Emerging carbon capture techniques in cement plants
Carbon dioxide (CO2) production is inherent to the cement manufacture process. The gas is formed chemically and thermally as well as through indirect emissions such as electricity use.
Typically, the chemical reaction involved is responsible for the greatest proportion of the overall CO2 emissions.
As part of the global transition to net zero, many cement manufacturers are seeking to decarbonize. The methods proposed generally fall into the following categories:
- reducing indirect emissions by using decarbonized electricity
- increasing thermal energy efficiency to reduce fuel usage
- switching to low carbon fuels (both in the process and in transport)
- using alternative raw materials (substitutes and supplements to natural resources)
- reducing the clinker-to-cement ratio
- carbon capture, utilisation and storage.
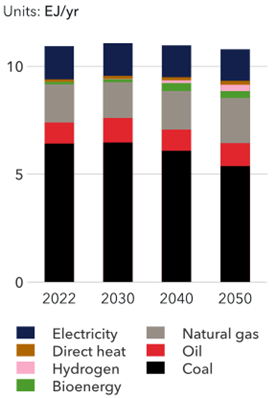
The adoption of alternative fuels in the cement industry is examined in DNV’s 2023 Energy Transition Outlook, which presents a single ’best estimate’ forecast of the energy future (see Figure 1). In 2030, 2040 and 2050, the roles of hydrogen and electrification in the cement industry are expected to remain limited, with conventional hydrocarbons remaining the dominant energy source. Due to the high-temperature requirements and the necessity of an emissions abating process regardless of the fuel used, carbon capture is expected to play a significant role in cement industry decarbonization.
Post-combustion carbon capture
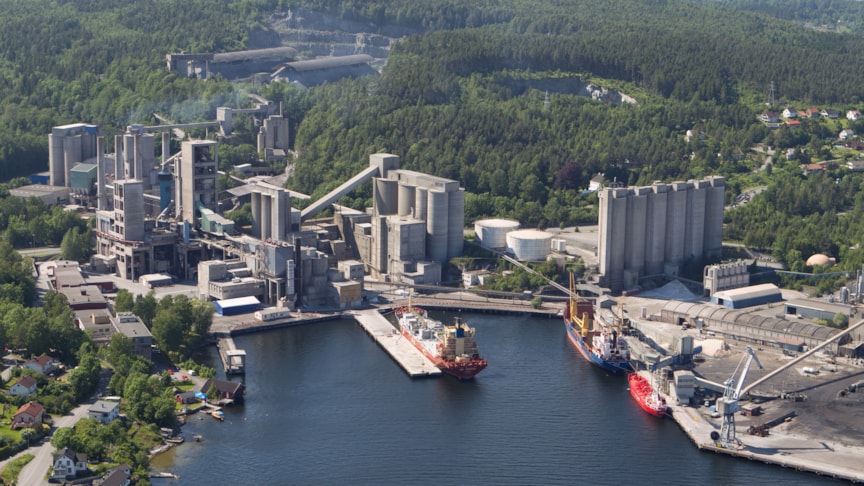
Post-combustion capture of CO2 using amine-based solvents is an end-of-pipe technology. The approach does not directly affect the cement manufacture process, and is able to tackle both combustion and process emissions. The technique has been adopted by Norcem’s Brevik cement plant in Norway, and the plant’s carbon capture facility is currently under construction (see Figure 2).
The large-scale plant will be the first of its kind equipped with CCUS and is scheduled to begin operation in 2024, storing captured carbon via the country’s Northern Lights facility. The flue gas from cement production varies in chemical composition, and is heavily dependent on the fuels and materials used. It can be a challenging application for solvents used in post-combustion capture. To address such challenges novel amine-based solvents with lower degradation rates, such as that provided by Aker Carbon Capture for the Brevik cement plant, have been developed.
Pre-combustion technologies
In the cement sector, pre-combustion carbon capture technologies would have limited mitigation potential as they could only deal with energy-related CO2 emissions. They might be of use in new cement plants integrated with gasification technologies to produce syngas or hydrogen. However, new and more efficient hydrogen burners and cement kiln lines would be required.
Oxyfuel combustion
An alternative approach is the combination of oxyfuel combustion with CO2 separation. Oxyfuel combustion uses pure oxygen (separated from air) to maintain combustion conditions whilst typically recirculating exhaust gases to the burner to reduce flame temperatures. The removal of atmospheric nitrogen from the combustion process both reduces NOx emissions and the overall volume of flue gases, thereby leading to higher concentrations of CO2 in the flue stream. This reduces the CO2 separation plant’s complexity and size. Oxyfuel combustion improves the efficiency of the combustion process and clinker throughput, but the required addition of an air separation unit adds complexity and cost. Oxyfuel combustion involves different thermochemical processes and, as such, cannot be easily retrofitted to existing plants. However, it is an approach which may be promising for new facilities.
Calcium looping
Another alternative approach is calcium looping, sometimes known as the regenerative carbon cycle (RCC). Here, a calcium oxide (CaO) sorbent is used in two reversible reactions: carbonation and calcination. During carbonation, calcium oxide reacts with CO2 in the flue gases to form calcium carbonate. A calciner is then used to decompose the calcium carbonate, generating CO2 and calcium oxide. The latter can then be re-used in the process.
One of the main challenges with this technique is the degradation of the calcium oxide over time, requiring replacement. However, the waste sorbent can be used in cement manufacture, reducing raw material costs. Another attractive feature of this technology is that it can be retrofitted to cement plants and offers potential for high levels of integration of waste heat – increasing efficiency.
Direct capture of process emissions
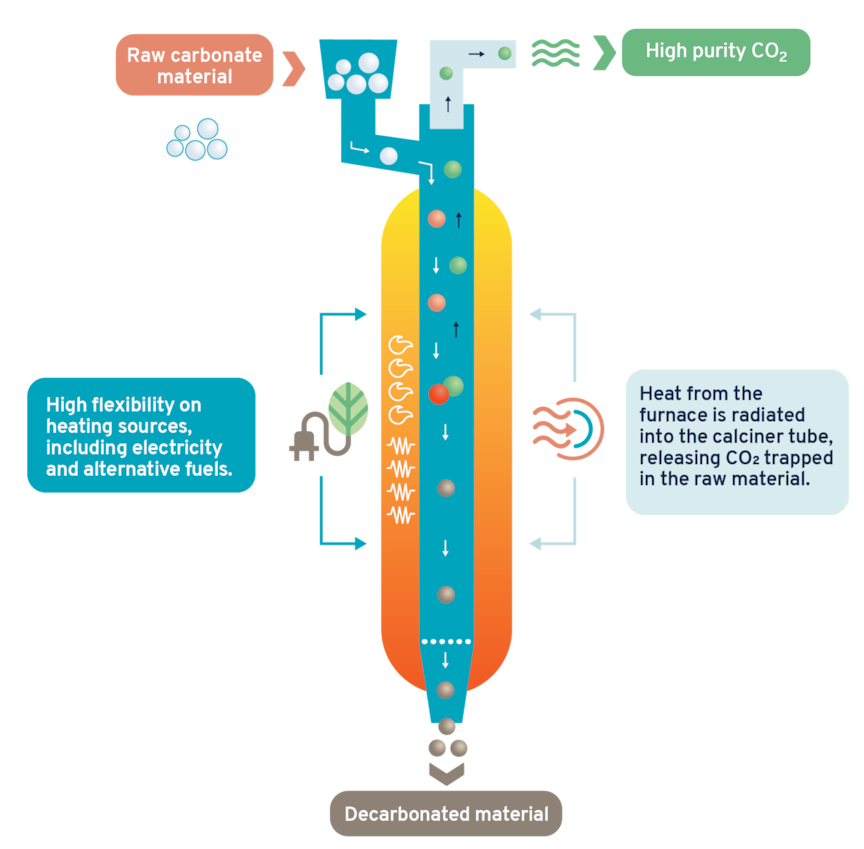
Direct capture of process emissions has been developed by Calix who created and patented an indirectly heated calcination technology. The Low Emissions Intensity Lime and Cement Project, known as LEILAC, is based on indirect calcination by heating the limestone using a direct separator reactor (DSR) within a novel ‘precalciner’ (see Figure 3). The external surface of the DSR is heated using natural gas or electricity. Raw meal is dropped at the top in the interior of the DSR, through conductive and radiative heat transfer from the reactor wall, this material is calcined and releases CO2.
Limestone calcination is isolated from the fuel combustion, enabling pure CO2 to be captured as it is released. The LEILAC-1 project involved the construction of a pilot plant at Heidelberg Materials in Lixhe, Belgium. The project had a CO2 capture capacity of 25,000 tpa. Work commenced on LEILAC-2 in April 2020, having been awarded EUR16m in funding by the European Union’s Horizon 2020 programme for the construction of the demonstration plant. It is set to be a scalable module, integrated with the Heidelberg Materials plant in Hannover, Germany.
Carbon utilisation
While efforts today are often focused on the capture of CO2 for subsurface storage, there are various utilisation options that can offer a high degree of permanence that the cement industry is well poised to take advantage of. One such technique is Accelerated Carbonation Technology, developed by Carbon8, which mineralises CO2 with residues produced on site to manufacture aggregates which can then be used within the construction industry. Such techniques step around the need for CO2 transport and storage infrastructure, which is sometimes not available near cement plants, and can reduce the level of CO2 conditioning required.
To the future
Given the process emissions inherent to the cement manufacture process, it is difficult to see how the cement industry can decarbonize without the use of CCUS techniques. A growing number of carbon capture projects on cement plants are emerging, particularly in regions where there is supportive policy such as in North America and Europe.
Today, the industry is supporting research and development of a wide variety of carbon capture techniques, efforts that are likely to lead to technology improvements and cost reductions that will enable wider deployment in future.
This article was first published in International Cement Review 2024: www.CemNet.com.