New rules for MOUs – Classification for smarter operations
The traditional class and statutory survey regime consisting of annual and five-year cycles has been shown to be too rigid for mobile offshore units (MOUs). Leveraging advanced digital technology, DNV GL’s revised Offshore Rules published in January 2018 provide much more flexibility.
The road towards digitalization in the offshore industry is long and many steps need to be taken to ensure safe and smart operations. Yet, there is an increasing need for new and alternative approaches to the cooperation between class and customer, especially with the aim of reducing “out-of-service” time. In response DNV GL has updated the rules for mobile offshore units (MOUs) in-service to make sure classification remains relevant and keeps abreast of new technologies and trends.
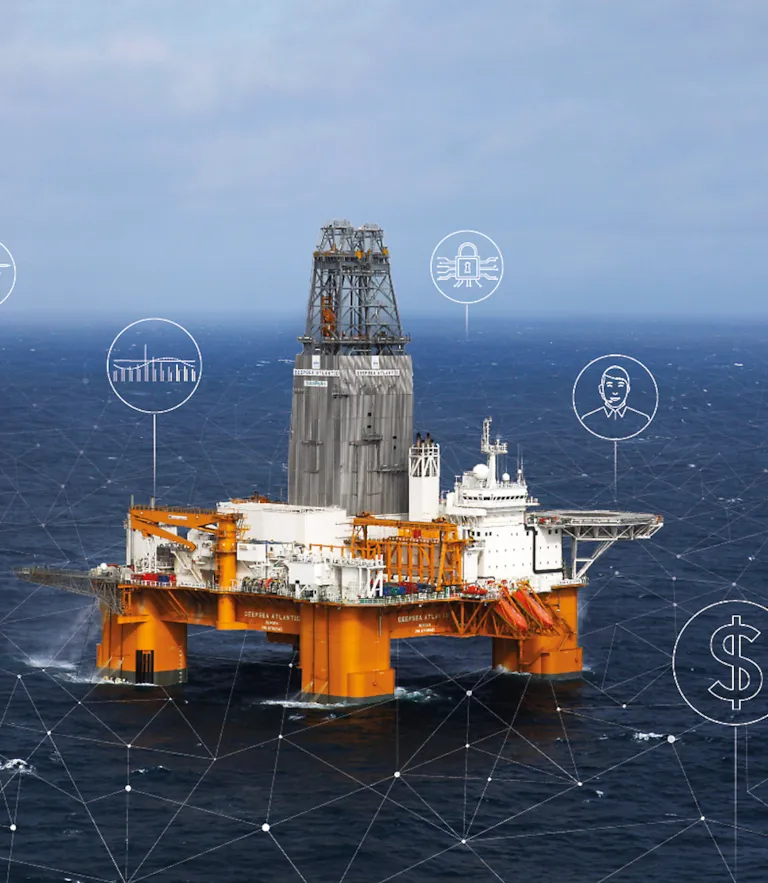
New, collaborative options
The new rules for MOUs in service introduce a new concept called “Classification for Smarter Operations”. Are Torstensen, Director Technology and Service Development, Offshore Classification at DNV GL, explains: “The main objective of this initiative is to find smarter ways of working to improve the utilization of assets, reduce downtime, and minimize the impact of testing and inspection activities.”
Classification for Smarter Operations takes a holistic approach, offering various arrangements and methods that may be selected in accordance with the company’s asset management strategies and plans. The concept promotes integration between class and owner by allowing the owner to take a more active role in testing and inspection activities, and by performing our classification activities on a continuous basis aligned with the actual operation of the unit.
A modern MOU generates huge amounts of data from various sensors every day. It is a challenge to get an overview of what data is available, select and collect the most meaningful information, and use it to determine the condition of various systems or pieces of equipment. Classification for Smarter Operations introduces alternative arrangements and methodologies for utilizing sensor data, including rules for data management and data quality.
For example, the concept supports the implementation of condition-based maintenance (CBM) for machinery, thrusters, drilling equipment, etc. by combining both predetermined (scheduled) and predictive maintenance (based on condition monitoring) and making use of sensor data and data analytics.
New technologies such as drones and other types of remote inspection techniques applied in structural inspections are a welcome means to determine the right time for the next inspection and avoid unnecessary downtime. Risk-based corrosion and fatigue management based on sensor data are other examples.
Another newly developed concept called Electrical Systems Integrity Management allows alternative test methods, such as fault simulations, isolation and local testing as well as built-in test functionalities, to be applied in the inspection and testing of electrical installations. These tests can be performed by the owner’s own, qualified personnel on a continuous basis, resulting in better coordination between the class and the owner while further reducing equipment downtime.
A solution developed for dynamic positioning (DP) provides for a distributed survey scope enabling continuous follow-ups. The scope of testing can be adjusted from year to year depending on operational activities. FMEA testing is spread over the five-year period. The owners have the option to have parts of the testing performed by their own specifically qualified personnel. This new testing and inspection scheme will serve as a framework and basis for further development of the DP survey, inspection and testing.
For lifting appliances, a new and efficient alternative inspection approach has been introduced under the name Condition Assessment. The inspections and tests can be optimized based on an analysis of the actual utilization history in relation to the design life of the lifting appliance. Accounting for the utilization history results in a more realistic inspection and testing schedule. “The new classification concept will provide a good basis for the new age of digitalization and further developments,” Torstensen believes, adding that these innovative tools and methods are just the beginning of digitalization in the offshore industry.
Henning Carlsen
Smart Class Development and Implementation Manager