FellowSHIP project concludes 15 years of maritime battery and fuel cell research
After 15 years of extensive research, project partners Eidesvik Offshore, Wärtsilä Norway and DNV GL have recently announced the closure of the FellowSHIP project. It aimed to explore the use of battery, hybrid and fuel cell technology in the maritime industry.
“FellowSHIP has been a productive project,” says Bjørn-Johan Vartdal, Maritime Programme Director for Technology and Research for DNV GL Group. “Its results have shaped our knowledge of battery and hybrid power on board ships and enabled the industry to implement innovations which will help to enable the next generation of more efficient and sustainable vessels.”
The project partners started to explore marine fuel cell technology in 2003 and installed a prototype fuel cell on board Eidesvik Offshore’s Viking Lady PSV in 2010. While the fuel cell vision may have been ahead of its time in 2003, proof of concept and basic principles for maritime fuel cells were established that guided the industry through the next stages of development.
In the last phases of the FellowSHIP project, focus shifted to demonstrating the applicability of hybrid battery power systems, and the project signaled the charge to lithium ion batteries. Now, class rules have been established and the technology is fully commercialized; thus the partners have determined that it is time to decommission FellowSHIP.
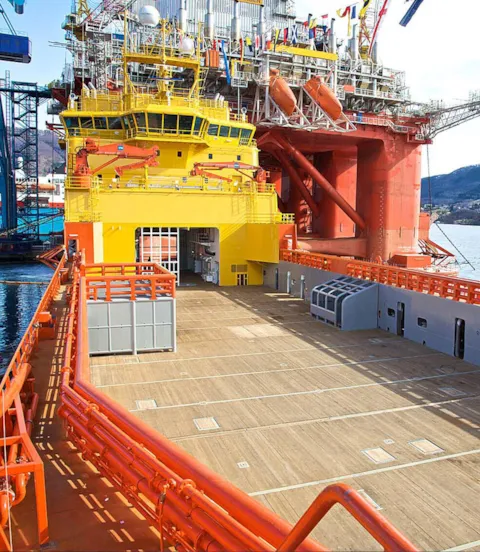
Learning by doing
The shift in focus to batteries came partly as a reaction to fuel cell performance: “Fuel cells had a slower response time, and we found that battery power could compensate for that,” says Bjørn-Johan Vartdal.
But interest in batteries quickly grew for other reasons as well: “Batteries became more interesting as an enabler, such as providing reserve power to meet redundancy requirements, and as an alternative to spinning power to handle variable loads, or peak shaving. Fuel savings of 15 per cent were also identified, with short payback periods,” Bjørn-Johan Vartdal reports.
The FellowSHIP project went on to document many other advantages of hybrid power in addition to fuel savings. Enhanced vessel performance, noise reduction and improved safety due to quicker response time were just some of the benefits achieved by combining battery power with fuel cell and LNG. But perhaps the most significant advantage has turned out to be emissions reduction.
“Viking Lady operates on LNG, and burning gas at low loads produces higher amounts of methane. Using batteries to cover low load requirements allowed us to reduce methane emissions,” says Øystein Alnes, Principal Maritime Engineer for DNV GL. This is among the reasons that the combination of battery and gas power is attractive; not just for the offshore fleet, but also for global shipping: “With the upcoming sulfur cap, gas will become more important. LNG or LPG will help companies meet clean fuel requirements, and batteries can help ensure the desired performance.”
The environmental advantages of batteries quickly became apparent, but safety had to be ensured as well. The FellowSHIP project provided the arena for calculating both elements. “The safety element is critical,” Øystein Alnes points out. “Batteries are a potentially risky component, and they must be taken seriously. DNV GL was the first to issue class rules for marine lithium ion batteries, and FellowSHIP defined our knowledge of battery technology.”
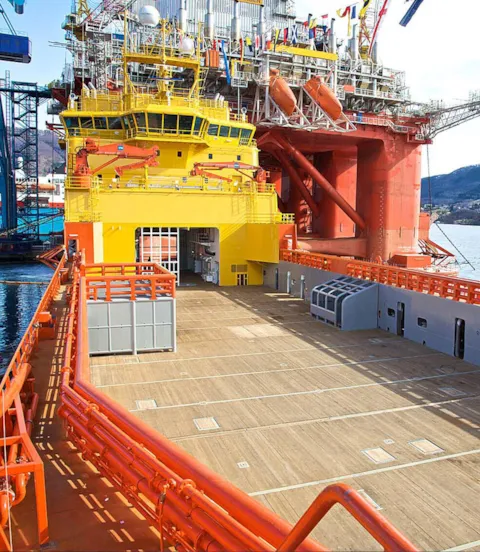
The start of something big
Vermund Hjelland, Vice President of Technology and Development for Eidesvik Offshore, credits the project for bringing batteries on board their ships. “Eidesvik is continuously searching for the most forward-looking, efficient and environmentally friendly ship designs and operational solutions for our fleet. Upgrading four of our ships with battery systems since 2016 would never have happened without the results, experience and knowledge obtained through the FellowSHIP project,” he concludes.
The Norwegian Research Council provided funding throughout the project period. Øystein Alnes maintains that groundbreaking public–private projects like FellowSHIP are essential for advancing knowledge of new technologies.
“FellowSHIP brought down barriers to commercialization of battery hybrid technology and helped to resolve safety issues,” Øystein Alnes says, adding that the project brought a higher level of awareness of the requirements and the possibilities for batteries to commercial shipping. “Developments in battery technology would have happened eventually, but everything has to start somewhere, and the marine battery revolution started with Viking Lady.”
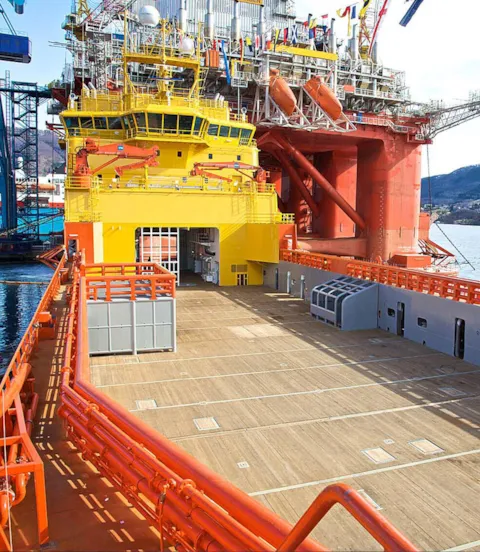
The cleanest ship wins
That revolution has now become institutionalized in many facets of shipping. “Low or zero emission propulsion is now a requirement in many tenders,” says Øystein Alnes. “Return on investment in batteries drove the discussion initially. Now, batteries are often the key to getting jobs, and demands from contractors have become a key driver for the industry.”
As the largest operator on the Norwegian continental shelf (NCS), Equinor has many reasons to appreciate the advances that the FellowSHIP project demonstrated to the industry: “Equinor’s ambition is to be a leader in carbon-efficient oil and gas production, and to reduce emissions from our logistics activities,” says Helge Såtendal, Principal Consultant, Supply Chain Management, Marine Operations. “Batteries on platform supply vessels allow for more efficient operation of motors, reducing CO2 and NOx emissions and lowering fuel consumption.”
Ingve Sørfonn, Head of Technology & Development for Wärtsilä Marine Solutions, Power Conversion, notes that the FellowSHIP project has been one of the important industrial projects for demonstrating, validating and documenting new, efficient and low emission technologies for the future. “The fuel savings and emission reductions achieved during the different phases of the project have been enablers for developing the maritime industry in a more sustainable direction,” he states.
Results from the FellowSHIP project were published internationally throughout the life of the project, contributing to the basic industry knowledge of hybrid battery systems. Bjørn-Johan Vartdal sums up: “The field is open now. Each supplier will find their own battery hybrid solutions, but FellowSHIP proved it was possible.”
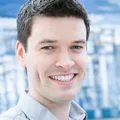
Øystein Åsheim Alnes
Principal Engineer