A new dimension in manufacturing
3D printing, or additive manufacturing, has the potential to transform the maritime industry – radically disrupting existing business models and redefining the entire supply chain. DNV GL is ready to help the industry navigate the way ahead, seize the potential, and mitigate risk, on a journey into the future.
“Imagine you’re the captain of a vessel off the coast of Australia,” says Marit Norheim, Vice President, Material Specialist, Hull, Materials & Machinery at DNV GL – Maritime. “A system component has broken and must be replaced to continue sailing. Communication with the shipowner reveals that the piece is not kept in stock as a spare part and has to be manufactured by the European supplier before being shipped to you. Your vessel is looking at a downtime of weeks, perhaps even months.”
Norheim’s colleague Ramesh Babu Govindaraj, Principal Material Specialist, takes up the story: “But what if that component can be printed in your nearest port? The manufacturer sends the relevant CAM file to their local office, a partner organization, or possibly the port itself where it is promptly made using a 3D printer. The part is then attached to a drone which transports it to your vessel, simply dropping it onto the deck for the crew to install. The downtime, not to mention the costs of manufacturing and logistics, is minimal.”
“And,” he adds with an enthusiasm clearly inspired by the unique possibilities of this technology, “what if your vessel even had its own printer? One it could utilize to print spare parts on demand?”
There’s a slight pause in conversation for this scenario to sink in. “Don’t you think,” Norheim states, somewhat rhetorically, “this can be truly transformational for the maritime industry?”
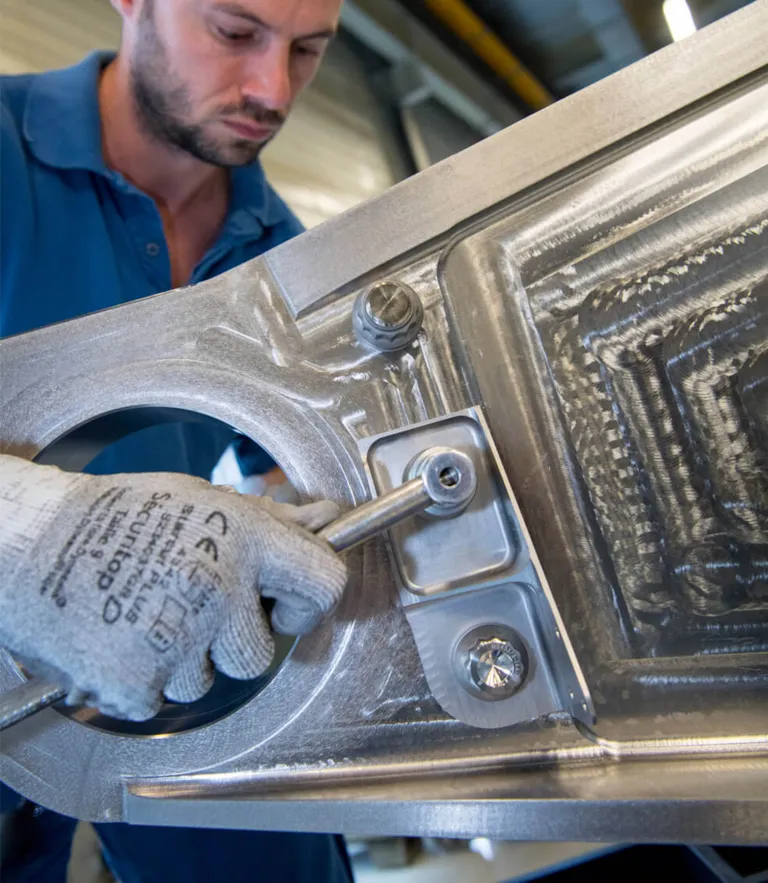
Layers of potential
It sounds like something from the realm of science fiction. But this is a near-future scenario, not an industry pipedream, as Norheim and Govindaraj, who have been studying the potential of additive manufacturing (AM) at DNV GL’s Høvik headquarters, are quick to stress.
AM is a type of 3D printing. Over the past few years additive manufacturing has hit the headlines revealing how machines applying layer upon layer of polymers can create objects of almost any shape and geometry guided by design files – even in the comfort of your own home.
What is more, a fascinating new development is now sending shockwaves of excitement through numerous industrial arenas, including the maritime industry: it is now possible to print in metals.
“Suddenly everyone is paying attention,” Norheim reveals. “The implications for stakeholders throughout the industry are enormous. If products and components can be printed as needed locally or even on board a ship, this is truly a disruptive innovation for the supply chain, translating into shorter lead times, lower costs, and a reduction of effort in labour, logistics and spare parts stock keeping.” AM can be used for maintenance and repair as well, simply by adding layers of material to worn components to avoid having to replace them. “This,” Norheim stresses, “could be a complete game changer.”
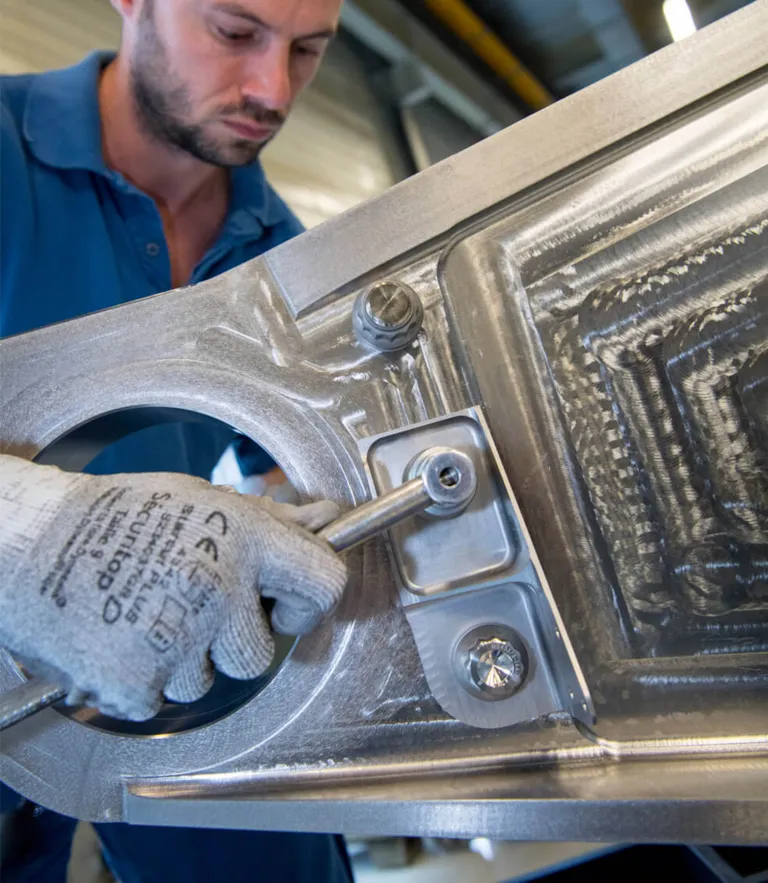
Global movement
Govindaraj remarks that the technology already had that effect for certain analogous industries such as aviation, where an Airbus A350 boasts more than 1,000 3D-printed parts. The maritime sector is following suit and, he says with conviction, the desire to embrace AM is abundantly clear.
“There are now 3D printers in many ports and industry hubs around the world,” he notes, “and this is just the start. Parts ranging in size from screw pins and bearing shells to box heat exchangers and even propellers have been printed successfully. As the technology, and our understanding of it, matures, the spectrum of printable components will increase. That is exciting, but it does come with challenges as well.”
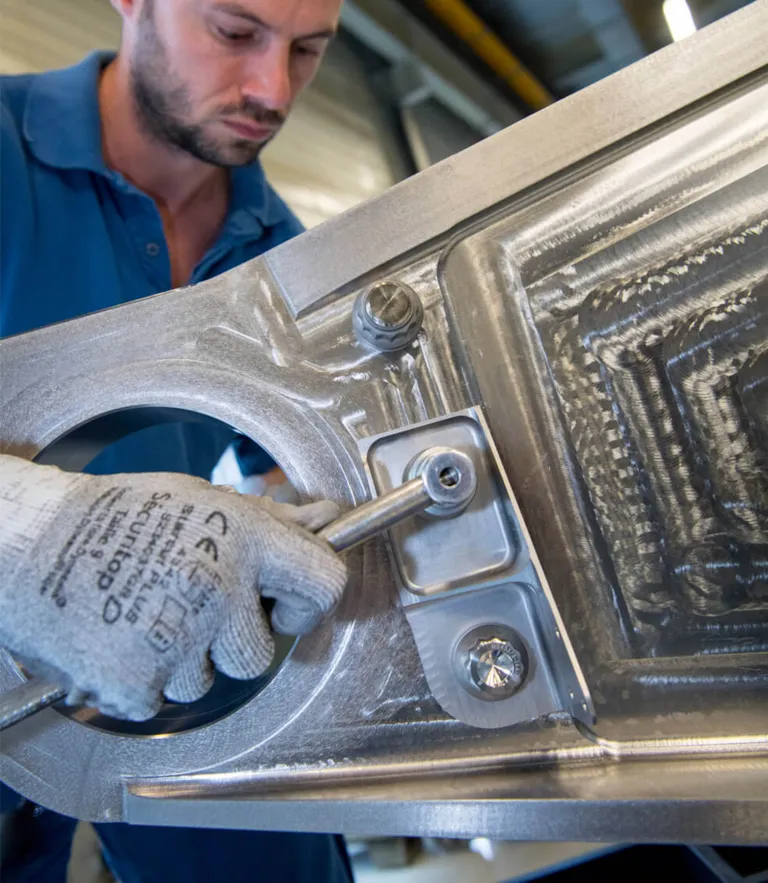
The need for legal protection
The challenges for the manufacturers and for multiple other players within the supply chain are obvious. If manufacturing shifts away from their factories to local sites and even ships or oil and gas platforms around the world, their current business model will feel the pressure. As for shipowners, while the potential to save costs and time is promising, the risks associated with AM parts and their quality assurance – which includes answering the question whether a given part is “fake” or not – surely increase.
Simply put: if it becomes this easy to print fakes, or reprint parts once you have obtained an original file, isn’t that the potential death knell for manufacturers already reeling from the loss of production? Every stakeholder, Norheim notes, is entitled to a legally protected environment to do business. “Manufacturers have to protect their intellectual property, and shipowners must safeguard the integrity of parts to ensure safe operation,” she points out. “Part of the solution lies in the software that is used.” Employing a technology like blockchain (see page 28) would allow those printing the parts to use a specific design only once – the same way consumers can digitally rent a film and play it once without actually owning it. This means the manufacturer still has a product to sell and the customer knows they are getting “the real deal”. “And then, of course, there’s the role of class,” Norheim emphasizes.
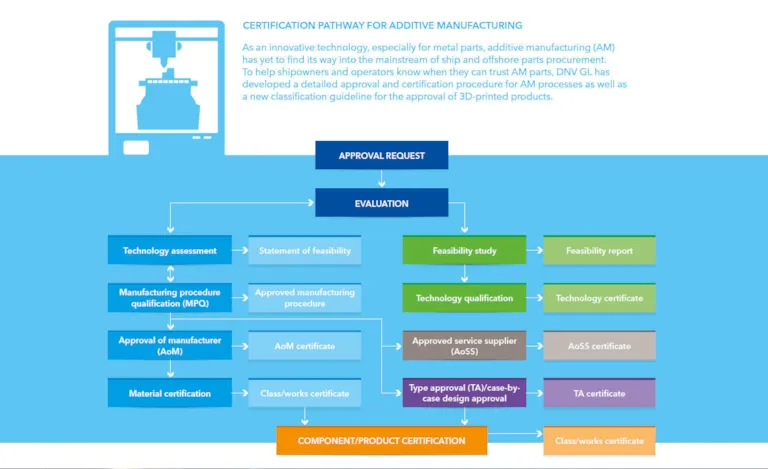
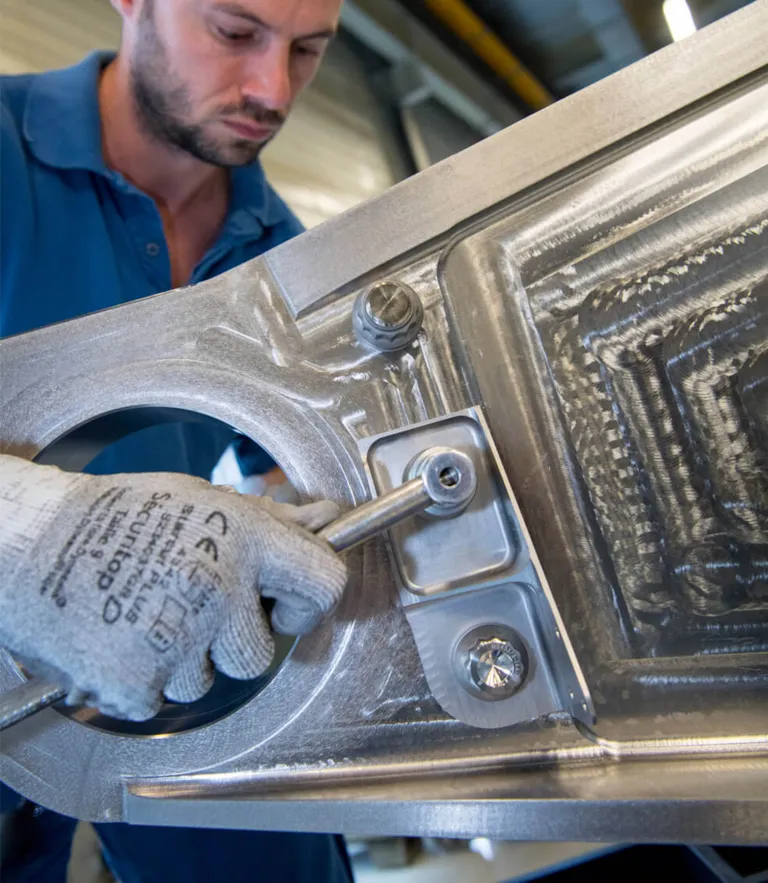
Building understanding
DNV GL has been looking into the potential of 3D printing for the maritime and oil and gas sectors since 2010. This has seen the organization releasing research and innovation papers, undertaking pilot studies and, more recently, an involvement in various JDPs, the latest of which involves a specialist team working alongside PJ Diesel Engineering, Kompressorenbau Bannewitz, Maersk Drilling, Thürmer Tools, and FORCE Technology to assess the repair and reconditioning of turbochargers with laser cladding 3D printing technology.
However, Norheim, Govindaraj and Sastry Yagnanna Kandukuri from DNV GL Oil & Gas have focused on a more over-arching remit – initially researching, then developing DNV GL’s first classification guideline for the approval of 3D-printed products. This guideline, which has been released recently, is a landmark achievement for DNV GL and their customers.
Building confidence
“DNV GL has a long history as an independent and trusted partner for the maritime and oil and gas sectors,” Norheim states. “So it is important that we take a lead role in supporting our global customers and helping them realize the potential of emerging key technologies.”
Govindaraj explains how it will be delivered, going step-by-step through the class guideline DNVGLCG-0197. “Basically we have to start at the very beginning,” he explains, “with a complete review of any requested 3D prototype model that is to be printed. We look at the design, functionality, materials – every parameter that will have an impact upon the final product. This is followed by a technology assessment, manufacturing procedure qualification, data transfer, then the actual printing and post processing. We are physically present for the printing of the prototype, and have a full understanding of the printer capability to ensure that it can be emulated anywhere around the world.”
He continues: “This is still a critical manufacturing process, regardless of the fact that it is not being undertaken in a traditional manufacturing environment, so we ourselves and our customers need to have complete confidence in it. The final step is a comprehensive evaluation and testing process, as we would undertake with any product. If we are satisfied with the results, we will issue the certificate. This may be a revolutionary concept, but our customers need the same level of assurance in these products as they would in any others. That is exactly what we aim to provide with our new guidelines.”
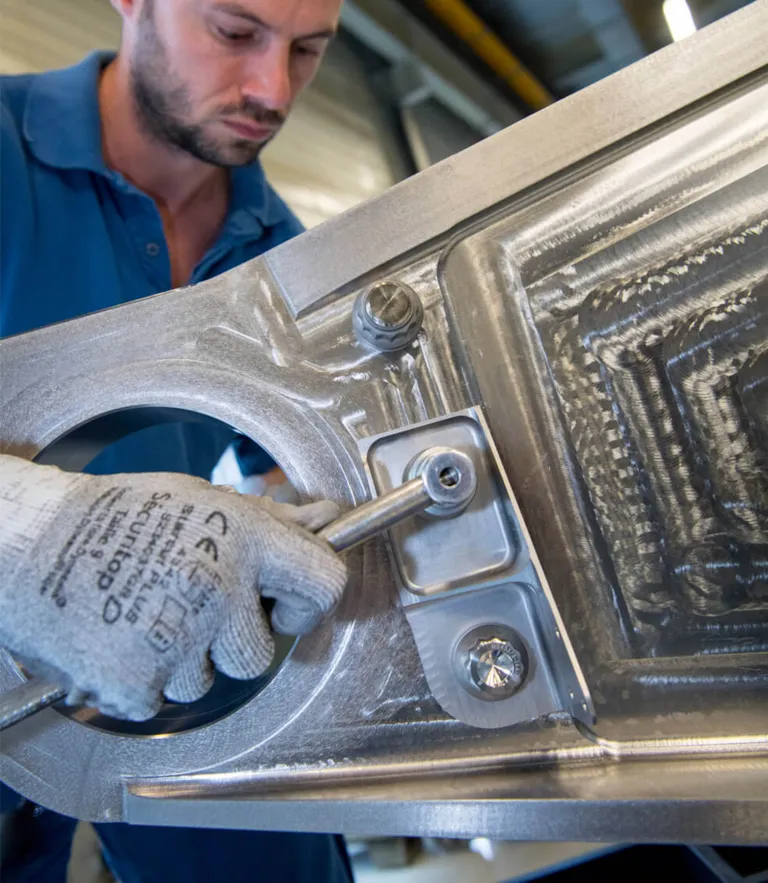
Here to help
Norheim concludes that 3D printing is “here to stay” and should be welcomed, noting: “It is an opportunity that should be embraced, rather than a challenge the industry should try and resist. The new classification guideline is here to help, assisting all stakeholders in the implementation of AM.”
Govindaraj agrees, adding: “We are ready to certify, and ready to support. This really is a new dimension, and we look forward to helping our customers discover its potential.”
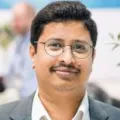
Ramesh Babu Govindaraj
Principal Specialist - Material, Welding & Additive Manufacturing