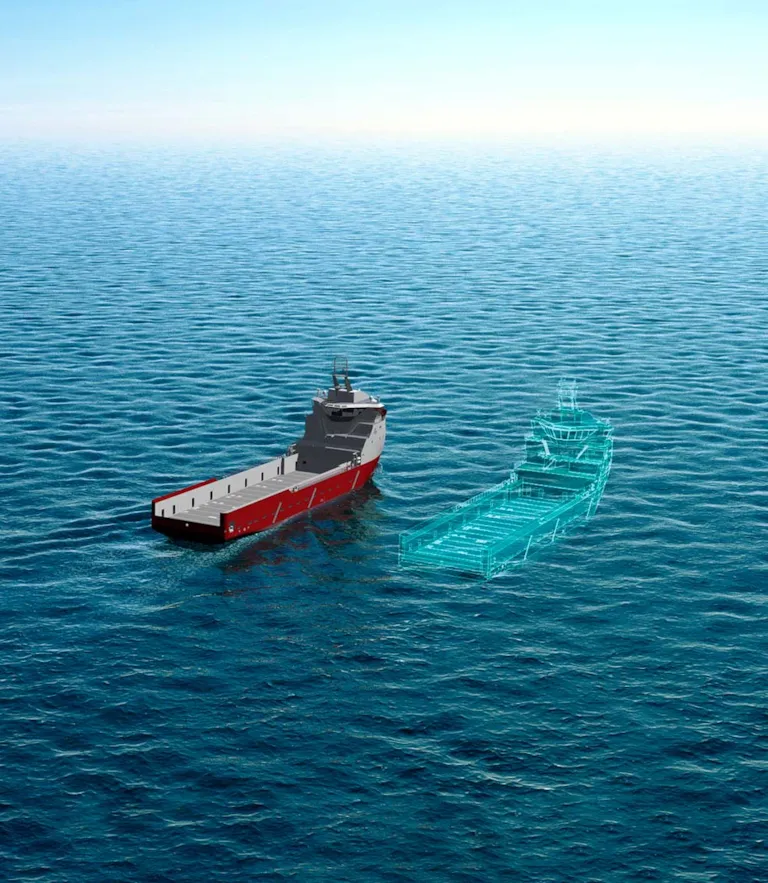
Browser-based visualization
When designers or yards replace 2D drawings with a 3D model as design documentation, the stakeholders will need a new tool to visualize and inspect the 3D model. For this purpose, DNV has developed the CAD-neutral, web-based browser “Sesam Insight” to visualize OCX 3D models. For full visual verification the participants in the process can use “Sesam Insight” to view, enlarge, rotate and annotate the OCX model. Engineers can compare various design revisions in several iterations to verify the direct consequences of modifications and optimize the model progressively. “One great aspect of this approach is that no files need to be sent forwards and backwards,” says Astrup. “There is no need to sit at a customer’s CAD system together; the platform allows both sides to maintain a constant dialogue about the 3D model.”
Once the CAD design has been updated based on the feedback from DNV, the final model is converted to the OCX format again and submitted formally for approval.
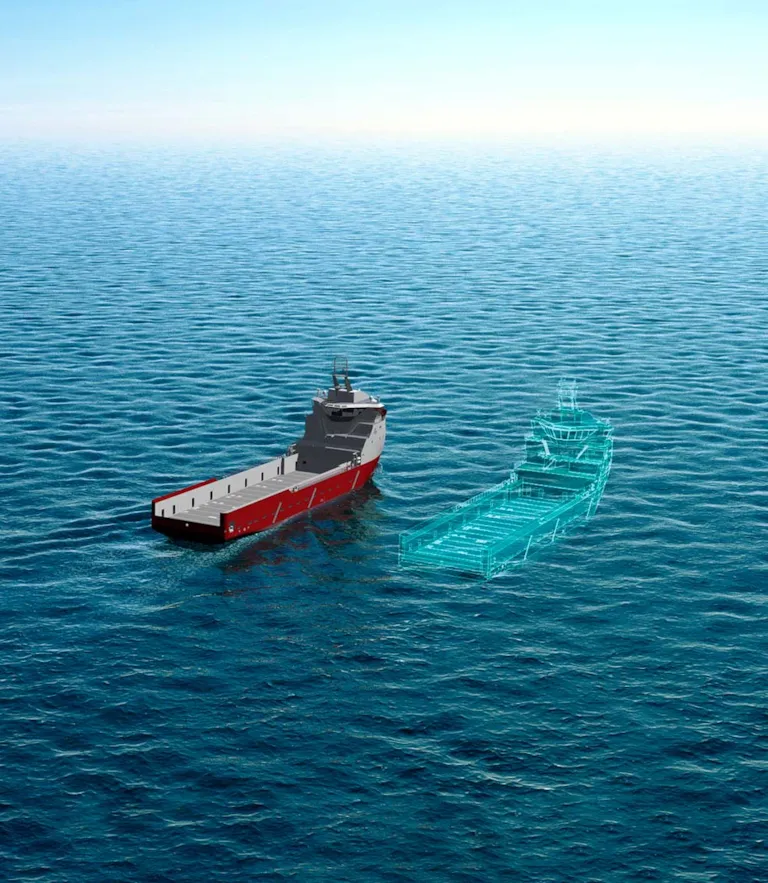
Multiple benefits for newbuild projects
“Using 3D models for approval offers multiple benefits to both the designer and the class society,” explains Astrup. “First of all, it spares the designers the manual effort of creating calculation models, normally a large portion of the design process for the hull structure. It also lets class take a look at a design ahead of time to give feedback before the actual approval process, providing an opportunity for very early feedback and optimization. Of course, a design must have a certain maturity before it can be verified, but this step-by-step approach gives the customer a decision basis earlier in the process and considerably accelerates iterations and optimizations.”
Duke Lee, technical director for hull basic design at DSME, comments: “We are developing a 3D model-based design procedure using NAPA Designer to improve our design capability as well as engineering competitiveness. As our 3D model can be used for class rule checking and can be submitted to class for approval using the 3D OCX format, 3D OCX can be very helpful to both DSME and class.”
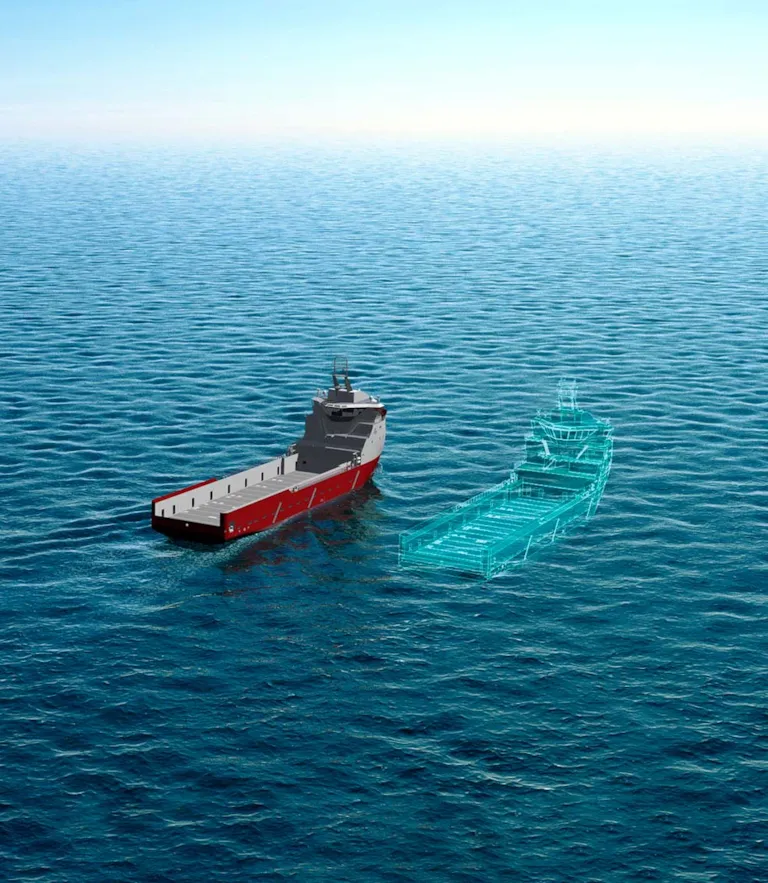
The virtual twin is born first
“The 3D OCX model provided by the customer can be used for streamlining and automating the approval services for other disciplines than hull, which can be a big time saver. To use the 3D model to streamline the whole plan approval process is a natural next step.” The shared 3D model – essentially the birth of the virtual twin before the “real twin”, the actual ship, is born – also opens up many downstream opportunities for managing the fleet in service, Astrup continues. To be able to reap these benefits, he stresses, it is essential for both the class and owner to obtain the rights to use the model from the yard or designer as the owner of the intellectual property rights in the CAD design. “DNV can take on a mediator role between yard and owner to help clarify the copyright question,” he says.
Considering the enormous benefits to the design verification and approval process and the commitment of several major class societies to its support, Astrup hopes that OCX will become the unified standard for the entire maritime industry in the near future.
Ole Christian Astrup
Senior Principal Specialist
- Rymden – Shutterstock.com/DNV
- LaNataly – Shutterstock.com
- OCX Consortium
- DNV
- DSME
View image copyright information