3D-printed spare parts revolutionize maritime supply chain
It is an alluring proposition: imagine being able to procure urgently needed spare parts at any major seaport in the world within hours. The idea of using advanced 3D printing technology to make this vision a reality promises to be a game changer for shipping companies like Berge Bulk, which recently received the first shipment of 3D-printed parts.
In early February 2020 the bulk carrier Berge Mafadi was one of the world’s first ships to receive a commercial delivery of 3D-printed spare parts, including scupper plugs. Her owner, Berge Bulk, participates in a pioneering project that aims to establish a supply chain for 3D-printed items and answer several key questions relating to the feasibility of additive manufacturing (AM) as an alternative to traditional forms of procurement, similar to the aerospace industry, where AM has played a significant role for some time. Hakon Ellekjaer, Head of Venture — 3D Printing at Wilhelmsen Ships Service, which procured the spare parts for Berge Bulk, sees great potential in the technology. “The savings in terms of reduced cost, time and environmental footprint make 3D printing of maritime spare parts a tremendous opportunity for our customers.”
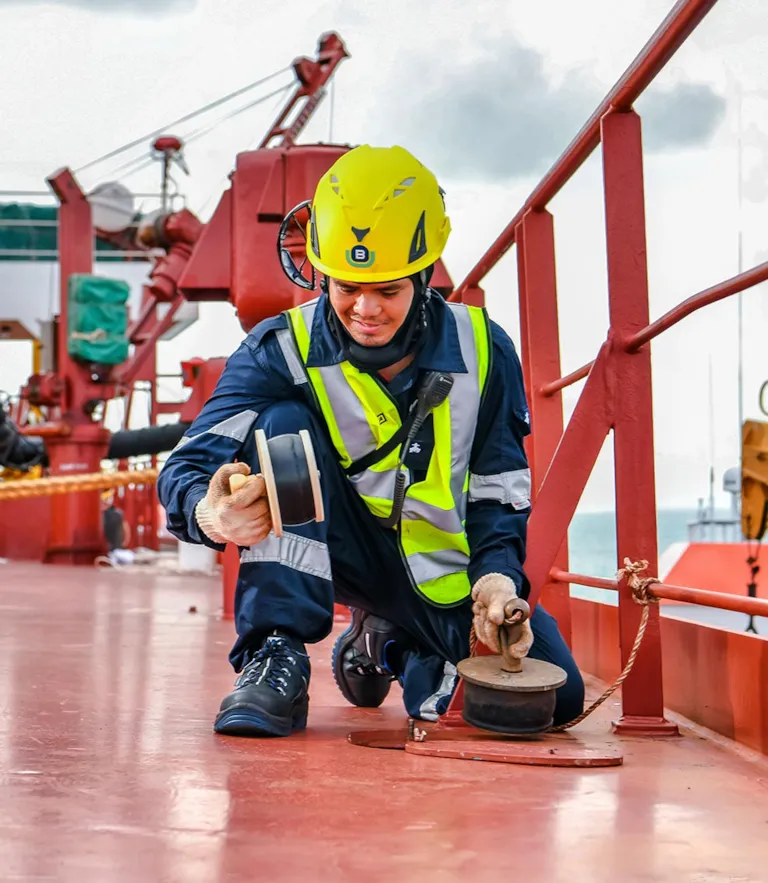
Singapore Centre of Excellence advances AM supply chain
Recognizing the disruptive potential of 3D printing technology, the Maritime and Port Authority of Singapore (MPA), the National Additive Manufacturing Innovation Cluster (NAMIC) and the Singapore Shipping Association (SSA), various industry partners and the University of Singapore launched a joint industry programme (JIP) in early 2019 to develop a concept for a future supply chain of AM spare parts. DNV GL was asked to lead the first phase of the project, which included a study into the feasibility of establishing a local additive manufacturing infrastructure able to supply a set of one hundred commonly ordered marine spare parts on demand.
Among the industry partners of the Singapore JIP is Wilhelmsen Ships Management. The Norway-based company owns a stake in its cooperation partner Ivaldi, a company specializing in on-demand 3D printing of spare parts for heavy industries. Ivaldi’s part replacement-as-a-service business model and 3D printing expertise were a perfect fit for Wilhelmsen’s global supply chain, and the two companies decided to make 3D-printed parts more widely available to the shipping community. The Singapore JIP provided an ideal platform to advance this concept.
In December 2019 the Marine Products division of Wilhelmsen launched an exclusive Early Adopter Programme (EAP) with six Wilhelmsen customers – Berge Bulk, Carnival Maritime, Thome Ship Management, OSM Maritime Group, Executive Ship Management and Wilhelmsen Ships Service – to begin utilizing on-demand additive manufacturing. Wilhelmsen and Berge Bulk had beta-tested the EAP concept for a year before the programme was rolled out. The role of DNV GL in this pilot project is to assure the parts-as-a-service ecosystem offered by Wilhelmsen and Ivaldi.
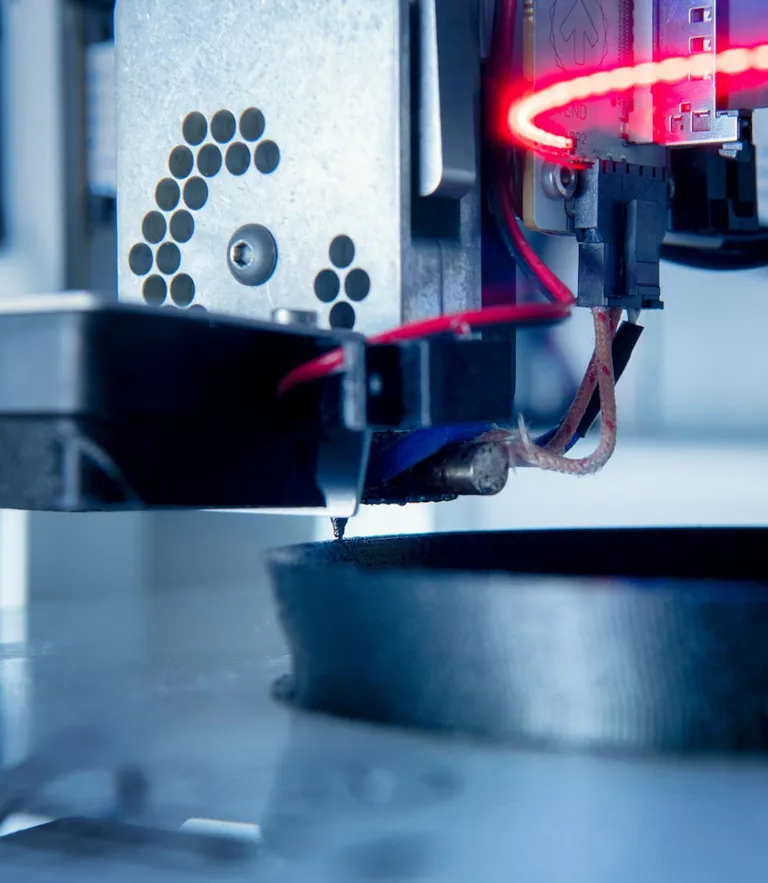
Establishing a digital inventory
Among the aspects that make additive manufacturing very attractive to the shipping industry is the ability to reproduce complex shapes out of many different materials using a variety of technical approaches, and to do so on demand. The key prerequisite, apart from the 3D printing equipment itself, is the availability of an electronic file for the desired part. But to be able to print parts fast, AM companies must have instant access to an entire library of printing files for common spare parts. Over the coming years more than 50,000 unique spare parts are expected to be digitized so they can be produced on demand, avoiding time-consuming and costly storage, shipping, customs and receiving processes.
Simon Ratcliffe, Team Lead, Additive Manufacturing X-Team at DNV GL, describes what this entails: “If you want to provide a distributed supply chain of spare parts on demand, you need a digital inventory. Developing such a library of 3D files takes effort. Then, to get the exact results you want at a different location that uses other equipment or material, you will need to redo some of your development work. This means that you end up with several files for the same part, which expands the size of the digital inventory significantly.”
Wilhelmsen, Ivaldi and DNV GL are testing a new universal part-tracking system to support quality control, part evolution and traceability. All relevant data and requirements related to the manufacture, design and performance requirements of each part are documented, and each part is assigned a unique identifying code. “We are building a registry of information for traceability and proof of fitness for purpose,” says Ratcliffe. “And we will scale that as needed
Wilhelmsen’s Hakon Ellekjaer comments on the benefits of this digital inventory: “Assurance is a vital part of our 3D printing service, both towards end users and OEMs. In order to ensure trust, every part, no matter how small, must be produced in a traceable and quality-controlled manner. With DNV GL’s help, every part we produce can be traced from the digital file through to part delivery. When we get feedback from the field, this enables us to go back all the way to the design and make whatever improvements are necessary. Wilhelmsen are therefore very proud to have teamed up with DNV GL to build a new service especially aimed at the assurance of digital inventories – accelerating the adoption of 3D printing in the maritime industry.”
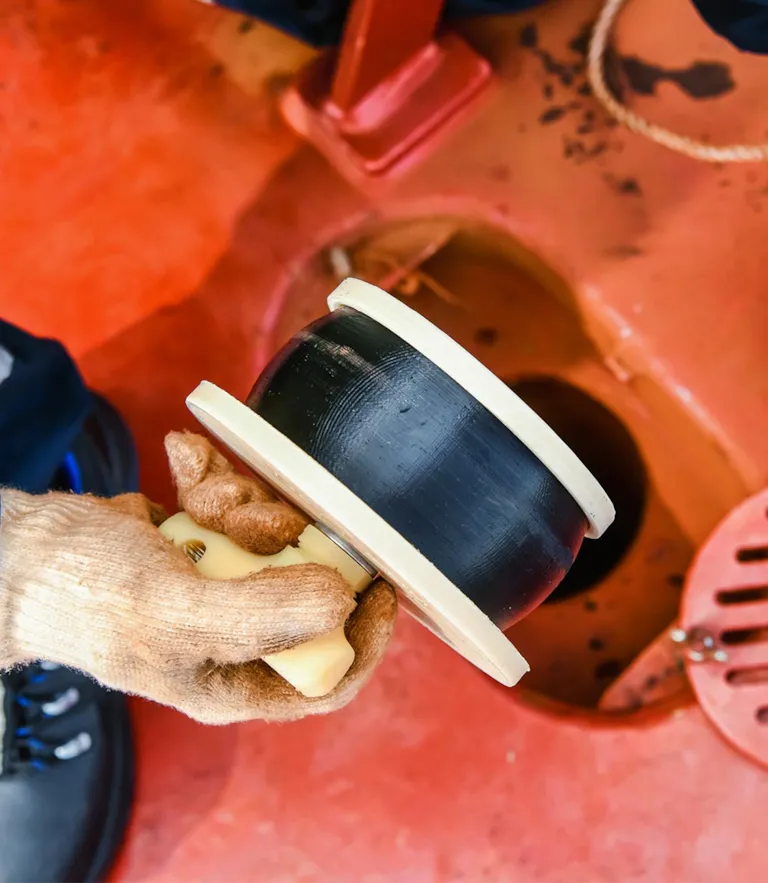
More critical AM parts will follow
The first list of 3D-printed parts available through Wilhelmsen’s subscription service may look unspectacular at first. But being able to procure these parts on demand at key ports – and at some point in the future at any major port in the world – makes a big difference for shipping companies, a fact highlighted by the growing number of companies asking to be included in the early adopter programme. Scupper plugs, which are used to close drainage holes to prevent oil or contaminant spills, are a good example to illustrate the many benefits of the new AM supply chain, as Sim Teck Siang, Procurement Manager at Berge Bulk, explains. “Scupper plugs are expensive, and there are no universal dimensions, which means that when there is a broken element, a new scupper plug needs to be brought. With additive manufacturing, the company is able to procure scupper plugs faster, cheaper and locally. If any part breaks, Berge Bulk can replace that one part instead of the whole unit. It is exciting to be part of Wilhelmsen’s Early Adopter Programme as on-demand additive manufacturing will revolutionize the spare parts industry.” He adds: “We are excited about the possibilities this will bring. Not only benefiting the supply chain but also the ability to modify and improve parts with input from end users’ experience.”
Captain Tarun K Gupta, Master of Berge Mafadi, explains: “It is very exciting for us at Berge Mafadi to try out new technology and the possibilities it will bring. Spare parts are currently a pain point, and we have trouble with for instance scupper plugs as they are easily stolen for their brass components. They are expensive, and we are constantly needing to replace them. By replacing them with plastic, we are eliminating any possibility of theft, and best of all, we get them on-demand within a short period of time. We are looking forward to experiencing the expanding offering from Wilhelmsen Ships Service.”
More complex parts and components will doubtlessly follow eventually. Even in those cases where the price of a 3D-printed spare part is higher than that of an original part because of higher material costs, the overall costs are likely to be lower, and the added benefits of rapid availability and eco-friendliness remain. From the manufacturer’s perspective, sending a file for an appropriate fee rather than shipping a finished part eliminates the disproportionate time and effort of retooling a manufacturing line just to make a single spare part.
The Wilhelmsen programme, while still in its trial phase, is definitely demonstrating the benefits of the concept and has attracted plenty of interest from shipping companies. Wilhelmsen’s Hakon Ellekjaer is confident: “We believe on-demand manufacturing technologies are going to completely reshape the maritime supply chain.” It is the responsibility of DNV GL to build trust in AM by providing assurance and certification, know-how and advisory services to help the individual players in the ecosystem collaborate with a constant eye on quality. “We believe that the safe and controlled use of AM will contribute to our purpose of safeguarding life, property and the environment,” Simon Ratcliffe points out. “It will do so in small ways, such as reducing the carbon footprint of the spare parts supply chain, or beating counterfeit products on the grey market. AM will be much safer if end users are able to get the right, reliable parts easily. That’s why we believe in AM and want it to be adopted by our core industries.”
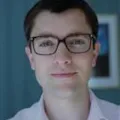
Simon Ratcliffe
Business Transformation Manager