A fleet in a day: MMC unlocks new efficiencies in machinery maintenance and survey
DNV GL has launched its remote machinery planned maintenance survey system, Machinery Maintenance Connect (MMC), which will allow surveyors to survey the machinery of an entire fleet in a single day, saving time, money and disruption.
“Planned maintenance is the way forward for vessel owners,” says Rolf Petter Hancke, Surveyor and Principal Engineer at DNV GL, confidently. “And with Machinery Maintenance Connect (MMC), we have a service that both enables and enhances this trend. By using data from the vessels alongside a powerful learning algorithm, we can remotely perform the maintenance survey of a customer’s whole fleet in one process, both saving time and reducing the disruption of daily operations.”
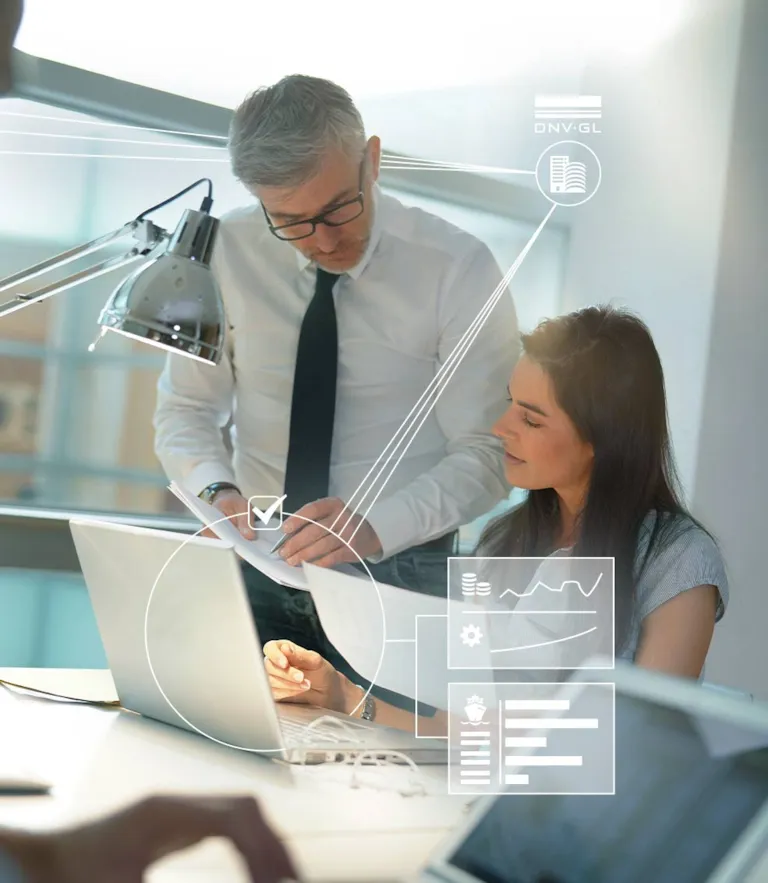
A class staple gets a digital makeover
In the past, machinery planned maintenance surveys used to be a tedious, time-consuming and disruptive procedure for the shipowner, crew and DNV GL. Surveyors had to travel to each vessel of a fleet, sit down with the chief engineer, and dig into the planned maintenance system (PMS) software on board to look for, gather and evaluate the relevant maintenance data.
Machinery Maintenance Connect (MMC) is DNV GL’s new approach to the machinery planned maintenance system (MPMS). Instead of requiring surveyors to travel to each individual vessel and go on board, machinery data can be processed via algorithms and presented to customers via digital dashboards, enabling the remote survey of both vessels only and the entire fleet and unlocking new insights into vessel and fleet performance.
“This is the first time we have completely digitalized a formerly analogue service,” says Hancke. “It was a huge team effort, both internally and in working with planned maintenance system (PMS) software providers, without which this wouldn’t have worked. But we are really proud to have created something that offers a service that is easily the equal of the on-board survey, if not better.”
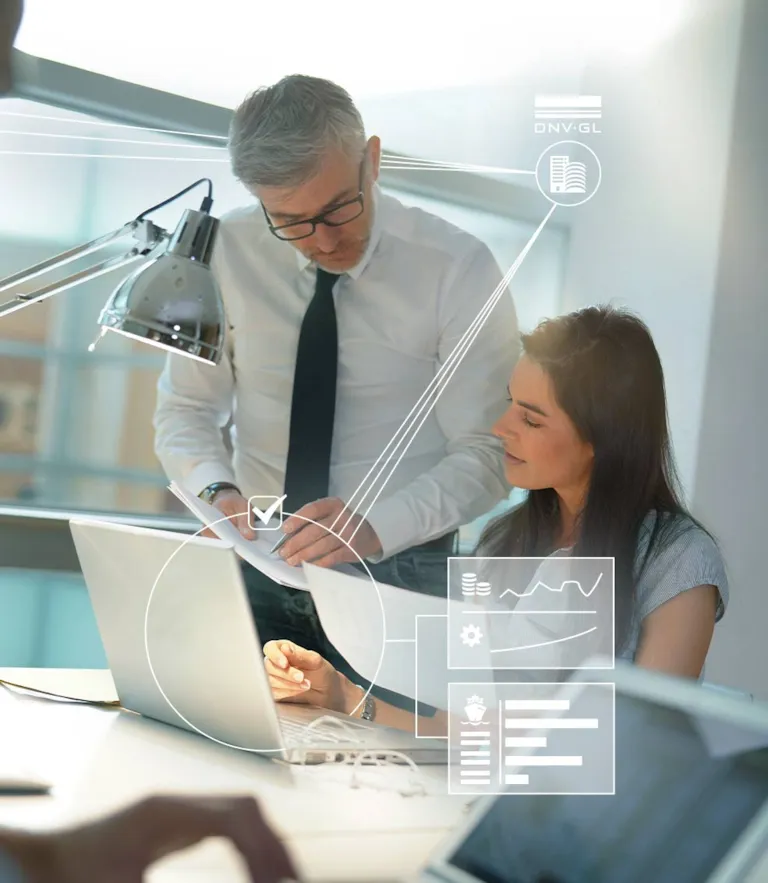
An idea for streamlined surveys becomes a solution
MPMS is essentially a data-based process, which made it an excellent candidate for digitalization, Hancke says. The development of the MMC solution began with some experiments during a conventional survey that ultimately prompted the customer to send him an Excel file with five years’ worth of maintenance history for four vessels. “I started to play around with the data and realized that this was exactly what we needed,” he recounts. “A colleague from Digital Solutions then created a dashboard to present the maintenance history in a new way, with infographics and bars. We showed the result to our customer. They were impressed, and the idea soon took off with other customers as well. Before we knew it, four more customers had sent us their maintenance histories.”
These experiments evolved into MMC, an online application accessed via the My Fleet portal, where vessel and fleet-specific maintenance data is collected and processed. The dashboard neatly arranges all the information, presenting a vessel overview of completed and outstanding maintenance tasks and an overview of the owner’s fleet-wide maintenance statistics including planned, completed and overdue work. This all helps to keep track of maintenance activities, providing the owner with essential insights for decision-making, and letting surveyors perform their inspections in a fraction of the time.
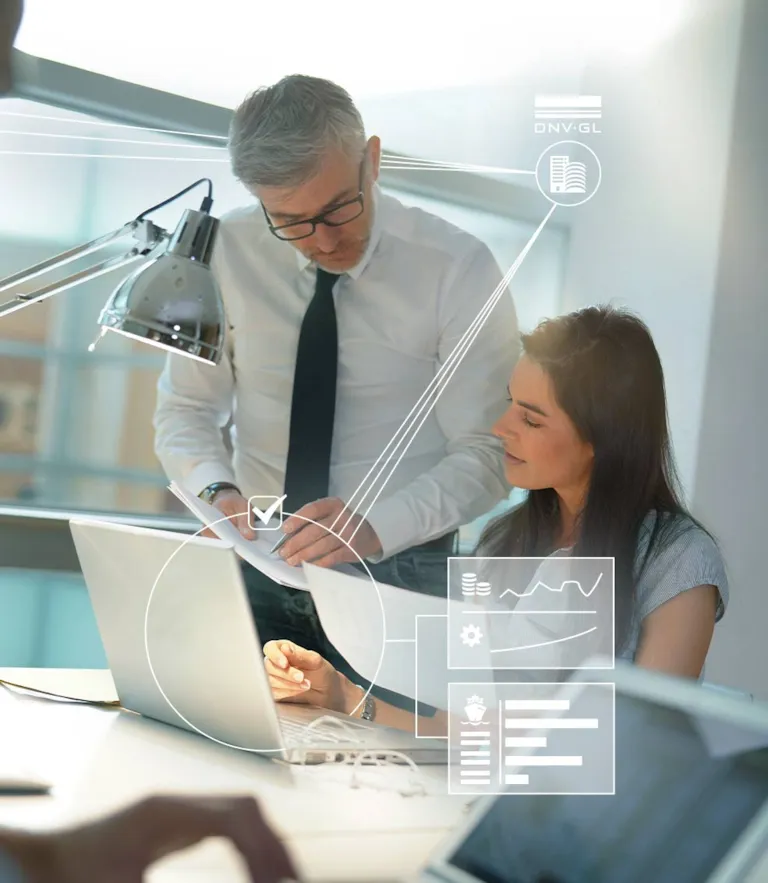
Collaboration with BW Offshore
“In 2018, we launched our corporate digitalization group to look at how we could apply some of the latest technologies to boost our operational efficiencies,” says Gabriel de Moraes, Technical & Maintenance Coordinator at BW Offshore. “We quickly perceived the great potential of MMC to carry out conventional class management tasks centrally and cover our entire fleet from our head office, with outstanding efficiency. The cooperation with DNV GL has been great, as it has been crystal clear that our goals are the same, to work together with efficiency and transparency in order to achieve reliable, efficient and safe operations.”
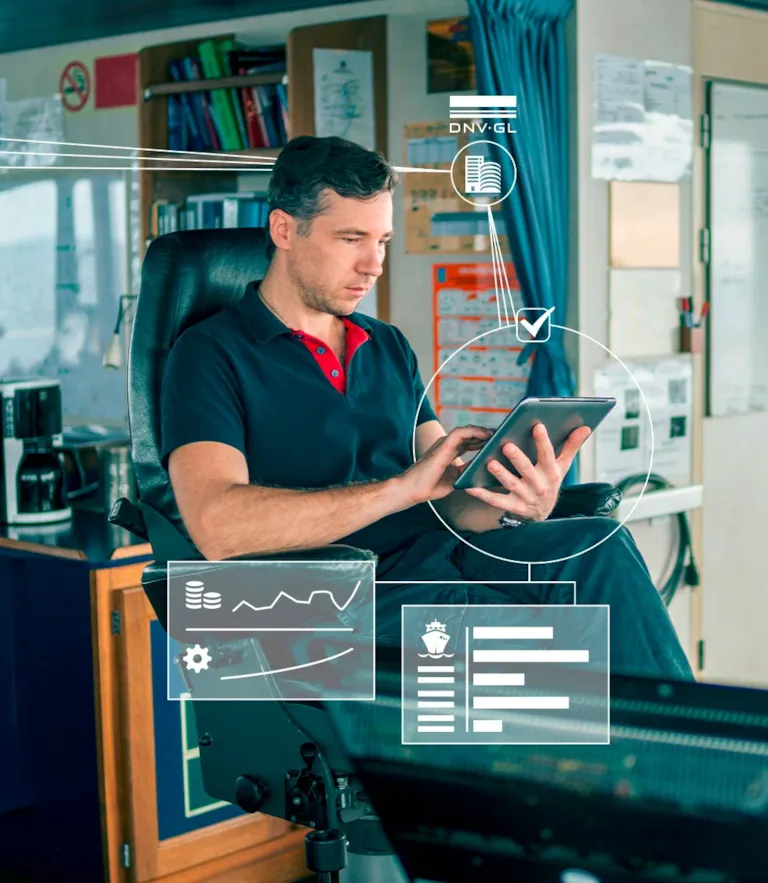
Getting started with digital machinery data
Each MMC dashboard can be customized to the needs of the individual shipowners and transmitting the maintenance data to the platform is easy for most ships, says Hancke. “We worked with the largest PMS software providers to integrate their software into MMC, so sending maintenance data to MMC from a vessel is as simple as plug and play,” he says.
Once the system is ready, maintenance data gathered subsequently can be automatically transmitted to DNV GL’s database via the Internet. Then by conducting surveys remotely, an annual fleet survey can be completed within a day without requiring costly surveyor visits. In addition, the annual MMC survey can replace traditional five-year inspections.
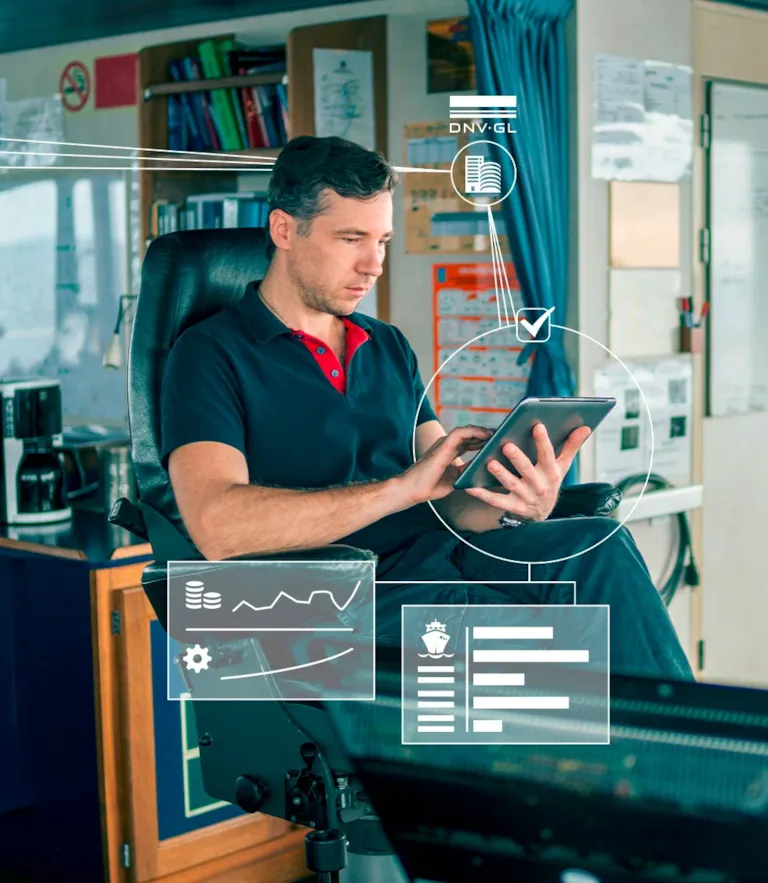
Efficiency gainings are substantial
For BW Offshore the advantages of performing surveys remotely were clear. “If we consider ten vessels of our fleet, which operate on five different continents, and account for all the logistics required to send a surveyor on board each one, adding also the man-hours from our staff to support the verification activities, and further impacts on regular operations in having to run extra tests on equipment for verification purposes even though we perform the same tests on a regular basis, the savings are substantial. Not to mention the environmental and safety impacts that can be avoided by executing these verification tasks remotely.”
For class as well, the time to perform surveys is radically reduced, explains Hancke: “Once we have the verified MPMS data, to get going with MMC we sit down with management for an initial company audit that also functions as their annual survey. This reduces the time required significantly. In one case we completed surveys on 49 vessels in roughly four hours, something that would normally take 49 separate on-board surveyor visits. And the data is all right there – instantly, easily and directly accessible by management in real time.”
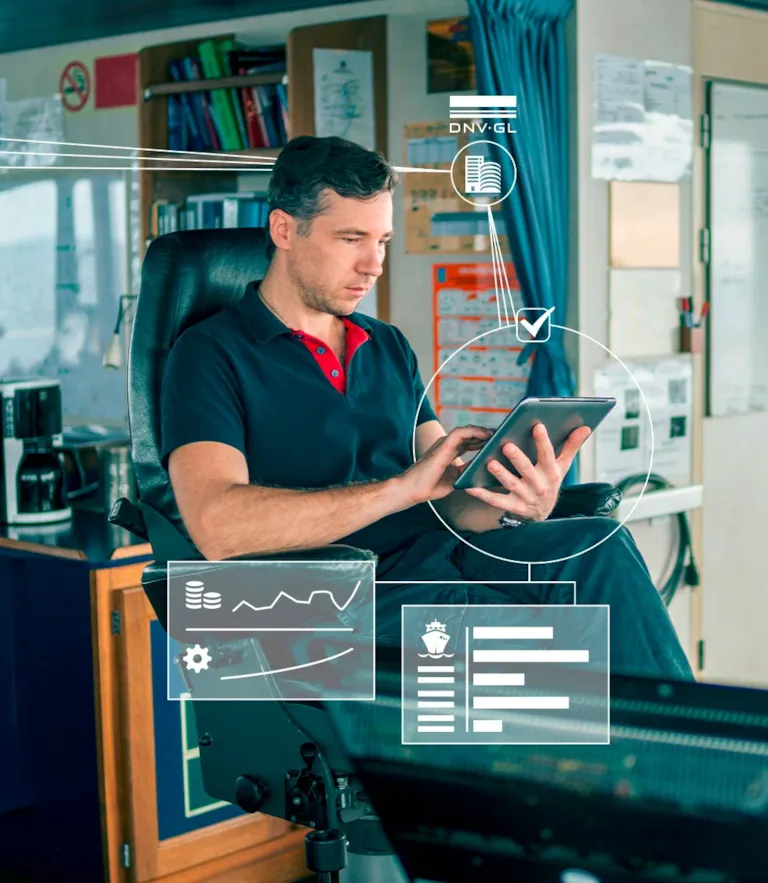
Consistency and transparency of data
In addition to streamlining the survey process, MMC adds consistency and transparency to maintenance and machinery data, emphasizes Hanke. “By working from the data directly, we cut down on variables. Every vessel is surveyed in the same manner, independent of the surveyor, chief engineer and PMS software. This provides a more objective survey and a stronger basis for comparisons and benchmarking.”
At BW Offshore, de Moraes noticed overall improvements as well: “After establishing the MMC with data streaming from our computerized maintenance management system (CMMS) to DNV GL, we found that our teams were more mindful about our maintenance routines. Furthermore, we appreciate the feedback that we have received from DNV GL as part of MMC. It contributed to further improvements to our maintenance activities.”
With additional data, BW Offshore is also looking to push ahead with their maintenance philosophy. “With support from the insights we gain by using MMC, we are able to revisit the effectiveness of all the work we do, which will allow us to develop more effective maintenance routines. Also worth to mention are a number of features of MMC that are of great help in easily identifying higher workload periods that can often create bottlenecks.”
By accessing the data analytics element of the system for decision support, the owner can create a maintenance plan to minimize disruption and predict the requirements of individual vessels, all of which helps to streamline operations and reduce costs and downtime. Then, by taking advantage of the AIS data integrated within the dashboard, the owner can choose the repair yard closest or best suited to the job required, dispatch engineers, and schedule an alternative ship to cover the downtime, all well ahead of time.
The classification society’s improved insight into the machinery maintenance status of each vessel is highly useful as well. “It enables us to give more informed recommendations for future improvements across the whole fleet,” says Hancke.
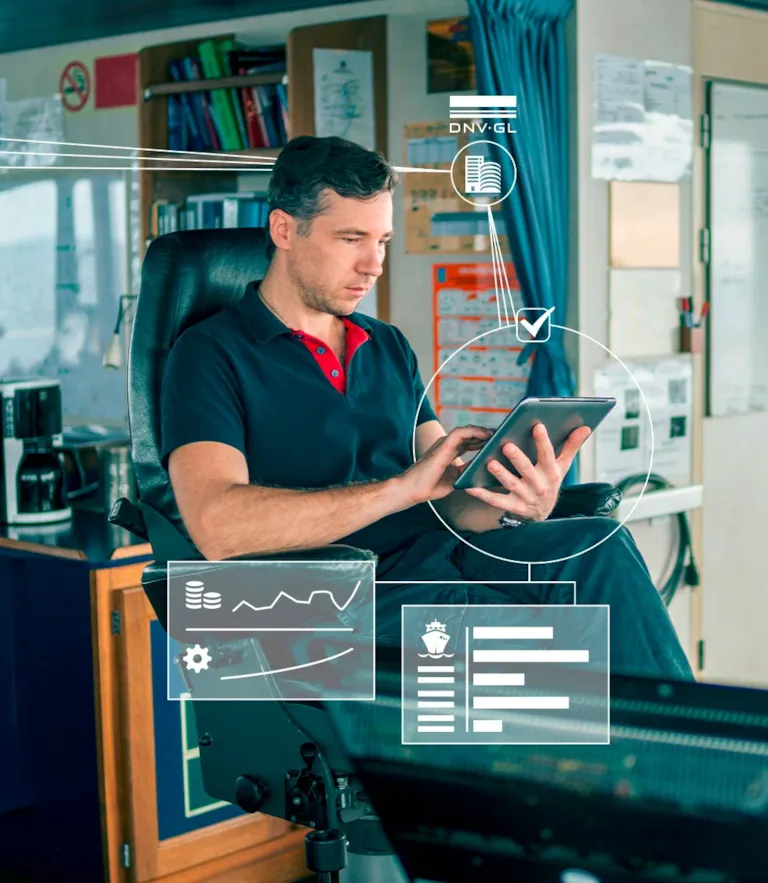
An evolving digital regime for survey and condition monitoring
As the digitalization of shipping continues, Gabriel de Moraes is enthusiastic about the possibilities. “We are very interested in using deeper MMC analytics, and to share the data on the maintenance and performance of various equipment and systems. As we progress on predictive maintenance, we will be able to develop models to better predict machinery performance and specific maintenance needs. Because at the end of the day we are not looking to do more maintenance, but smarter maintenance.”
DNV GL is also looking ahead, as MMC becomes more widely adopted and additional functionality is added.
“As we continue to add features to the tool, MMC will give owners even greater control and insight into the maintenance regimes of their vessels,” says Hancke. “Plus, with the roll-out bringing MMC to even more vessels within the fleet we will have access to more data and be able to help further reduce the number of unplanned maintenance issues. It’s another example of the benefits our customers are seeing from the process of digitalization that we have initiated at DNV GL. And it’s a journey that we are just beginning.”
DNV GL intends to continue on this journey by shifting towards digitalization in other surveys as well, such as the TMON, BMON and safety PMS surveys.
Rolf Petter Hancke
Global KAM & BDM
- Side image 2: goodluz - stock.adobe.com
- Side image 3: Igor Kardasov – Shutterstock.com
View image copyright information