How to sail the best yacht
Designing and sailing modern yachts involves engineering complexities that are difficult to resolve. DNV GL’s advisory services support owners in selecting and optimizing a wide variety of on-board systems.
On-board technology is getting more complex all the time as new, more advanced systems are added to improve operational efficiency, automate control functions, better protect the environment, and enhance comfort and the cruising experience.
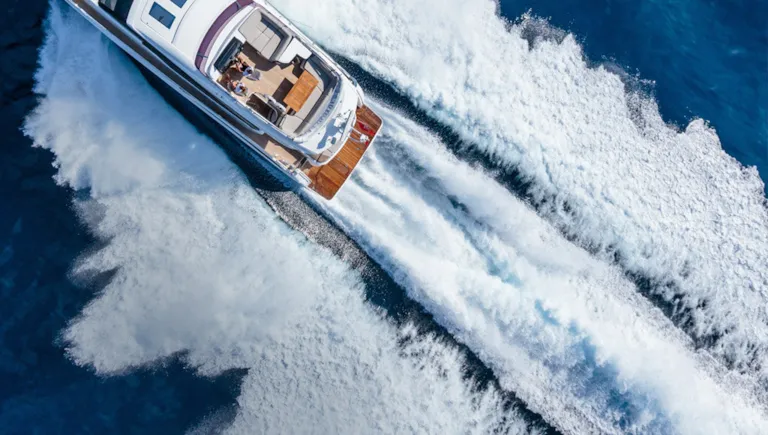
When rotating components rumble
The propulsion and power producing machinery is a universe of its own, and there are more choices than ever to consider when custom-designing the perfect system for a yacht — from diesel-electric or hybrid solutions and pods all the way to batteries and fuel cells. But all the innovative technologies and alternative fuels have repercussions on the remaining on-board ecosystem.
This is where DNV GL’s advisory services can make a big difference: its very purpose is to minimize risks and pinpoint crucial aspects that should be considered before any final decision is made. For example, if a customer envisions a newbuild with a hybrid propulsion system, there are experts available at DNV GL to assist in the development and evaluation of system specifications from a holistic perspective. Bid Evaluation and Hybrid Evaluation are software tools DNV GL uses to streamline the machinery selection and benchmarking processes ensuring all components work together to achieve the desired fuel and emission-saving or eco-friendly profile. This includes presenting the client with alternative options so the features and benefits will live up to the owner’s expectations.
Pinpointing the source
Noise and vibration on board are not only a nuisance to the passengers and crew but also typically indicate that energy is being wasted somewhere in the machinery and components are subject to excessive wear. Detecting the root cause takes experience and sophisticated equipment, and since every yacht is different, the right strategy for approaching the problem must be developed from scratch in nearly every case. For example, shaft and structural vibration measurements, combined with local vibration measurements in problem areas on board, may reveal the vibration source. Computer-based finite-element modelling can deliver further decisive clues.
In one such example, DNV GL was contacted when unfamiliar noises on board a yacht seemed to indicate trouble. It turned out that a stern tube bearing was overloaded due to poor design and inappropriate operation. The risk of loss of propulsion was evident if no corrective action was taken. The yacht had to be taken off-hire for major repair. Experts from DNV GL accompanied every step of the process, from root cause analysis to preparing a proposal for a new bearing design that accounted for the effects of hydrodynamic propeller forces, hull deflections and shaft line interactions with the hull and bearings, through to quality monitoring at the repair yard. Guiding all these processes carefully is important to minimize the off-hire time and make sure the repair costs will be justified by the improvements achieved.
Design assistance and vibration analyses, design and system verification, simulation and optimization, strength and fatigue analysis, alignment and in-situ measurements — the ultimate goal is always the same: to make mechanical and power systems run as smoothly as possible while minimizing the risk of failure.