Additive manufacturing makes spare parts easily available for yachts
Layer upon layer: 3D printing enables rapid production of individual parts with shapes that cannot be created by traditional manufacturing techniques. A new supply chain based on digital engineering data promises to make spares and bespoke objects available at lower cost and on short notice.
In mid-March 2020, in the heat of the coronavirus crisis, a hospital in Italy runs out of crucial valves that connect life-saving oxygen ventilators to patient respirators. The original manufacturer is unable to deliver the parts on short notice. In their despair the doctors turn to a local 3D printing firm, which reverse-engineers the part, tests a few prototypes, then makes 100 of them – all within 48 hours. Without certification, that is – saving human lives is all that counts in this case. Notwithstanding the haphazard circumstances, this incident is a compelling manifestation of the power of additive manufacturing (AM).
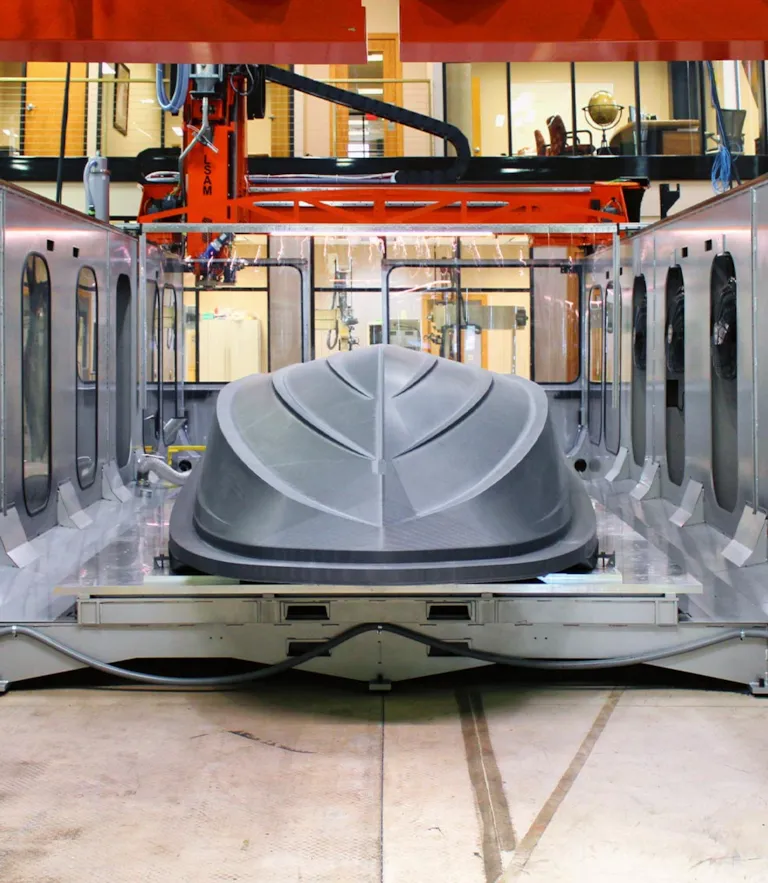
A wide range of potential applications
Saving lives may not be a typical concern when it comes to reaping the benefits of additive manufacturing in the yachting world, but safety certainly matters often enough. So plentiful are the possibilities offered by this young digital technology that it is probably fair to say AM is heralding a new era for this segment where every craft is unique and countless items on board are custom-designed. 3D printing seems like the perfect approach to manufacturing not only spare parts but original items for yachts as well.
AM has made enormous strides since its humble beginnings a few decades ago. Helped along by powerful computers capable of controlling extremely complex processes in real time, a wide range of materials can be 3D-printed today. Tried and tested in the aerospace industry, where stringent quality and safety considerations must be observed, the technology is mature and capable of solving many procurement issues in other industries as well.
Additive manufacturing is fast and an ideal approach to making individual objects that would otherwise be prohibitively expensive to manufacture. Simple, portable 3D printers are quite affordable today and can be used to produce or reproduce a wide variety of simple plastic parts, even on board a vessel. More sophisticated objects, including metal parts, require much more costly AM equipment and specialized manufacturing firms. But as the maritime sector becomes increasingly aware of the benefits of an on-demand supply chain for bespoke parts, a young industry catering to its specific needs is springing to life at major ports around the world.
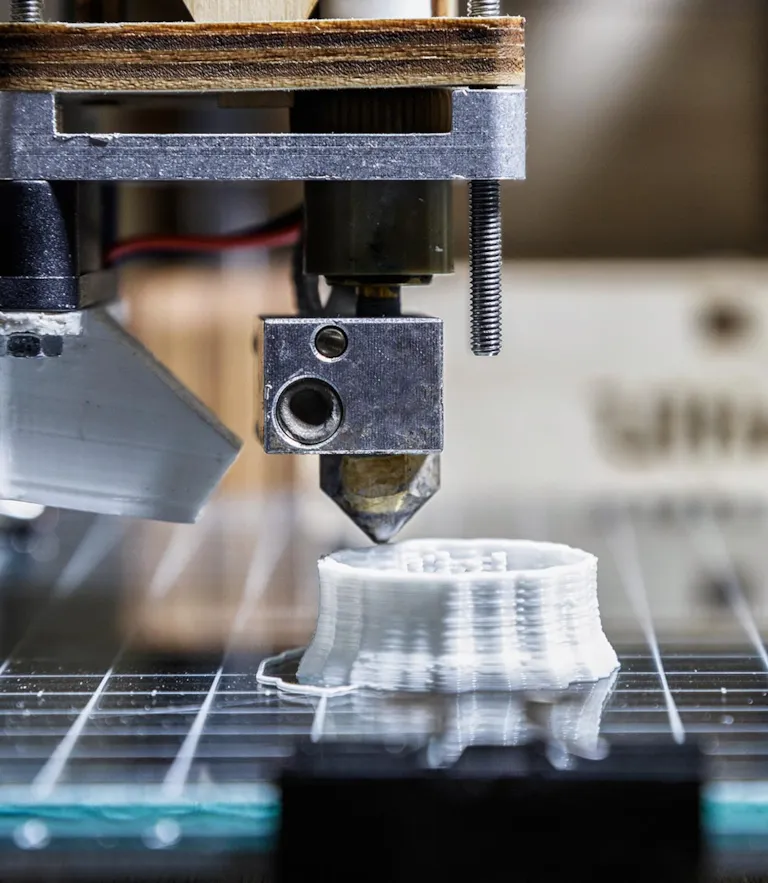
Overcoming engineering constraints in 3D printing
Apart from making parts available relatively quickly that would otherwise be difficult if not impossible to obtain, or expensive to make and ship, additive manufacturing offers a list of unique advantages over traditional technologies. By building up objects layer by layer, AM can produce entirely new shapes and complex geometries that traditional, subtractive methods are unable to achieve. For example, objects can be printed with an ultralight but strong honeycomb structure instead of being machined or forged from massive castings. The resulting object is much lighter than its conventional counterpart without sacrificing any of the physical performance characteristics, says Simon Ratcliffe, Team Lead, Additive Manufacturing X-Team at DNV GL: “With a honeycomb design you look at a huge piece of metal and think it’s going to be super heavy, but it is not because of the way it was 3D-printed.” This is of great interest to the racing world, where every gram saved translates to greater speed and agility. Lower weight can also improve the performance of engines and propellers while saving fuel.
Expensive materials, such as titanium, are used much more sparingly in an AM process because there is virtually no waste, and if for any reason a 3D-printed part fails to satisfy the quality expectations, it can simply be ground to powder and reused. The same applies to worn or damaged parts made of costly materials. Recycling the material in this manner is both economical and eco-friendly, especially if it occurs close to the customer.
What is more, 3D printing is a great approach to rapid prototyping. Before making a newly designed object from expensive material, a prototype can be printed using cheap plastic to test its shape and properties; there are even biodegradable printing materials available that avoid any kind of waste in the process.
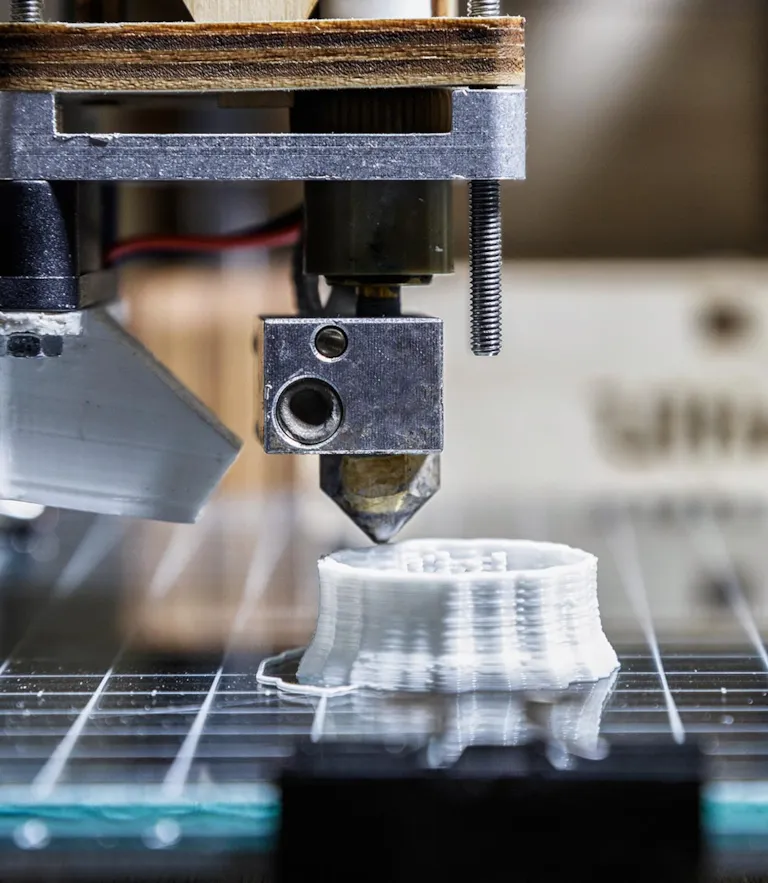
The challenge: Building a digital inventory
Producing 3D-printed spare parts locally at the place of use rather than having to order them from a faraway place not only saves time but also transport and warehousing costs, customs fees and taxes. In many cases the original manufacturer has discontinued production of an item and would have to retool an entire assembly line to make a small number of spares, causing disproportionate effort and costs. “There is increasingly a simple business case for moving from casting and forging to additive manufacturing,” says Ratcliffe.
When a part is obsolete and cannot be procured through conventional channels, additive manufacturing opens up a new approach to procuring replacements. If no original drawings exist, the part can be reverse-engineered, for example by scanning, and 3D-printed individually at a reasonable cost.
As long as the original manufacturer of an item is in business, it most likely owns the intellectual property rights in the part. Whenever additive manufacturing is more economically feasible than the traditional production method, there needs to be a contractual arrangement so the AM company can legally obtain the corresponding CAD files and the right to reproduce the item.
Moreover, if 3D-printed parts are to be widely available at major ports so the shipping sector can make extensive use of this novel supply chain, companies specializing in additive manufacturing must have access to large databases of printing files for common parts. Since printing files are typically created for specific materials and equipment, and manufacturers in different ports may use equipment and materials from different manufacturers, there needs to be a printing file for each specific combination of equipment and material. Building this digital inventory is a massive task for the ecosystem. The inventories are likely to be split and owned by multiple stakeholders, such as OEMs, printer companies, end users etc., depending on who owned the original IP and did the work to digitize a part for printing. DNV GL’s role is to provide assurance of these inventories. “We are building a registry of information for traceability and proof of fitness for purpose,” says Ratcliffe. “And we will scale that as needed.”
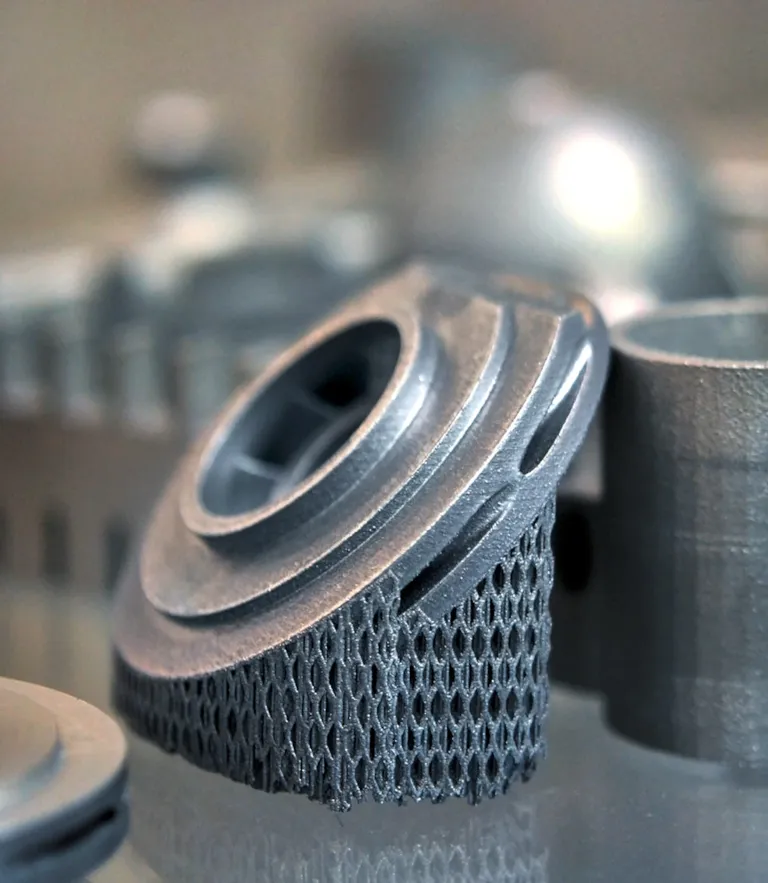
A rapidly evolving AM industry
In a groundbreaking project, the well-known ship management company Wilhelmsen Ship Management launched an exclusive early adopter programme with six Wilhelmsen customers to test the practicability and feasibility of a subscription concept: each customer pays a monthly fee for an unspecified number of 3D-printed plastic spare parts of a specific type deliverable on demand. During the ramp-up phase, these parts are made and delivered from the Singapore-based Wilhelmsen Ships Service facility. If successful, the Wilhelmsen global network will also offer spare parts-as-a-service in other ports such as Rotterdam. DNV GL’s Simon Ratcliffe says: “I believe we will see printing hubs in many places yachts frequent, instead of parts flying around on aircraft.”
It is only a matter of time until metal parts will be included in the list of items ship operators can order on demand at major ports. In fact, various manufacturers have incorporated AM into their standard processes. For example, Tahoe Boats and Thermwood have 3D -printed a metal pattern for the T16 boat hull in individual sections. The Spanish shipbuilder Navantia 3D-prints hatch grates because the conventional iron casting process is too costly. RAMLAB have begun making ship propellers in a fast AM process. As the technology evolves and the procurement infrastructure grows, yacht designers and builders will increasingly be able to order one-off parts, including interiors and furniture, from local 3D printing companies.
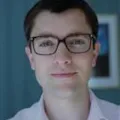
Simon Ratcliffe
Business Transformation Manager
- Thermwood Corporation
- MarinaGrigorivna – Shutterstock.com
- Sergi Lopez Roig – Shutterstock.com