Hydrogen quantitative risk assessment
One of the more holistic solutions to tackle hydrogen safety concerns is to undertake a quantitative risk qssessment (QRA) study. There are regulations, standards, guidelines and a strong industry practice from e.g. the downstream industry for the performance of QRAs. The QRA methodology captures the hydrogen facility and pipeline scope definition, hazard identification, failure cases, leak frequencies, event development, ignition probabilities, consequence models, impact models, and risk summation. Furthermore, a QRA is crucial in assessing separation distances, whether risk targets are met, if sensitivities and uncertainties are incorporated, and whether risk-reduction measures can be reasonably justified.
QRA, risks, and major accident hazards are all related to Seveso. In the EU, the Seveso III (Directive 2012/18/EU) aims to control major accident hazards involving dangerous substances by regulating the quantity of the substance stored in one place. The Seveso directive was implemented in EU member states for the first time in 1982 and has been updated continuously over the years.
For hydrogen, the limits for the lower and upper Seveso tier are 5 and 50 tonnes respectively, and the safety report (QRA) is first needed when one passes the upper tier. In practical terms, Seveso denotes less risk to Seveso below 50 tonnes of hydrogen, and thus even less so when below 5 tonnes of hydrogen. However, the issue with hydrogen is that volume, and not mass, drives the risk.
Introduction to modelling tools and validation
At DNV, we are often asked the question whether our consequence and risk modelling tools, Phast, Safeti, KFX and Exsim can aid in the identification and mitigation of hydrogen risks and, more specifically, in the prediction of hydrogen behaviour. The short answer is yes. Coupling these modelling tools and solutions with rigorous testing and validation is crucial to ensure their accuracy and effectiveness. At DNV, we prioritize and emphasize the validation and verification of our models against experimental data and actively take part in hydrogen Joint Industry Projects (JIPs). An internal DNV guideline is developed specifically for hydrogen QRAs, ensuring the QRA services are performed according to state-of-art practices and are consistent across different DNV offices. When scaling up hydrogen plants with increasing complexity, it is essential to have QRA models where geometry effects are included for dispersion and explosion risk, which necessitates the use of Computational Fluid Dynamics (CFD) models. This way, the industry can get to inherent safe designs during the first critical projects. The combined use of experiments and validated models can make the needed roll-out of large-scale hydrogen facility go faster.
Hydrogen QRA specifics
While the capability to simulate hydrogen releases in Phast and Safeti, and KFX/Exsim has been around for years, the complexities that hydrogen simulations present are constantly evolving. New areas of uncertainty emerge while ongoing research keeps best practices dynamic. Unlike more conventional fuels, hydrogen’s properties pose specific safety challenges stressing the importance of implementing comprehensive risk management strategies. Subsequently, some of the more prominent issues for hydrogen QRAs are covered.
Frequency rates
A well-established failure frequency database specific for hydrogen applications is something that the industry is still struggling with. A derivative comprising of commonly used frequency databases and hydrogen incident data adjustments in the form an exceedance curve that also accounts for uncertainties (error factors) is one of the solutions to overcome this hurdle. The internal DNV QRA guideline documents the approach. It is also clear that hydrogen equipment will be designed differently (more demanding) compared to the conventional hydrocarbon (oil and gas) equipment, thereby assuming a reduction of uncontrolled releases. This assumption is balanced by the fact that hydrogen has the smallest of all molecules, meaning hydrogen gas is more challenging to contain. There are also additional safety challenges related to storage of liquid hydrogen (LH2) at high pressures and cryogenic temperatures.
Failure modes
Equipment that is associated with hydrogen production or storage can have significantly different failure modes compared to conventional oil and gas installations. One of the more relevant examples is the hydrogen electrolyser, where risk of internal explosion caused by damage to the membrane/diaphragm may lead to the mixing of H2 and O2. The likelihood of this scenario needs to be carefully assessed and it is considered to be highly linked to design. QRAs should as a minimum analyse these as a potential scenario for electrolysers and whether this event is considered in the quantitative modelling. By focusing on root causes and preventive measures, a fault tree analysis (FTA) can be integrated with a QRA in which scenario development can be followed and tailored to likelihoods/frequencies developed to represent some of these more hydrogen topical scenarios.
Ignition probabilities
Hydrogen has wide flammability limits (4-75% in air) and very low energy required for ignition compared to hydrocarbon fuels. The probability of ignition depends on the causes of the release and the number and strength of ignition sources that the cloud covers before it disperses below its flammable concentration. Immediate and delayed ignitions are typically distinguished in QRAs because immediate ignition is assumed to produce a jet fire while only delayed ignition has the potential for an explosion. These assumptions may be inapplicable for hydrogen since an early ignition of hydrogen may produce an explosion, and explosions may be followed by jet fires. Therefore, ignition models need to be hydrogen specific with an appropriate split between immediate and delayed ignition carefully considered. The DNV hydrogen QRA guideline includes state-of-art ignition probability models to be applied.
Jet fire modelling
One key area of work in Phast and Safeti is the inclusion of the Miller jet fire model. This was introduced in Phast and Safeti 8.6 and became the default for hydrogen vapour releases in Phast and Safeti 8.9. Developed by Derek Miller at Air Products, this model enhances predictions of thermal radiation from hydrogen jet fires. It represents the flame as a line source with two segments, accounting for uplift and wind, leading to more accurate predictions for vapour hydrogen jet fires. Validation has shown the Miller model produces good radiation predictions for vapour hydrogen jet fires, as shown below for horizontal hydrogen jet fires.
Explosion modelling
A hydrocarbon-air mixture ignited in an open area will burn relatively slowly with little overpressure generation – this is termed a flash fire. Congestion from large amounts of process equipment and piping can cause turbulence in the burning flame front, leading to high flame speeds and hence explosion. Alternatively, if the combustion is confined (e.g. in a building), the combustion gases cannot expand and the pressure increases, causing an explosion.
For hydrogen, the situation is different. Experiments have shown that the turbulence of a jet release alone is sufficient to create the conditions for an explosion. Therefore, explosions must be modelled, even outside of confined and congested regions.
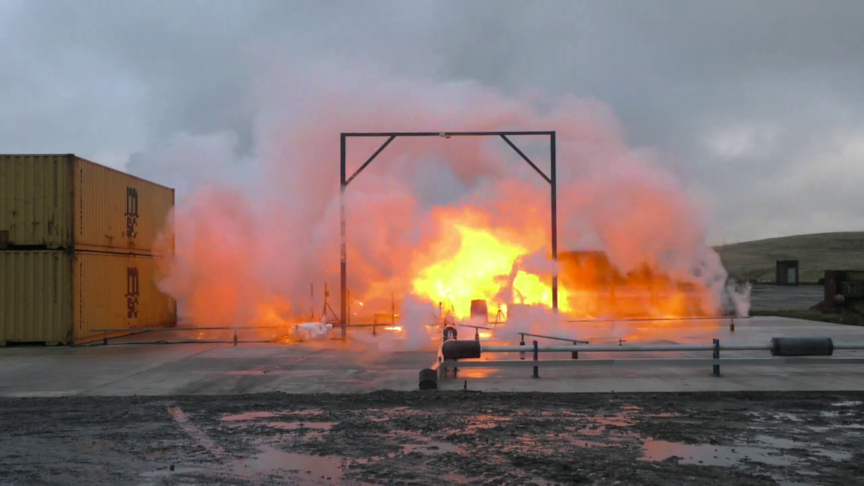
Perhaps the most dramatic difference with hydrogen is the potential for detonation. There are two types of explosions, deflagrations and detonations. In a detonation, the flame front moves at greater than the speed of sound. The pressure rise is sharper, and the peak pressure is higher. Importantly, the shock wave can cause compression and auto-ignition of the fuel ahead of the flame front, leading to the entire flammable mass of the cloud contributing to the explosion, without the need for further congestion or other means of flame front acceleration.
The QRA model must take detonation effects into account or else it will severely underestimate the risk.
Regulatory framework and standards
As hydrogen technologies evolve, the regulatory frameworks and standards that govern them will evolve as well. Currently, updates to Seveso are under consideration due to reviews of new technical knowledge, changes in industrial practices, and lessons learned from recent accidents integrating the Seveso Plants Retrieval System (eSPIRS) into the Global Disaster Alert and Coordination System. This has been done to improve prevention, preparedness, and response to major industrial accidents and additionally aligning with broader EU initiatives like the European Green Deal. Plants are also covered by other EU directives that rely on risk assessments and where guidelines are being developed and National regulations develops in parallel to deliver goal setting and prescriptive requirements.
8/30/2024 8:45:00 AM