DNV GL tackles shaft bearing challenges
DNV GL has revised the main class rules for single stern tube bearing installations and now offers new optional shaft alignment class notations.
In the wake of a reported upsurge in stern tube bearing failures, DNV GL has revised main class rules for single shaft bearing installations and introduced two optional shaft alignment class notations: Shaft align(1) and Shaft align(2). The revised rules for single-bearing installations, included in Part 4, Chapter 2, Section 4 of the DNV GL Rules, mitigate the impact of potential influencing factors behind the failures, while a recently announced joint research project into environmentally acceptable lubricants (EALs) will investigate the performance of biodegradable lubricants compared to traditionally used mineral oils.
Both notations can be assigned to newbuilds as well as vessels in operation (in conjunction with a propeller shaft withdrawal). Design and in-service follow-up rules for the notations are included in DNV GL’s January 2018 rules for ships, Part 6, Chapter 2, Section 10, and Part 7, Chapter 1, Section 6 (38) respectively.
DNV GL observes keen interest from the industry in the new class notations and is currently engaged in many live projects.
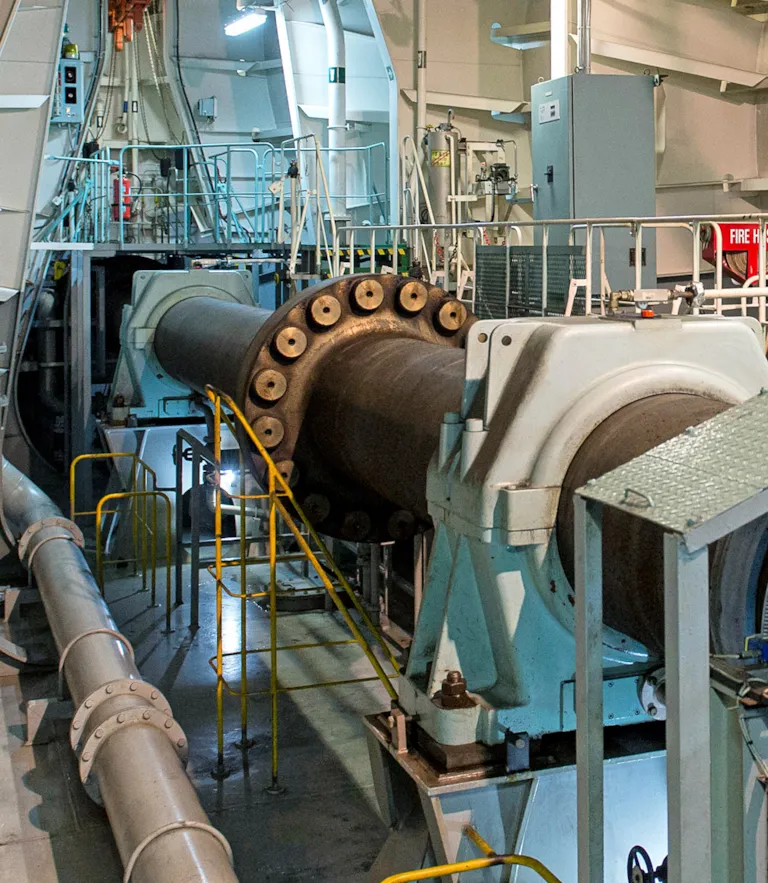
Reliability challenge
Oddvar Deinboll, head of the machinery approval section, DNV GL, explains: “The industry has faced challenges with some of the more recent single stern tube bearing installations with respect to the reliability of the propeller shaft bearings. Extreme turns in the upper speed range have been observed as one of the predominant scenarios in which many of the failures have been reported.”
Most of the reported damages have been observed on the aft-most part of the aft bearing and were accompanied by high bearing temperatures with an abrupt rate of rise. Expensive and time-consuming repairs were the consequences.
“We hope that ships complying with the revised main class rules for single bearing installations and Shaft Align(1) or (2) will have substantially reduced risk for stern tube bearing failure. Hence DNV GL will meet the industry needs for more reliable stern tube bearing installations,” Deinboll adds.
Monaco-based Scorpio Shipping, a frontrunner with DNV GL in many evolving trends in classification, is the first operator to opt for the Shaft align(1) notation. Dean Mihalic, Technical Director at Scorpio, notes: “We are looking forward to deriving early benefits from this DNV GL class notation by being the first to bring it to the market. Our immediate plan is to use it on an 82,000 dwt bulk carrier being built under DNV GL class.”
DNV GL is currently the only classification society requiring verification of the hydrodynamic lubrication of the aft bearing in continuous operation. Larger propellers with lower rpm in combination with hydrodynamic propeller loads make it challenging to maintain an effective shaft-to-bearing contact area and keep the aft bearing well lubricated, DNV GL’s internal research has shown. This realization has benefitted many applications and helped resolve issues in ships both in and out of class.
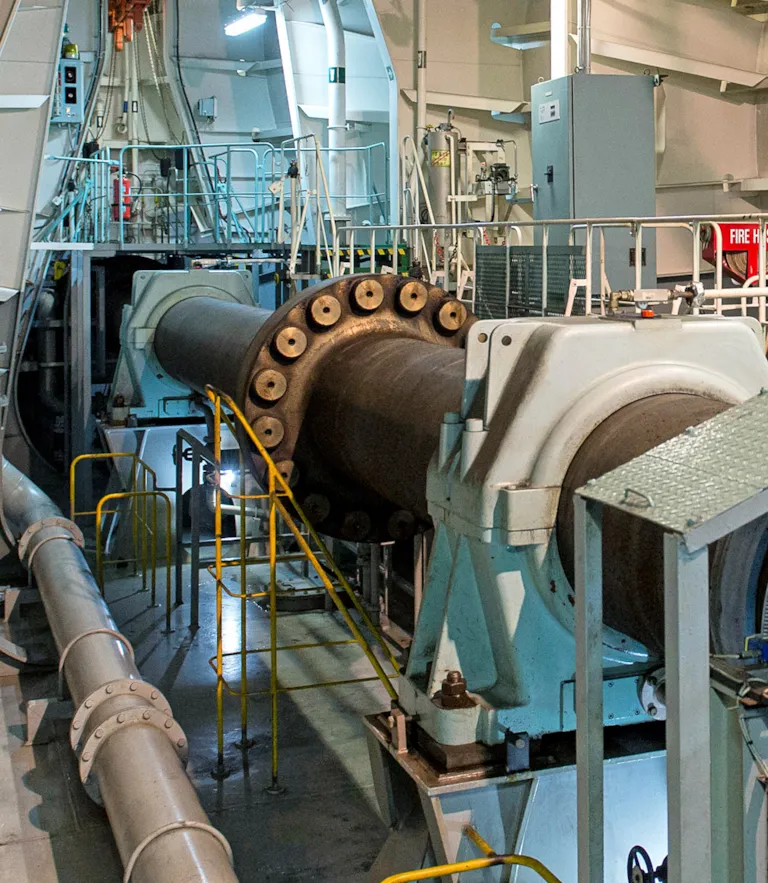
Extra focus
The new rules put additional focus on the impact of transient hydrodynamic propeller forces and moments on the aft-most propeller shaft bearing during turns, specifically at hard-over steering angles at maximum continuous rated (MCR) speed.
The Shaft Align class notations and revised requirements for single stern tube bearing installations call for a multi-sloped aft bearing design. This is supplemented by an additional evaluation of the aft bearing lubrication under an increased propeller-induced hydrodynamic downward bending moment on the aft bearing (corresponding to 30 per cent of MCR torque).
The requirements are formulated to improve bearing performance during turning conditions. The additional design and installation criteria will also increase operating margins and enhance bearing performance and lifetime under normal continuous running conditions.
Shaft align(1) is a cost-effective option for vessels with conventional hull forms, improving aft bearing performance in normal operation and in turns. Shaft align(2) is intended for propulsion systems requiring additional calculations to predict hydrodynamic propeller loads during extreme turning conditions, typically on vessels with unconventional hull forms such as asymmetric sterns or twin-skeg configurations.
The main benefits of the notations include prescriptive design criteria beyond generic class requirements; increased operating margins for continuous and transient (turning) operation; potentially more accurate installation by enhanced sighting methods (laser-aided or equivalent); and the owner’s benefit of having an additional notation in the vessel’s certificate.
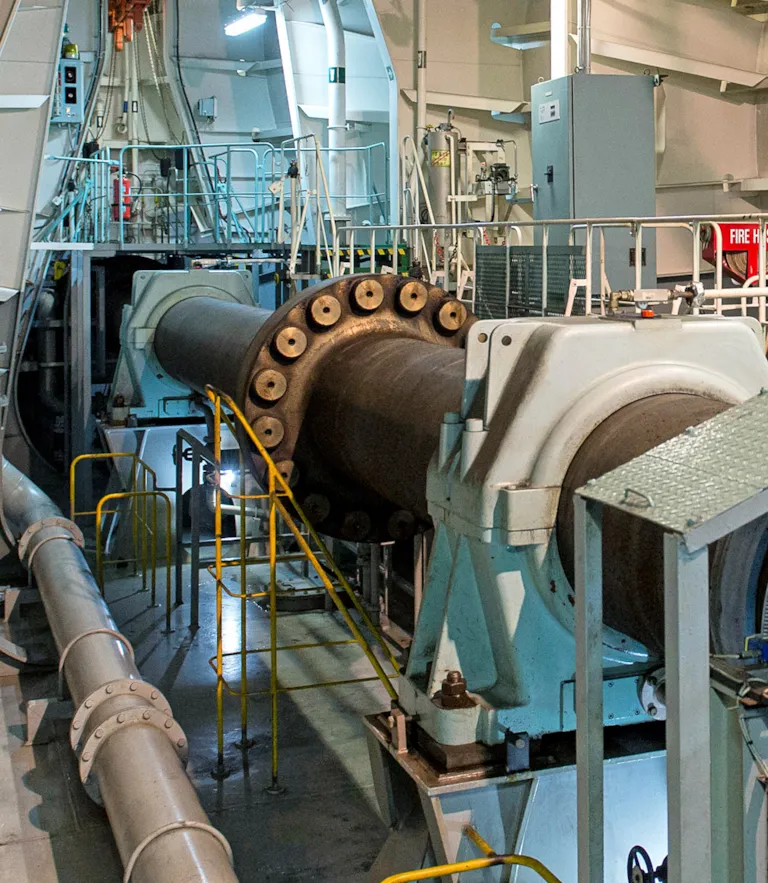
Bearing interaction
This shaft alignment philosophy aims to achieve an acceptable load distribution on shaft bearings while accounting for the hydrodynamic loads induced by the running propeller. The propeller weight as well as hydrodynamic forces and bending moments influence the angular misalignment of the shaft inside the aft bearing (relative slope) and, subsequently, the shaft-to-bearing contact area. The hydrodynamic lubrication – the formation of an adequate oil film – is mainly influenced by rpm, the shaft diameter, the oil viscosity, the net effective shaft-to-aft bearing contact area, and the bearing load and clearance.
The aft bearing design geometry must ensure a satisfactory shaft-to-bearing contact area in relevant operating conditions. This will also mitigate extreme localized loads (edge loading), the surface pressure on the aft bearing and associated thermal loads.
The most predominant hydrodynamic propeller loads are typically caused by continuous ahead operation under hydrodynamic lubrication conditions (typically a lifting bending moment induced by the propeller) or extreme transient manoeuvre (typically, hard over turning at MCR speeds with exaggerated hydrodynamic propeller loads acting downwards on a reduced area of the aft bearing).
Transient extreme turning conditions at the maximum speed can lead to mixed or boundary lubrication condition, which is not calculated under the main class criteria but is deemed satisfactory based on experience, provided that the installation complies with the applicable rule criteria for continuous running and incorporates the relevant range of bending moments.
A hot static starting condition, i.e. starting the prime mover to the minimum continuous propeller shaft speed, is also of interest with respect to hydrodynamic lubrication under the relevant rule criteria.
“A multi-sloped bearing design helps better optimize the shaft-to-bearing contact area in all operating conditions with regard to hydrodynamically induced propeller loads,” observes Arun Sethumadhavan, Senior Principal Engineer, fleet in service for hull, materials and machinery, DNV GL. In the case of a single-sloped bearing, improving the contact area for one operating condition may reduce the contact area in another operating condition.
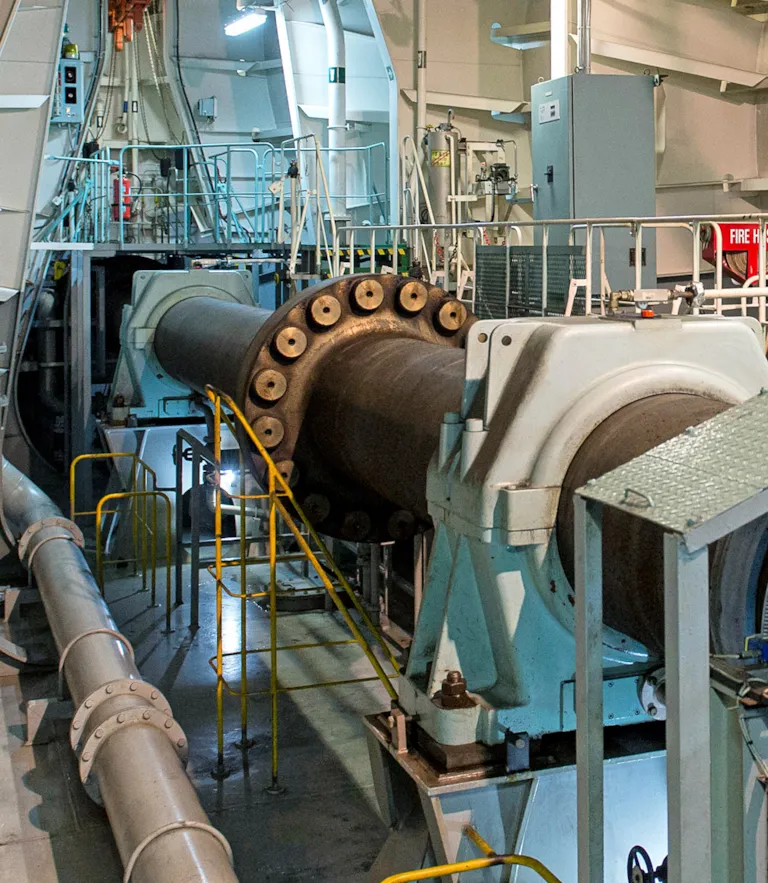
CFD calculations and finite element analysis – Shaft align(2)
On some installations, such as vessels with asymmetric sterns and twin skegs, propeller water inflow conditions during a turning manoeuvre may be altered beyond what is normally seen on more conventional designs. For such vessels there is a risk of excessive propeller loads and an empirical approach to stern tube bearing performance assessment may be insufficient. Rather, an additional evaluation of hydrodynamically induced bending moments and forces from the propeller on the aft stern tube bearing is mandatory for the Shaft align(2) class notation. Similar requirements may also apply upon evaluation under main class criteria.
Based on DNV GL’s experience, this evaluation is essential to ensure satisfactory shaft-and-bearing interaction during extreme turning conditions at maximum speed. Computational fluid dynamic (CFD) propeller load calculations combined with finite element analysis (FEA) of aft bearing contact pressure/area are best suited to support aft bearing evaluation and design.
CFD predicts the bending moments and forces induced by the propeller during continuous straight-forward operation and under hard-over MCR turning conditions as input to the aft bearing contact area and contact pressure estimation. A class guideline, CG-0283, will be published in 2018 to provide easy reference on the expected process and results in this regard.
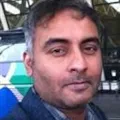
Arun Sethumadhavan
Senior Principal Engineer