From composite evolution to vessel construction revolution
Maritime applications of composites are varied and increasing. Two experts with a combined experience of 40 years discuss the future of composites, exploring whether they could eventually overthrow structural steel as the vessel construction material of choice.
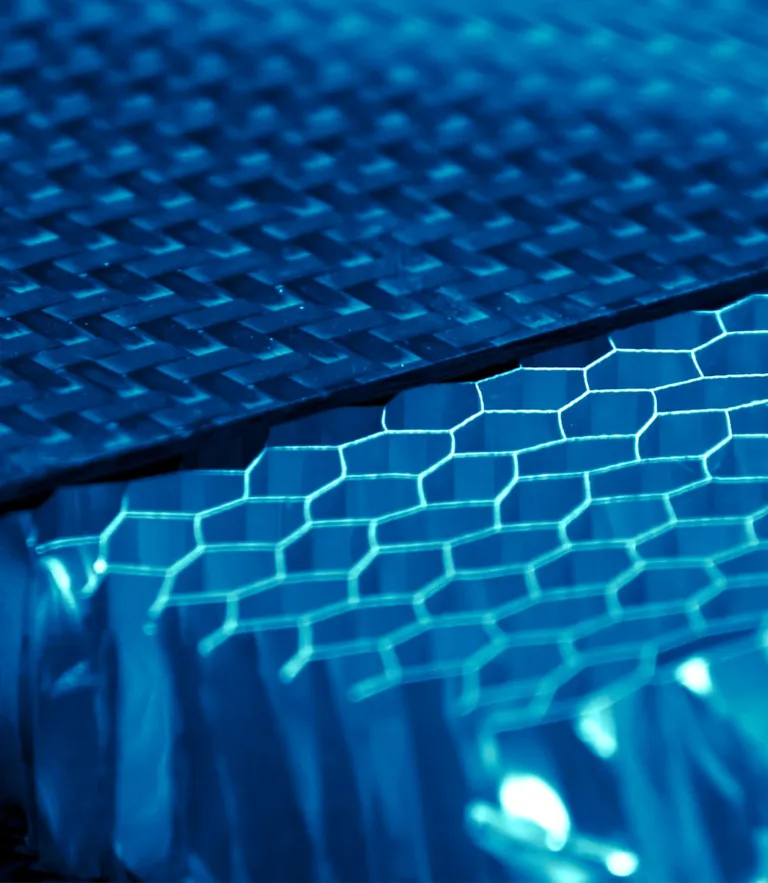
Long history of composites
“Composites have been around for thousands of years,” says Dr Philippe Noury, principal engineer, fracture mechanics and non-metallics at DNV GL – Oil & Gas, a naval architect and composites specialist who has spent more than two decades working with composites in the marine, oil and gas and naval industries. “Today you can find composites almost everywhere, from cars to planes and bicycles – the list is growing. In the maritime industry, the invention of glass and carbon fibre in the 1930s and 1960s respectively paved the way for the introduction of composites to the sector. In the 1970s their use really picked up, starting with high-speed leisure vessels made from fibre-reinforced polymer (FRP) composites.”
Dr Neil Little, technology and innovation director at SPS Technology, is part of the original executive team that took SPS Technology’s permanent composite – the Sandwich Plate System (SPS) – from a lab concept to a proven technology with more than 500 applications worldwide. He recalls one of the most significant early uses of maritime composites. “These composites were cement-based and known as thermo-cement constructions, which consisted of a steel frame that was reinforced with steel rods and then covered with chicken wire. This provided a template you could pour cement over and cure. The result is a very inexpensive composite mainly utilized in low-cost barges.”
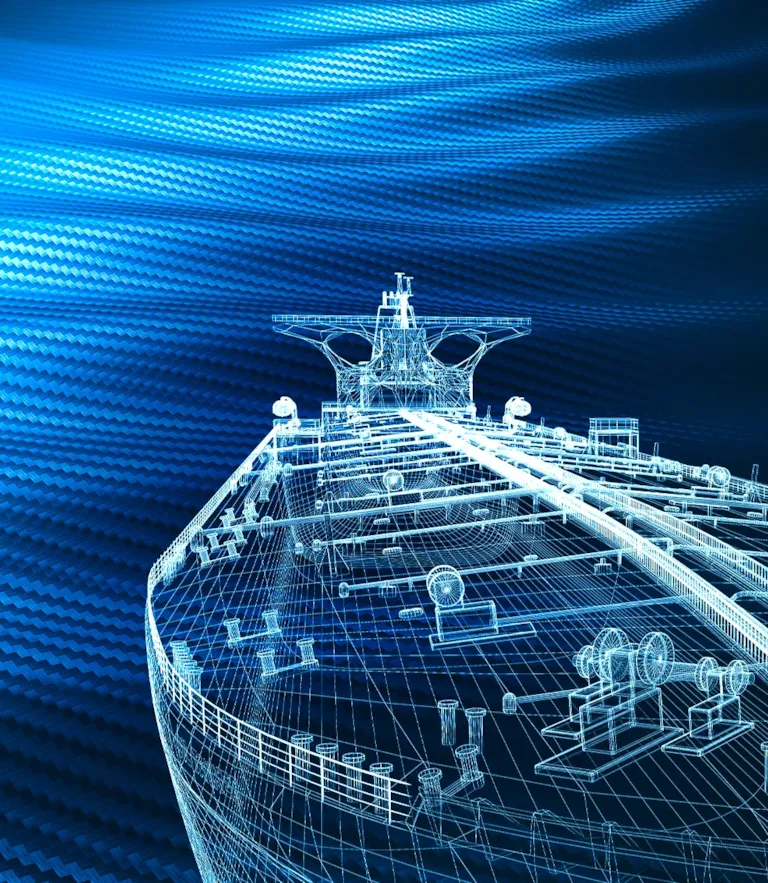
Most promising: Thermoset and thermoplastic composites
Fast-forward to today, and maritime applications of composites are varied and growing. Although there are many composite types, it is two solutions in particular which are generating the most excitement. According to Noury, thermoset (including SPS) and thermoplastic composites offer standout examples of the latest technology. “They are the driving force pushing the reputation of composites to new levels,” he says.
FRPs – as a thermoset solution – remain popular for leisure crafts, naval vessels below 80 m and submarine components. FRP thermosets and SPS are utilized in the repair, reinstatement and reinforcement of existing steel structures, replacing traditional crop and renewal or gouging techniques. SPS is currently the only thermoset solution utilized in the maritime industry and is comprised of two metal plates bonded with an elastomer core. To date, SPS has been used on projects involving many vessel types, including cruise ships, bulk carriers, tankers, ro-ros, floating production storage and offloading (FPSO) units and military craft, as well as many offshore rigs. Application examples include vessel decks, side shells and bulkheads.
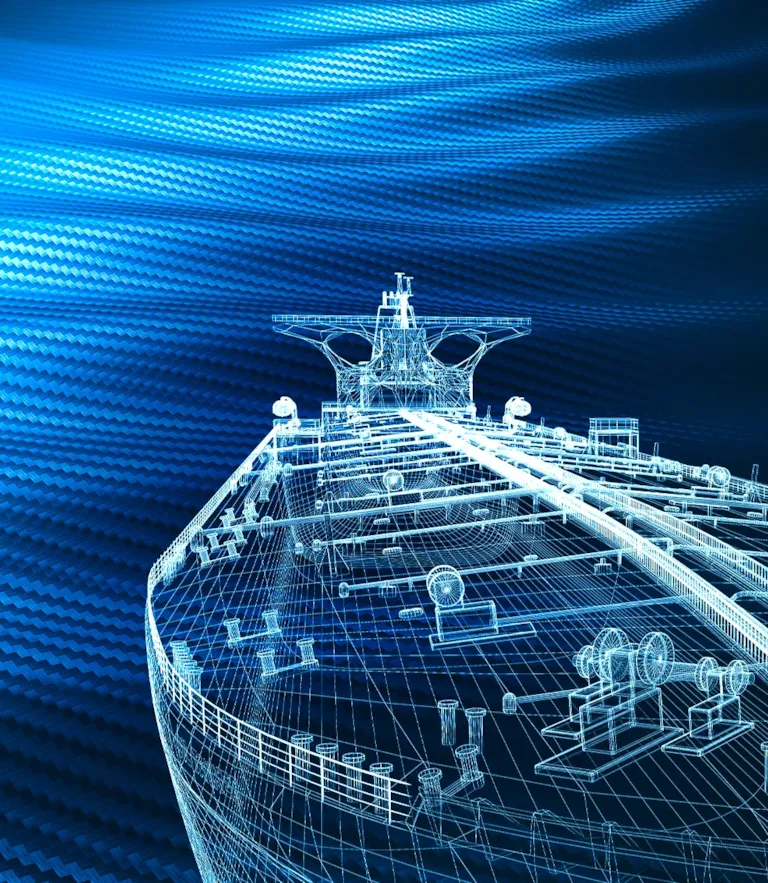
Withstanding the competition with conventional materials
Modern-day composites (including SPS) are cost-competitive with conventional building materials, such as stiffened steel, and deliver equivalent or even superior strength. They are significantly lighter and can often be installed without any “hot work”, reducing project risk, costs and duration. “You have a scenario where the faces of the construction (i.e. the exterior plates of the composite) are taking the load, and then the centre is making the structure very light and efficient,” says Noury. Importantly, composites also utilize advanced production techniques. “Lately, the industry has moved towards industrialized robot-type product systems which look very much like 3D printing in layers. Therefore, production has also greatly evolved, which has allowed this construction technique to become even more sophisticated.”
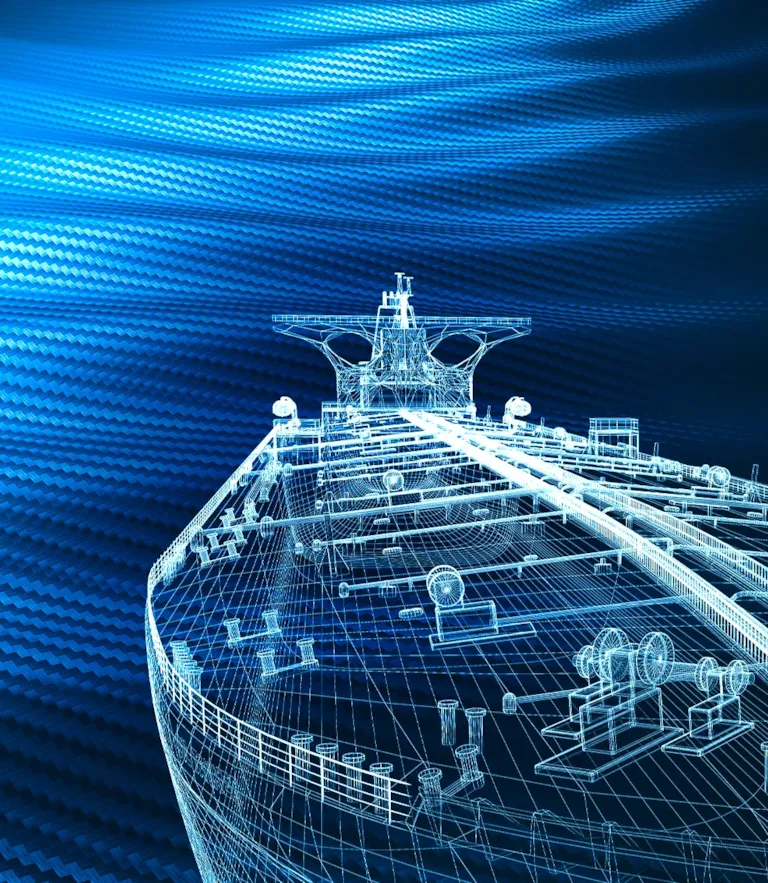
Proven fire safety of composites
While different types of composites offer a particular structural response, stringent fire safety assessments are a prevailing overall priority. In the early 2000s, Regulation 17 of the International Convention for the Safety of Life at Sea (SOLAS) made it possible for large commercial ships to use composites where it was possible to demonstrate equivalence of safety under alternative design and arrangements. The main deviation from the regulation was fire safety. “At the time, this was complicated because there was no clear guidance on how to demonstrate equivalent fire safety,” says Noury. “A lot of research was done and about five years ago engineers and scientists from several nations – under the lead of Sweden – succeeded in putting together new guidelines that were presented at IMO. These more detailed guidelines were finally adopted to help designers and national authorities demonstrate fire safety equivalence,” he says.
In parallel with this global-level work, Little and the team at SPS Technology spent the early 2000s working with the Maritime and Coastguard Agency (MCA) in the UK on a fire testing programme. This demonstrated SPS’s performance during a standard IMO fire test, with the findings presented to the IMO Sub-Committee on Fire Protection. Following the tests, a class society conducted a study on some of the SPS designs under SOLAS Regulation 17 in order to demonstrate the composites’ fire equivalence with stiffened steel. “The conclusion was that SPS was at least equivalent if not superior in terms of fire performance, when compared with insulated stiffened steel,” says Little.
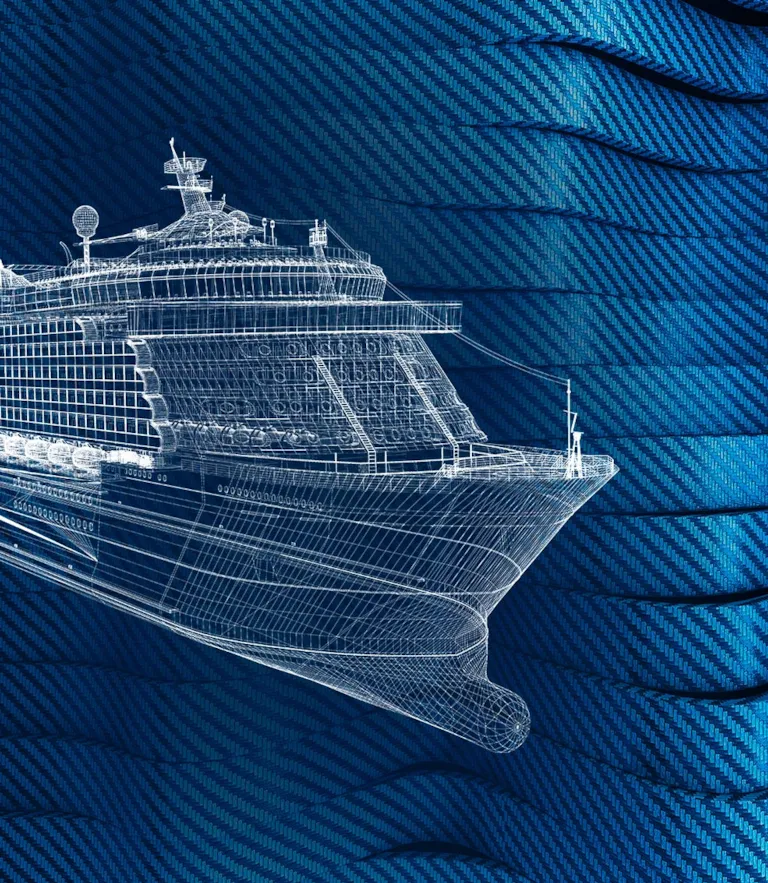
Understanding the risks and benefits to create acceptance
Notwithstanding the benefits of composites and the recent progress on regulatory hurdles, the pathway to widespread adoption still presents barriers. Key areas to address include enhancing foundational knowledge and opening up sufficient resources to demonstrate compliance with regulations on fire safety equivalence , which, despite recent clarity, remain demanding.
“In many current scenarios we have traditional shipyards, designers and national authorities that have little knowledge of composites, with many lacking the resources to enhance their understanding,” says Noury. “We must reach a position where everyone understands the risks but also, importantly, the benefits. Not just in terms of the technology, but also the business case.”
Little agrees, concluding, “It’s not just the technology, it’s the business case. It’s got to work economically for the shipowner, otherwise it isn’t going to happen.”
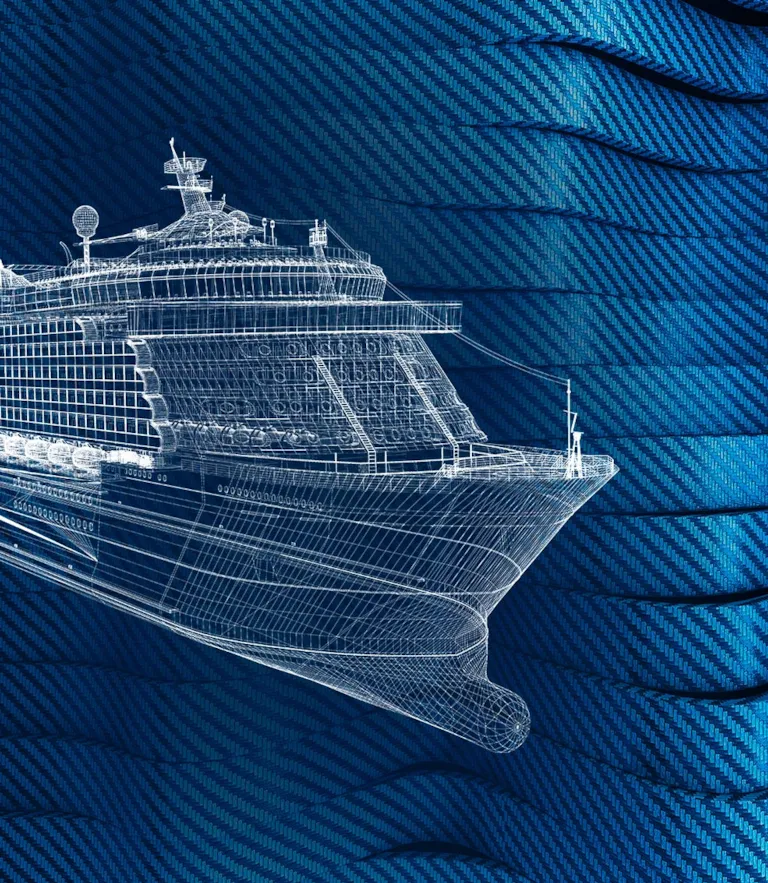
Newbuilding applications herald radical change
So, what does the future hold for composites? According to Little and Noury there are two main areas of growth. Firstly, the emergence of further newbuilding applications. Secondly, and more boldly, the creation of entire vessel structures constructed from composites as opposed to structural steel.
Currently, most composites are restricted to a few newbuild applications, rooted to small components such as decorative equipment on cruise ships. SPS Technology has however bucked the trend, having already utilized its composite to construct the escape tunnel on the Glen Lyon FPSO, as well as citadel access protection doors on more than 90 vessels. Other applications include funnel casings, cruise ship deck panels, modular impact protection decks and blast-resistant bulkheads. There is a strong appetite in the maritime industry to use composites for more newbuilding projects. For example, DNV GL is working on emerging applications of composites on hatch covers and tween decks. There are also several EU research projects underway that are looking to build vessels of up to 80 m entirely from composites. These include Fibre Ship and the Ramsses Project.
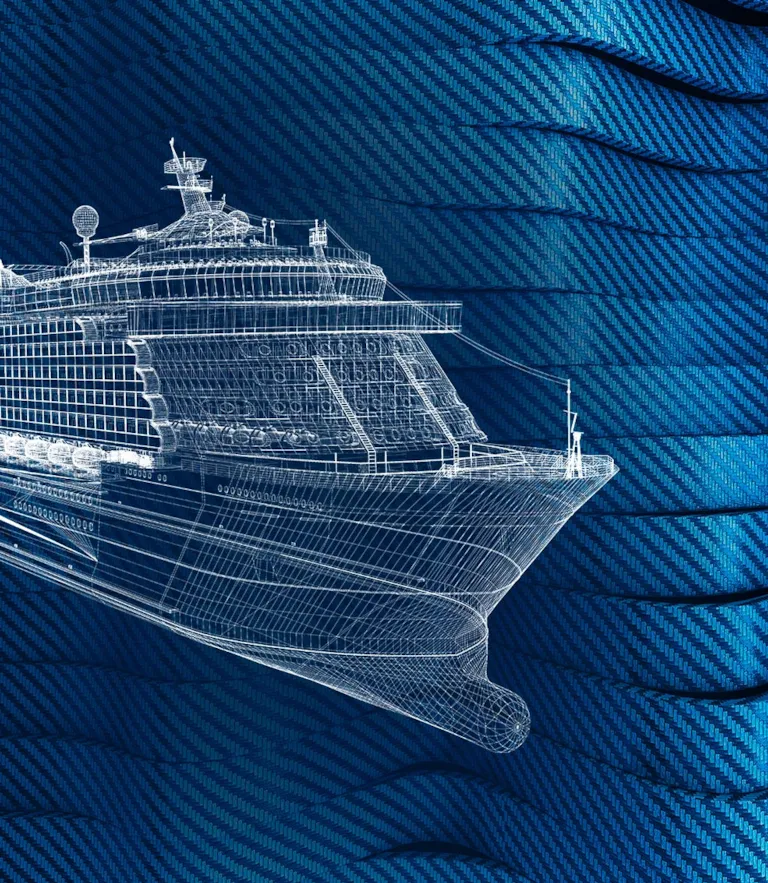
Autonomous ships as one future option to apply composites
Noury concludes: “There will be growth. It will be radical, but it will take some time. The first applications for newbuilds will be on low-risk applications and on medium-sized vessels. I see autonomous ships as an opportunity because of the low risk to life. Overall, I am optimistic. We moved from wood to steel and we will move from steel to composites. That’s for sure. You can’t stop technology.”
Summarizing his thoughts on the journey of composites so far, and what the future could hold, Little says: “The industry’s understanding of composites has already grown significantly. Twenty years ago, no one knew what SPS was, and then we went through a period where those who did understand it expressed a strong desire to see its proven performance, which is perhaps understandable in a conservative sector. Now SPS is very well established and has a great track record, with many structures already in service for more than 15 years. We remain highly motivated and determined to play our part in ensuring composite solutions gain widespread acceptance. They genuinely provide a real benefit in terms of performance and costs – I can only see the business case increasing.”
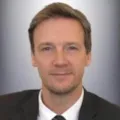
Philippe Noury
Principal Engineer
- TLaoPhotography – Shutterstock.com
- tiero - stock.adobe.com, Podsolnukh – Shutterstock.com
- SPS Technology
- archetype/Podsolnukh – Shutterstock.com