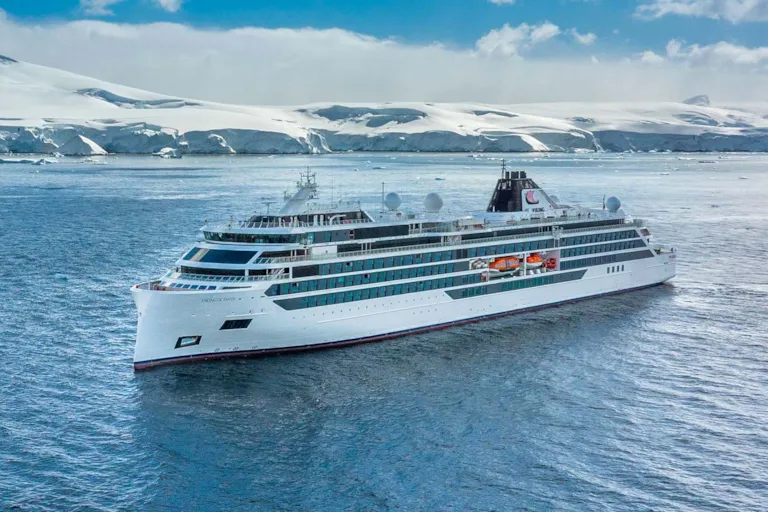
Diversification and flexibility: Building ships for net zero
Facing an unclear future regulatory environment, Italian shipbuilder Fincantieri commits substantial resources to research and development across all potential energy sources and propulsion technologies to offer owners flexible solutions for a variety of decarbonization pathways.
Featuring in this interview

Marco Bognolo, Vice President Basic Design, Merchant Ship Business Unit, Fincantieri
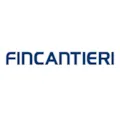
Marco Bognolo serves as Vice President of Basic Design in the Merchant Ship Business Unit of Fincantieri. Thanks to the extensive experience previously gained in various disciplines of the technical department, in project management and as senior designer for cruise ships, over the past decade he has been coordinating the technical definition of the prototype designs for passenger vessels developed by the group.
Mr Bognolo, Fincantieri is looking at a full order book. What is this success attributable to?
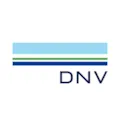
The first answer is diversification. Fincantieri does not rely solely on cruise ships; we have expanded into naval ships, the offshore sector and, more recently, land-based engineering, like bridges or the terminal in Miami. Today Fincantieri is a highly diversified engineering company. This enables us to adapt to a very volatile environment, which is key to survival. Serving a wide range of customers, we can deliver cruise vessels of any size and type, customized to operational needs and with different technologies on board. Another success factor is innovation. We invest in innovation so we can offer state-of-the-art products and keep pace with technological progress and the demand from the ultimate customers, the passengers.

Can you give our readers a brief overview of Fincantieri’s current newbuilding projects under DNV class?
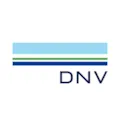
We are currently building two ultra-eco-friendly cruise vessels to DNV class for TUI Cruises, a joint venture between TUI AG and Royal Caribbean Cruises, which are scheduled for delivery in 2024 and 2026, respectively. These 160,000 GT (gross tonnage) LNG-fuelled ships represent an innovative concept developed by Fincantieri to minimize fuel consumption and environmental impact while offering an outstanding cruise experience. In addition, Four Seasons Yachts have ordered a 95-suite luxury cruise yacht to DNV class. It combines a dual-fuel MGO/methanol propulsion system and fuel cells and will have an ultra-low carbon footprint once green fuels are available. It will be delivered in 2025.

How do you ensure you meet different passenger demands?
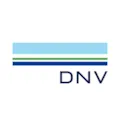
We have evolved from being a system integrator, building the steel hulls ourselves, to engineering and manufacturing many components such as cabins and public areas but also air-conditioning systems, electrical systems and batteries in-house so we can customize the product, control production and achieve full customer satisfaction. We want to be at the forefront in these sectors, managing the entire ship life cycle and strengthening our role as digital design authority and complex system integrator, including automation, data management and AI. This was highlighted in our 2023–2027 Business Plan, in which industrial sustainability is also another pivotal point. In response to recent challenges, we are also moving into emerging fields. During the pandemic we developed competencies in sanitizing systems to avoid the spread of viruses. This demand was entirely unknown and suddenly became particularly important for our customers. Another new focus is cyber security, for which we have established a subsidiary called E-phors.

Do you do your own research and development?
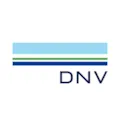
We have both a research and development department and an innovation department. Our R&D focuses on incremental changes in the basic and functional design of new projects. For major innovations opening entirely new technologies, systems or even markets, we have our innovation department. Pursuing both aspects allows us to be prepared for the challenges we will see in the next 10 to 15 years.

Can you give us a few examples of recent digital innovations?
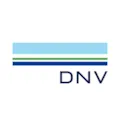
Our subsidiary Cetena, a research and consultancy centre in the naval and maritime field, develops software and pursues multiple engineering activities to bridge the gap between current and future design. For example, we have developed and certified an adaptive guidance system for safe-return-to-port scenarios which provides digital step-by-step real-time assistance to each crew member using tablets. This increases safety on board remarkably. Cetena is also working on an interactive digital energy management system which uses an energetic digital twin of the vessel and machine learning to provide suggestions to the crew how to operate the vessel in the most efficient way to minimize consumption and emissions.

What is your approach to the different alternative fuel options being discussed for shipping?
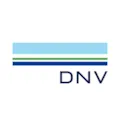
Realizing that the future in terms of alternative fuels, technologies and regulations is very volatile, our only option is to build competencies in all fields. This includes exploring zero-carbon fuels like hydrogen and ammonia as potential solutions in case the current tank-to-wake regulatory approach will prevail and the only way to decarbonize will be to have no carbon in the fuel at all. Three years ago, we completed an experimental fuel cell installation to fully understand this technology. If future regulations prefer a well-to-wake approach, biofuels or e-fuels could become the most viable solution.

What impact does that diversity have on vessel design?
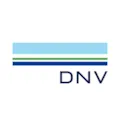
Looking at this variable scenario, we need to build and design projects with a great deal of flexibility. LNG is important today because in the current regulatory scenario it delivers a clear reduction in carbon dioxide emissions towards requirements like the EEDI (Energy Efficiency Design Index) or CII (Carbon Intensity Indicator). We need to build flexible designs that can operate on bridge technologies like LNG or methanol now and on other fuels or technologies in the future so that we can gradually minimize emissions.

How far do you expect fuel cell technology to take you?
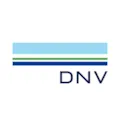
I do not see fuel cells taking over the entire energy supply required on a cruise vessel. It is not only a matter of total energy requirement but also operability. Based on our studies we now know that fuel cells are not capable of scaling a load ramp. They cannot react to sudden variations in energy load in the way an internal combustion engine can. I do not see a scenario in the future where we only have fuel cells. Rather, several technologies will be combined to cover the entire energy demand, for example fuel cells, batteries along with internal combustion engines to handle the demand fluctuations.

What future pathways do you see for LNG-fuelled ships built today when regulations tighten?
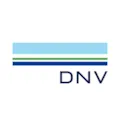
Several scenarios are imaginable. Some volumes of renewable LNG are already available today, and some cruise brands already use it as blend-in fuel. As long as the demand keeps increasing, I expect the availability of bio-LNG to increase as well. There may be a point in the far future where vessels will run on bio-LNG only and the regulation will have shifted from tank-to-wake to well-to-wake, and then we will be all set in terms of net zero. Another potential scenario occurs if the well-to-wake approach is not agreed. In that case we may have to opt for more complex solutions, for instance using LNG with fuel cells. A reformer would feed the fuel cells with hydrogen, and the resulting carbon dioxide would be captured.

How do you tackle the safety challenges that come with alternative fuels?
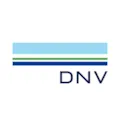
The companies of our group cooperate from the very beginning to ensure a safe product. We perform thorough simulations and hazard identification analyses during the pre-design phase of our projects. It is also important to involve suppliers and partner with class societies and flag authorities from early design stages because we need their expertise and capabilities during the definition of a new project to ensure we implement all possible mitigations.

Has class become more important over the years?
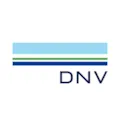
Yes. Ten years ago, class was a sort of third party, after the shipbuilder and the owner, responsible for approving drawings and configurations. Today we need DNV as a partner in the same team with the shipbuilder and the owner. The product has become central in this approach, and all the stakeholders cooperate to move in the same direction. We need DNV to provide ideas and suggestions and find solutions accounting for technologies, regulatory aspects, safety but also the owner’s requirements. In one recent example, we had a great preparation with DNV where we were targeting an entirely innovative design where neither of us had any related experience. By combining our own point of view as the shipyard, DNV the perspective of the class society, and by involving some suppliers, we came to the solution. This close cooperation is of paramount importance for successful projects such as those we are doing for TUI AG and Four Seasons.

How do you address supply chain decarbonization?
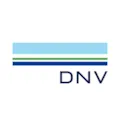
The emissions generated in shipbuilding depend on the kind of material being manufactured. We analyse our materials in detail and identify areas where we could use more beneficial configurations to reduce the emissions within scope 3 upstream but also scope 1 and 2. On the other hand, we cannot change the fact that ships are mostly made of steel. Metal production has unavoidable intrinsic emissions. All we can do is buy as much steel as possible from companies which compensate their emissions. The situation is similar with other materials. We have developed a model to precisely calculate the emissions for each material used. Interestingly, when we look at the entire life cycle of a cruise ship, only 4 to 5 per cent of the lifetime emissions are attributable to construction. Ninety-five to ninety-six per cent of the emissions are downstream. So, while it is important to look at the upstream part, most of our efforts are concentrated on reducing the downstream emissions.
