New model helps engineers predict wind turbine standstill vibration in extreme conditions
A new model developed by DNV significantly improves predictability around how wind turbines behave during extreme weather, reducing uncertainty and risk for modern flexible turbines.
In extreme conditions such as storms, strong wind gusts or tornados, wind turbines need to shut down for safety reasons. Under such conditions, the wind turbine is positioned in standstill by pitching the blades, and the rotor rotation is slow or stopped. Wind turbines must withstand large load levels in these conditions.
The trend of increasing wind turbine size in the last few decades has raised concerns regarding the established numerical modeling approaches. The blades are becoming longer, slender and more flexible, resulting in larger blade deformations which may challenge the assumptions of aeroelastic simulation tools. Uncertainty is particularly high in standstill cases where the blade sections reach post-stall conditions. This raises the question: will my engineering tool be able to accurately predict the standstill turbine loading and response?
Learn more about Bladed - the leading wind turbine design software
Aerodynamic damping and dynamic stall
Wind turbines operating in standstill conditions can be exposed to extreme variations of the angles of attack at the wind turbine blade sections. As a consequence, large variation in loads can be triggered, leading to large blade deformations which can challenge the turbine structural integrity. In such scenarios, the aerodynamic damping plays a major role in the aeroelastic stability of the blades [1].
One of the most important aerodynamic models in predicting dynamic loads in wind turbine blades is dynamic stall. This modeling approach enables an estimation of the dynamic response of the airfoil forces at the blade sections in response to the environmental conditions. Dynamic stall effects introduce hysteresis on the aerodynamic forces in terms of the lift, drag and pitching moment as illustrated in Figure 1.
Many wind turbine codes use Beddoes-Leishman [2,3] or Øye [4] models to incorporate dynamic stall effects. While these models work relatively well for small to moderate angles of attack, they suffer from post-stall prediction inaccuracies, and can lead to an incorrect hysteresis of the aerodynamic forces, and poor prediction of aerodynamic damping. If aerodynamic damping is underestimated, many simulations show instability that is not so widely observed in the field. To compensate for the inaccurate damping predictions, engineers commonly alter the simulation settings by artificially increasing structural damping (usually edgewise or torsional damping) according to their experience. However, it is not clear what is an appropriate level of artificial damping to add.
Read also: Cowi uses combined power of Bladed and Sesam
The IAG dynamic stall model in Bladed
DNV has developed and implemented a dynamic stall model in the Bladed code that is designed specifically for deep stall conditions. The model was based on the Beddoes-Leishman model but has adopted several important improvements from the IAG model [5] resulting in a second generation IAG model [6].
In contrast to the classical Beddoes-Leishman model or Øye model, the IAG dynamic stall model has been developed and validated against measurement data of real wind turbine airfoil geometries operating in post-stall conditions, making it a more appropriate model to be used for wind turbines in standstill and extreme scenarios. The prediction ability of the IAG dynamic stall model against measurement data is demonstrated in Figure 2, for a pitching S814 airfoil with 24% thickness. The IAG model is able to predict the hysteresis effects of the aerodynamic forces better than other models. The overshoots of the lift, drag and pitching moment coefficients predicted by the IAG dynamic stall model agree well with the experimental data. This implies that the aerodynamic damping of a wind turbine blade in deep stall will be better predicted by the IAG model in real operation.
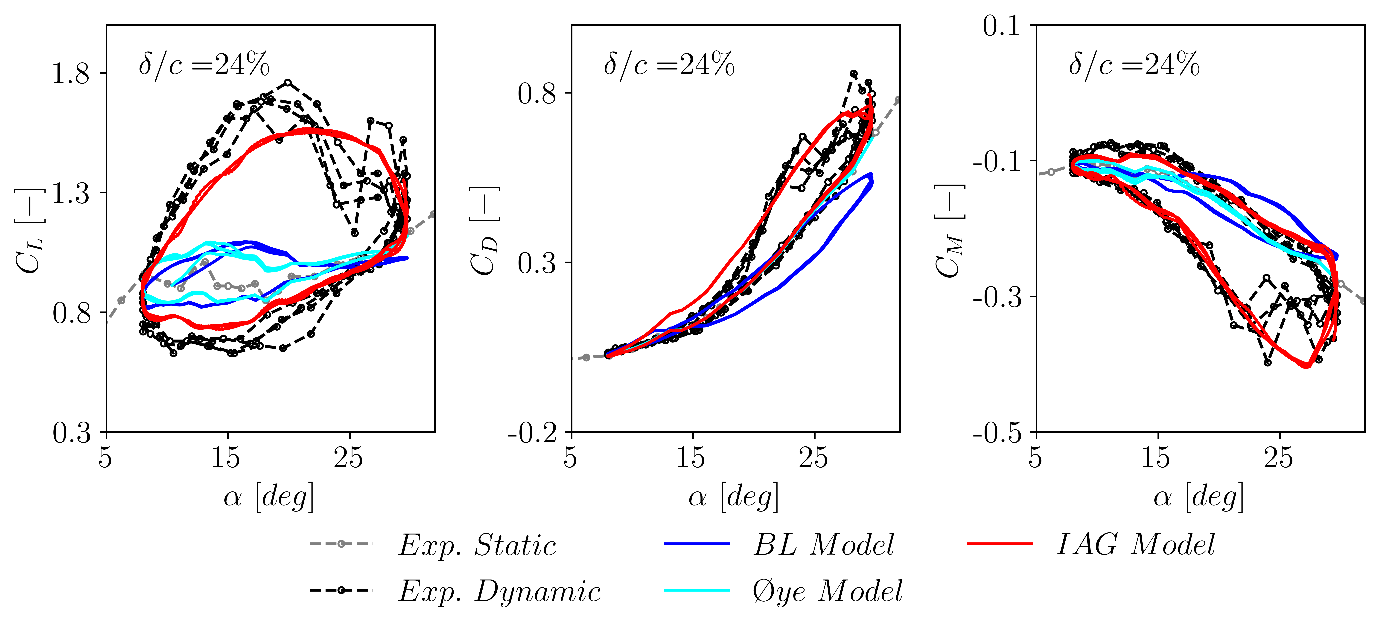
Figure 2. Comparison of three different dynamic stall models against experimental data of a pitching wind turbine airfoil in deep stall conditions. α = angle of attack, δ/c = thickness to chord ratio, CL = lift coefficient, CD = drag coefficient, CM = pitching moment coefficient about a quarter chord location.
How dynamic stall affects standstill wind turbine loads
The unsteady aerodynamic effects predicted by the dynamic stall models directly affect the aeroelastic characteristics of wind turbines in standstill operations [1]. The blade loads and deformations can become very large, causing high loading on the entire structure.
Figure 3 presents results from Bladed for an idling simulation of a large wind turbine at 40 m/s wind speed and yaw misalignment of +20 deg. It is seen that the dynamic response of the blade is strongly dependent on the dynamic stall model being applied. The Beddoes-Leishman and Øye models yield extremely large loads at the blade root and a tip torsional deformation above 20 degrees due to inaccurate aerodynamic damping estimation. Conversely, the IAG dynamic stall model predicts higher aerodynamic damping and yields a lower load level.
The grey line shows the traditional approach engineers take of artificially increasing structural damping, which gives a similar result to the IAG model.
Try the IAG dynamic stall model in Bladed
The latest versions of wind turbine design software Bladed incorporate the IAG dynamic stall model as an option for unsteady aerodynamic modeling. The use of the IAG dynamic stall model is recommended in standstill operations due to its improved prediction accuracy in deep stall compared to other widely used dynamic stall models. The addition of the IAG dynamic stall model in Bladed serves as a step forward to progress in wind turbine prediction technology, reducing uncertainty and risk in modeling modern flexible turbines.
Learn more about Bladed – the leading wind turbine design software
Author: Galih Bangga, Senior Turbine Engineer, DNV
References
- Wind Turbine Aerodynamics Modeling Using CFD Approaches; AIP Publishing LLC, 2022. https://doi.org/10.1063/9780735424111
- A Semi-Empirical model for dynamic stall. Journal of the American Helicopter society 1989, 34, 3-17. https://doi.org/10.4050/JAHS.34.3.3
- A Beddoes-Leishman type dynamic stall model in state-space and indicial formulations. Technical report, Riso-R-1354, Riso National Laboratory, Denmark, 2004. https://orbit.dtu.dk/en/publications/a-beddoes-leishman-type-dynamic-stall-model-in-state-space-and-in
- Dynamic stall simulated as time lag of separation. In Proceedings of the Proceedings of the 4th IEA Symposium on the Aerodynamics of Wind Turbines. Rome, Italy, 1991.
- An improved second-order dynamic stall model for wind turbine airfoils. Wind Energy Science 2020, 5, 1037– https://doi.org/10.5194/wes-5-1037-2020
- Development and Validation of the IAG Dynamic Stall Model in State-Space Representation for Wind Turbine Airfoils. Energies 2023, 16(10), p.3994. https://doi.org/10.3390/en16103994